Table of Contents
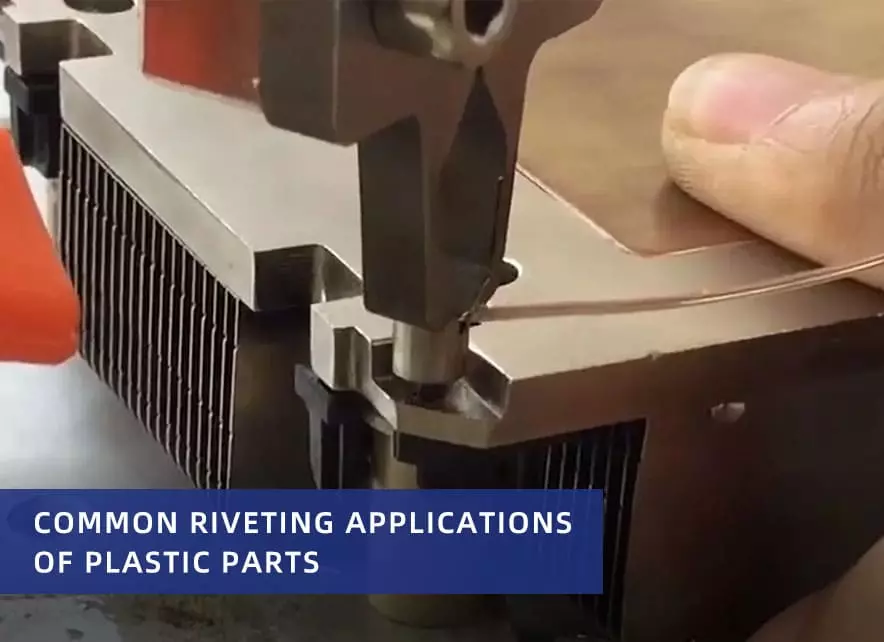
Plastic products flood our lives. That’s why it’s important for manufacturers to consider faster and simpler connections. And riveting plastic offers an excellent solution.
By using riveting to install plastic products, you can increase your productivity by up to 30%! Let’s discover its secrets!
Table of Contents
What is Plastic Riveting?
Nowadays, plastic is an indispensable material in people’s lives. So how manufacturers can install plastic products more quickly is one of the issues people need to pay attention to.
Plastic riveting is a fastening method used to permanently join plastic materials. This method uses rivets to hold two or more plastic parts together. It is widely used in automotive, electronics, home appliances, medical devices, toys and other industries.
Plastic riveting allows for the installation of a combination of different materials, such as plastic + plastic or plastic + metal. Therefore, riveting can provide a high-strength, vibration-resistant, lightweight fastening solution for plastic product manufacturers.
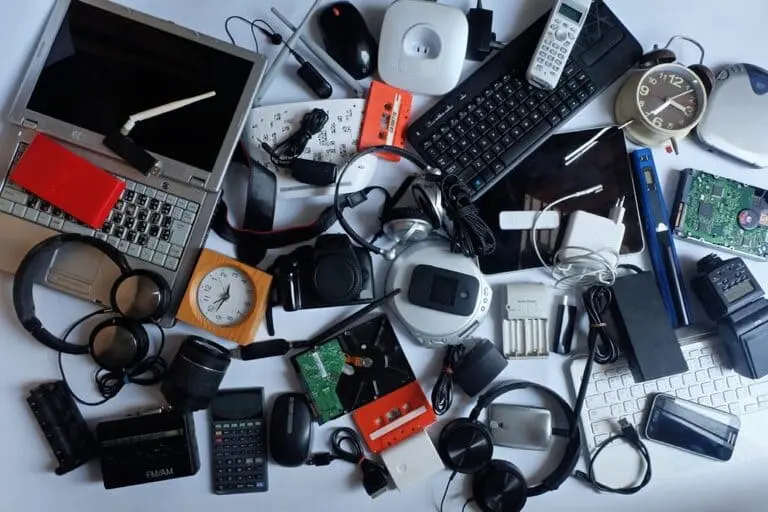
5 Benefits of Riveting Plastic
There are many types of fasteners that can be used to install plastic materials, and in the assembly of plastic products, Pop Rivets provide an efficient, stable and durable connection. If your project requires riveting plastic to metal, riveting solutions can deliver exceptional results. Pop rivets offer significant strength, durability and efficiency advantages over screws, glue or welding.
1. For connections between plastics and metals or plastics
In the actual production process, plastics are combined with plastics or metals. For example, automobile dashboards, electronic equipment housings, appliance housings, etc.. And Blind Rivet can realize the fastening of these heterogeneous materials, and will not cut threads on the plastic like screws, resulting in plastic deformation or cracking.
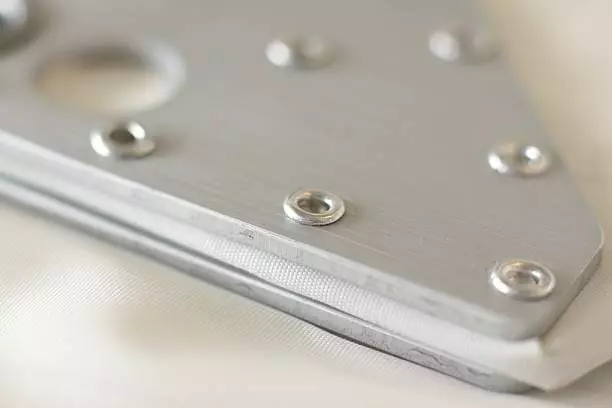
Common riveting scenarios for plastics are listed below:
- Plastic + Plastic Connections: Electronic equipment housings, plastic product assemblies
- Plastic + metal connection: automotive interior parts, medical device brackets, appliance fixing components
- Plastic + Composite Material Connection: Lightweight structural parts
2. No need for threads to avoid plastic damage
The plastic is softer for metal. When you use a screw on a plastic product, the threads of the screw are likely to damage the internal structure of the plastic, causing it to loosen or break. And the core-pulling rivets do not need to cut the threads, which can effectively prevent the following situations from happening:
- Plastic cracking (especially brittle plastics such as PC, ABS)
- Loosening after long-term use (threaded connections are prone to loosening due to vibration or temperature changes)
- Deformation of plastics due to over-tightening
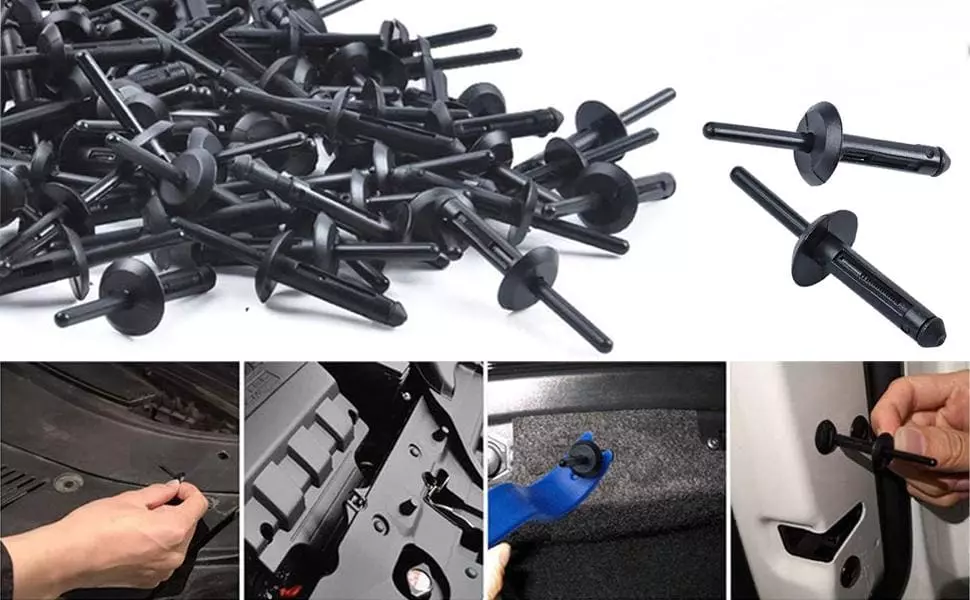
Therefore, in the actual application process, the emergence of blind rivets in plastic products is still very frequent.
- Plastic shells of household appliances (washing machines, vacuum cleaners, televisions)
- Medical equipment (blood pressure monitors, electronic testing instruments)
- Sports equipment (skis, plastic frame connection)
3. High connection strength, shock and vibration resistance
Compared to other fasteners, the connection of a blind rivet is permanent and will not loosen. The performance of blind rivets is excellent in applications where they are subjected to vibration, shock and vibration. For example, automotive parts, power tools, electronic equipment, these scenarios, rivets in the riveted, rivet tail expansion to form a fastening structure, can effectively disperse the stress and improve the overall strength of the connection.
The advantages of blind rivets in these applications are as follows:
- More vibration-resistant than screws: screws gradually loosen under prolonged vibration, while rivet connections will not come loose.
- Impact Resistant: Plastic products can be subjected to impact during transportation or use, and rivets are stronger than bonded or snap fasteners.
4. Suitable for mass production
As we all know, the biggest advantage of blind rivets is that they are very easy and fast to install. Therefore, in industrial production lines, riveting is more efficient than screws or glue. Automated riveting equipment can improve efficiency and reduce manual errors in assembly line operations.
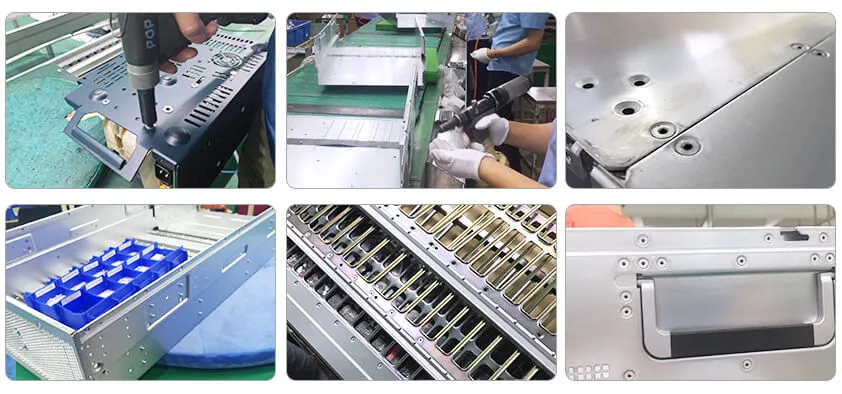
For manufacturers, blind rivets offer unparalleled production advantages.
- Faster than screws: screws need to be tightened, rivets are fixed in one pass.
- Can be automated: Riveting can be done quickly by robots or pneumatic rivet guns.
- Lower labor costs: no screws to tighten, reducing assembly time.
5. A variety of rivet materials can be selected to meet different needs
Different plastic products have different performance requirements, you can choose different material rivets to adapt:
- Nylon rivets (Plastic Rivets): for all-plastic structures, light weight, non-conductive, suitable for electronic equipment.
- Aluminum rivets (Aluminum Rivets): lightweight, suitable for plastic + metal structures, such as appliance housings.
- Stainless Steel Rivets (Stainless Steel Rivets): high strength, suitable for automotive, medical equipment, outdoor equipment.
Do You Have Any Questions?
Let Us Solve Your Problem
How to Riveting Plastic?
For riveting to be perfect, you need the right riveting plastic. Here is the proper procedure for riveting plastic.
1️⃣ Select the right rivets (plastic, aluminum, exploding rivets, etc.)
2️⃣ Measure & mark drill locations to ensure even distribution
3️⃣ Secure the plastic plate, use a low speed drill to drill and deburr the holes.
4️⃣ Insert rivets and apply force with a suitable rivet gun.
5️⃣ Check the quality of the rivets and fix possible wrong rivets.
6️⃣ Clean up the work area and make sure that the riveted surfaces are clean and presentable.
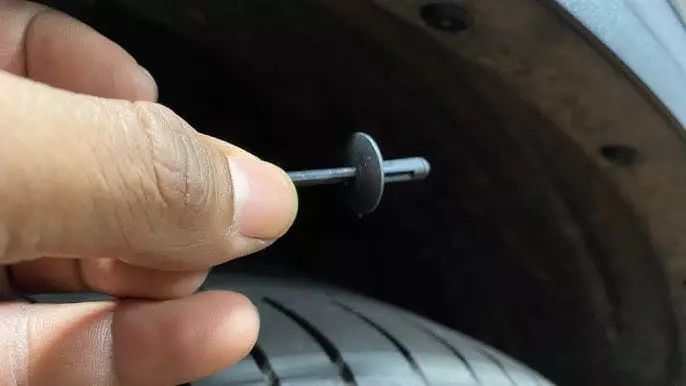
point of attention
It is important to note that choosing the right type of rivet is important. This will have a direct impact on the safety of your product. According to the type of plastic, connection strength, environmental needs to choose the right type of rivets:
- Plastic rivets (Nylon Rivets): lightweight, non-conductive, suitable for electronic equipment, automotive interiors.
- Aluminum Blind Rivets: suitable for plastic + metal connections, such as appliances, automotive components.
- Stainless Steel Blind Rivets : for corrosion-resistant, high-strength requirements of the application, such as medical equipment, outdoor plastic parts.
- Exploding Rivets: Rivets with an expanding tail for brittle plastics to prevent cracking.
Frequently Asked Questions about Riveting Plastics
In the process of riveting plastics, it is inevitable that some problems will occur. Below I have listed the common problems as well as their causes and corresponding solutions.
Cracking of Plastic
When riveted, the plastic may crack or rupture when the rivet tail expands. There are generally two reasons for this: 1. The riveting force is too great for the plastic to withstand the pressure. 2. The plastic is too brittle.
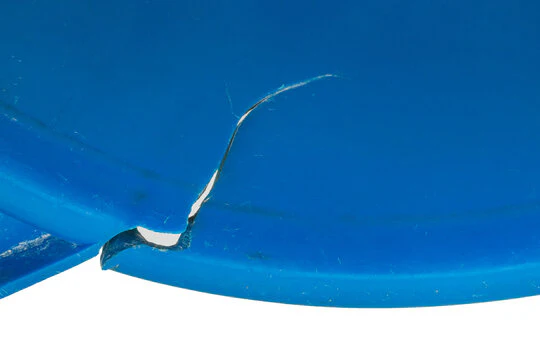
Solutions:
✔ Select Exploding Rivets or Nylon Rivets to reduce stress concentrations.
✔ Reduce the pressure of the rivet gun to avoid over-expansion of the rivet tail.
✔ Add shims (e.g. rubber washers) to the riveted parts to disperse the stress.
2. Loose or Spinning Rivet
If there is a rivet that is loose or rotatable inside the plastic, this will generally result in an unstable connection. There is a risk of detachment if exposed to vibration for a long period of time.
The possible causes are listed below:
❌ Drill holes are too large for the rivet to fit tightly into the plastic.
❌ The tail of the rivet is not sufficiently expanded, resulting in a poor fixing.
❌ The thickness of the plastic is too thin for the rivet to develop sufficient clamping force.
Solution
✔ Select larger diameter or longer rivets to ensure full tail spread.
✔ Switch to Multigrip Rivets (Multi Clamp Range Rivets) to accommodate different thicknesses of plastic.
✔ Add washers inside the plastic to increase clamping force and improve stability.
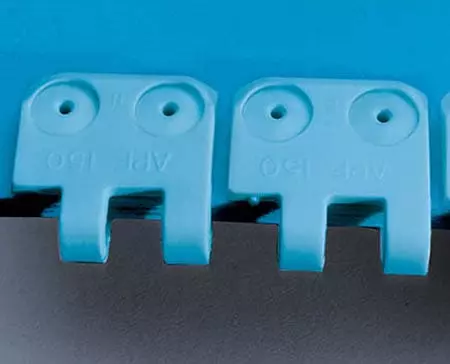
Plastic Deformation
In thin-walled plastic or soft plastic (e.g. PP, PE) products, after riveting, bulging, denting and bending of the plastic sheet may occur, which seriously affects the appearance and function of the plastic product.
Possible causes
❌ The riveting force is too high and the rivet is over-expanded causing the plastic to deform under pressure.
❌ The plastic sheet is too thin to withstand the riveting pressure.
❌ No support material is used and the plastic lacks sufficient rigidity.
Solution
✔ Select short rivets or low expansion rivets to minimize deformation.
✔ Add shims or metal supports to increase the rigidity of the plastic.
✔ Use a low-pressure rivet gun or manual rivet gun to reduce riveting stress.
Do You Have Any Questions?
Let Us Solve Your Problem
Riveting Plastic vs Screwing vs Adhesive Bonding
Riveting, Screwing and Adhesive Bonding are three common mechanical or chemical fastening methods used in the assembly of plastic products. Different application scenarios have different needs, here is my summary.
- For high-strength, long-term stable non-removable connections → Riveting
- For a removable, easy-to-maintain connection → Select Screwing.
- For aesthetically pleasing connections without exposed fasteners → Adhesive Bonding
In most industrial production, automotive manufacturing, appliance assembly, etc., riveting technology is usually the better choice due to its high strength, durability, and suitability for automated production. Screw joining is suitable for electronic products that require maintenance, while glue bonding is suitable for high-end consumer electronics and specialty applications.
Custom Riveting Solutions for Your Plastic Projects
At Rivmate, as a leading rivet manufacturer, we have provided the perfect riveting solution to hundreds of customers around the world. Trust us to provide customized riveting solutions for your plastic products.
By selecting the optimal rivet type (plastic, aluminum, exploding rivets, etc.) and combining it with precise drilling control and automated riveting processes, we optimize the assembly process to increase product durability and productivity. Whether it’s a plastic + plastic or plastic + metal connection, we have a fastening solution to fit your product needs. If you have assembly needs for plastic components in automotive, electronics, home appliances or medical devices, please contact us for professional, efficient and customized riveting technical support!
Get Rivets Quote
You may also find these topics interesting
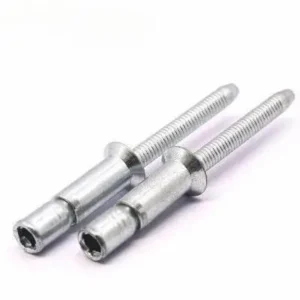
What is the Difference Between Countersunk Rivets and Regular Rivets? – Rivmate Expert Guide
What is the Difference Be