What Are Black Anodized Pop Rivets and Their Uses?
Table of Contents
Black Anodized Pop Rivets are blind rivets with a special surface treatment. It is anodized to form a dense black oxide film on the surface of the rivet. This not only enhances its corrosion and wear resistance, but also gives it a good decorative effect.
The application of this type of Rivets not only meets the basic needs of structural fixing, but also emphasizes the combination of aesthetics and durability. With the market’s emphasis on product appearance details and long-term performance, black anodized Rivets have become the Rivets choice for many engineers and product designers in the selection process. In this article, we will discuss its working principle, typical application scenarios and how to select the right type, in order to help you introduce it into the assembly system more efficiently.
what are black anodized pop rivets?
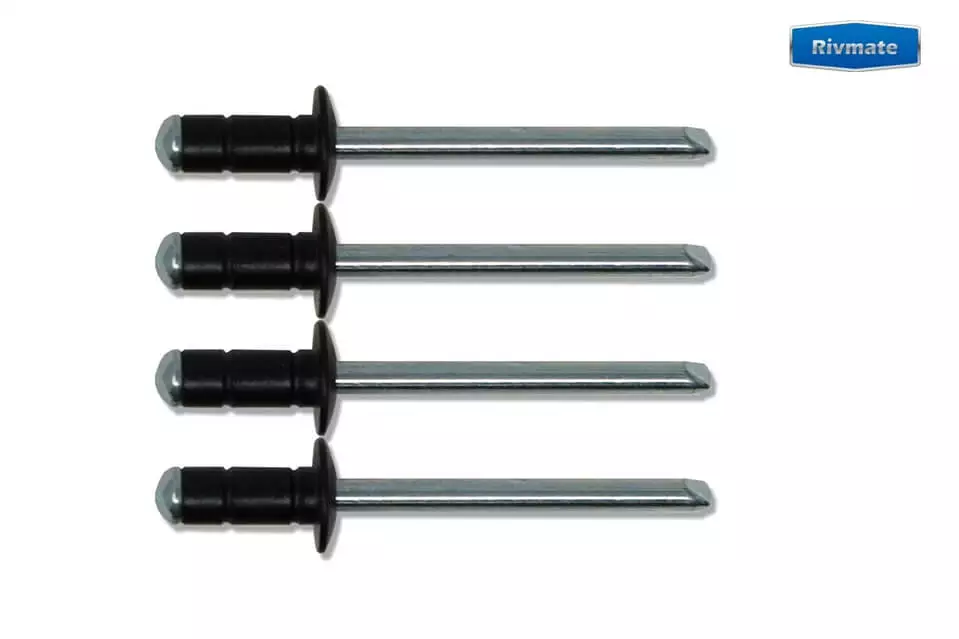
Black Anodized Pop Rivets are an anodized and blackened aluminum blind rivets. This type of rivet combines mechanical properties, corrosion resistance and aesthetic appearance. They are used in a wide range of scenarios where a structural connection + a black decorative effect is required. Examples include aluminum panels, black equipment housings and outdoor structures that require long-term weathering performance.
Black anodized pop rivets can not only meet the basic needs of structural connection, but also significantly improve the consistency and durability of the overall appearance of the product. Its anodized layer forms a dense, wear-resistant, corrosion-resistant oxide film, and the black color is very stable and not easy to fade.
What does black anodizing do on blind rivets?
Black anodizing enhances the corrosion and abrasion resistance of blind rivets and gives them a consistent, attractive and durable finish.
- Enhanced corrosion resistance: Anodizing treatment will form a dense oxide film on the surface of the rivet body, which can effectively block the erosion of air, moisture and chemical media.
- Enhance the surface hardness and abrasion resistance: the oxidized layer has high hardness, with good scratch resistance and impact resistance.
- Provide decorative black appearance: achieve the visual effect of consistent color tone and professional texture.
- Improves surface performance: the oxide film acts as an insulating layer, preventing the risk of galvanic corrosion or short circuits.
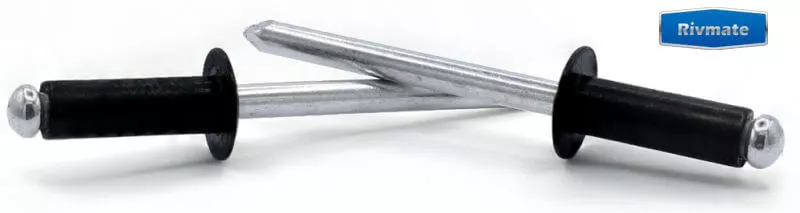
Black anodizing gives the blind rivet both cosmetic and functional advantages. It provides not only high performance in structural connections, but also a high degree of visual harmonization, meeting both industrial and aesthetic needs.
In terms of appearance, black anodizing creates a matte or semi-gloss uniform black surface with a calm tone and strong texture. Therefore, it can be perfectly integrated into ferrous metals, electronic equipment cases, architectural curtain walls and other application environments, realizing the consistency and professionalism of product appearance.
Functionally, the anodized layer has excellent corrosion resistance, oxidation resistance and surface hardness. Therefore, it can effectively resist water vapor, salt spray, friction and scratches, significantly extending the service life of rivets in outdoor, humid or industrial environments. It also provides a level of electrical insulation that makes it safer and more reliable in electronic and electrical structures.
Process characteristics of black anodized Pop rivets
Black anodizing is a common surface treatment for rivets, the main purpose is to enhance their corrosion resistance, aesthetics and a certain degree of hardness. The following is a typical black anodizing process:
1. Pre-treatment
- Degreasing and degreasing: Use alkaline cleaners or solvents to remove surface oils and impurities.
- Water rinsing: Neutralize residual lye to prevent contamination from subsequent treatments.
- Alkaline or acid etching (optional): Uniformly removes oxidized layer and creates a rough surface that helps film adhesion.
2. Anodizing
- Electrolyte: Sulfuric acid solution (15-20%) is usually used.
- Voltage/current control: Maintained between 12-20 volts, adjusted according to material thickness.
- Temperature control: Maintained at 15-25°C to obtain a dense and uniform oxide film.
- Anode polarity: workpiece is connected to the anode, the cathode is mostly lead or stainless steel plate.
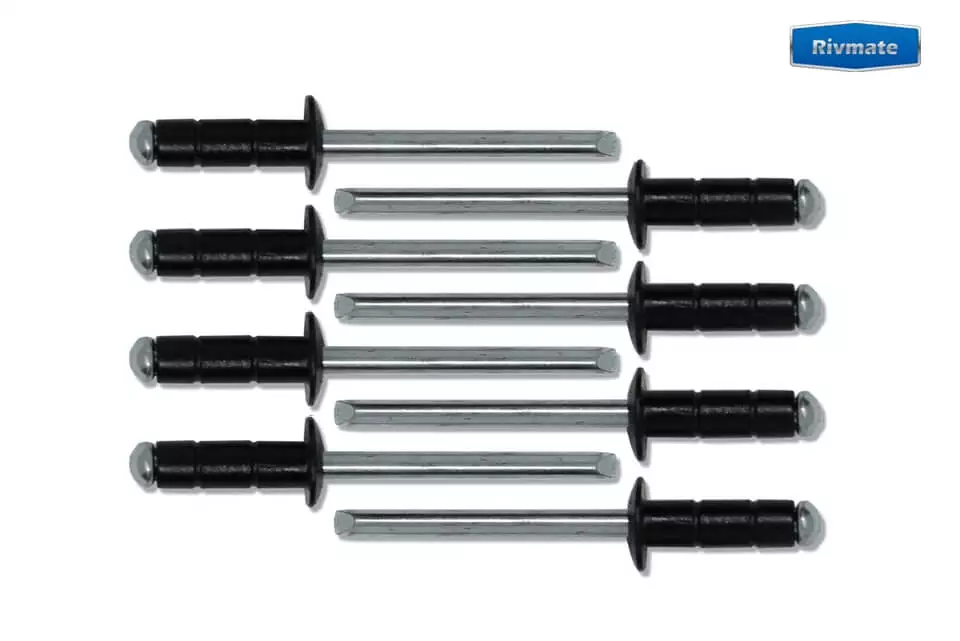
3. Black dyeing
- Dye type: organic dyes (such as acid black) or inorganic dyes (such as iron salt precipitation method).
- Time control: immersion time to control the depth of dyeing, often 5-15 minutes.
- Temperature and pH: Generally, the temperature of the dyeing bath is 40-60°C, and the pH should be kept stable to ensure uniform dyeing.
4.sealing
In order to close the pores of the oxide film, prevent the dye from seeping out and improve the corrosion resistance of the rivets. Rivet manufacturers commonly use hot water sealing, nickel salt sealing or nano sealing liquid. The rivets are sealed in hot water at 95-100°C for 10-30 minutes.
5. Drying and quality inspection
Finally dry the rivets using hot air or naturally. Then check the rivets for color uniformity, film thickness (usually 10-25 microns), adhesion, and corrosion resistance.
The principle of black anodizing to enhance the hardness and corrosion resistance of rivets
Black painted rivets provide protection and aesthetics by physically covering the surface with a coating layer such as powder or paint. The coating has good adhesion and weathering resistance, which is especially appropriate for aluminum rivets or applications that require a customized appearance. Spraying creates a thick, uniformly colored film that is resistant to UV light and humidity, but is prone to flaking or cracking in areas of high friction or mechanical deformation.
Black plated rivets, on the other hand, use electrochemical deposition of a layer of metal (such as zinc, nickel) and black passivation treatment, forming a dense and firmly attached metal protective layer. Its advantage lies in good wear resistance and low-cost batch processing capability, especially for carbon steel rivets, but not for aluminum, and the black plating layer in long-term outdoor use may fade or passivation layer degradation.
Sprayed Black Rivets vs Electroplated Black Rivets
Category | Black Painted Rivets | Black Electroplated Rivets |
---|---|---|
Surface Treatment | Powder or liquid paint coating, cured with heat to form a protective layer | Electrochemical deposition of metal (e.g., zinc, nickel) followed by black passivation |
Adhesion Mechanism | Physical adhesion, dependent on surface prep and curing | Electrochemical bonding, strong metal-to-metal adhesion |
Base Material Suitability | Suitable for aluminum, steel, stainless steel | Primarily for carbon steel; not suitable for aluminum |
Corrosion Resistance | Good, with sealed coating preventing moisture ingress | Excellent, especially with black zinc + sealing combinations |
Wear Resistance | Moderate; coating is thick but may scratch or wear | High; metal plating offers greater surface hardness |
Coating Thickness | Thick (60–100 μm), easily adjustable | Thin (5–15 μm), limited to prevent brittleness |
UV/Weather Resistance | Good (especially polyester powder); suitable for outdoor use | Moderate; black passivation may fade over time |
Appearance Uniformity | Even coloration; available in matte, gloss, and textured finishes | Prone to slight color variations or flow marks |
Defect Coverage | Can mask surface imperfections | Requires high surface prep; flaws are more visible |
Deformation Tolerance | Coating may crack or peel under mechanical deformation | Good; plating remains intact under forming or riveting stress |
Unit Cost | Medium to high, especially for small batches or multicolor requirements | Low; cost-effective for high-volume standard fastener production |
Environmental Impact | Powder coating is VOC-free and environmentally friendly | Electroplating involves heavy metal wastewater, requiring robust treatment |
Recommended Use Cases | Aluminum rivets, decorative or exposed parts, outdoor applications, custom finishes | Carbon steel rivets, high-volume runs, cost-sensitive or wear-critical applications |
Why choose black anodized pop rivets?

- Enhanced corrosion resistance: Anodizing treatment forms a dense oxide film, which significantly improves the corrosion resistance of the rivets. Compared with ordinary rivets, black anodized pop rivets have a longer service life.
- Consistent Appearance and Enhanced Product Value: Black anodized pop rivets are visually compatible with most industrial products or structural components, avoiding the abruptness caused by silver colored rivets. For users, this means higher end-product aesthetics and professional image.
- Less susceptible to discoloration: Compared to painting or dyeing processes, anodized colors are more stable and less likely to fade, flake or contaminate surrounding surfaces.
- Balancing strength and lightweight: Anodizing allows rivets to be strong enough to be used while maintaining a lightweight design.
applications of black anodized pop rivets
Black anodized pop rivets are used in industrial and consumer applications where uniformity of appearance, harsh environmental conditions, or long-term durability are required.
- Electronic and electrical equipment manufacturing: server chassis, power supply boxes, audio equipment, surveillance camera housings, etc.
- Architecture and curtain wall system: aluminum alloy window frames, curtain wall panels, metal decorative panels, facade sunshade system
- Automotive and motorcycle parts: interior trim panels, dashboard brackets, fenders, body sheet metal edges and corners.
- Consumer electronics products: black metal shell cell phone bracket, TV bezel, tablet shell fixed
- Security and lighting equipment: road camera shells, infrared lamps, outdoor LED lighting assembly
- Aerospace and rail transportation lightweight components: interior trim parts, wire harness brackets, antenna covers, cabin trim panels
- Military & Tactical Equipment: Tactical Cases, Portable Devices, Drone Housings, Night Vision Devices
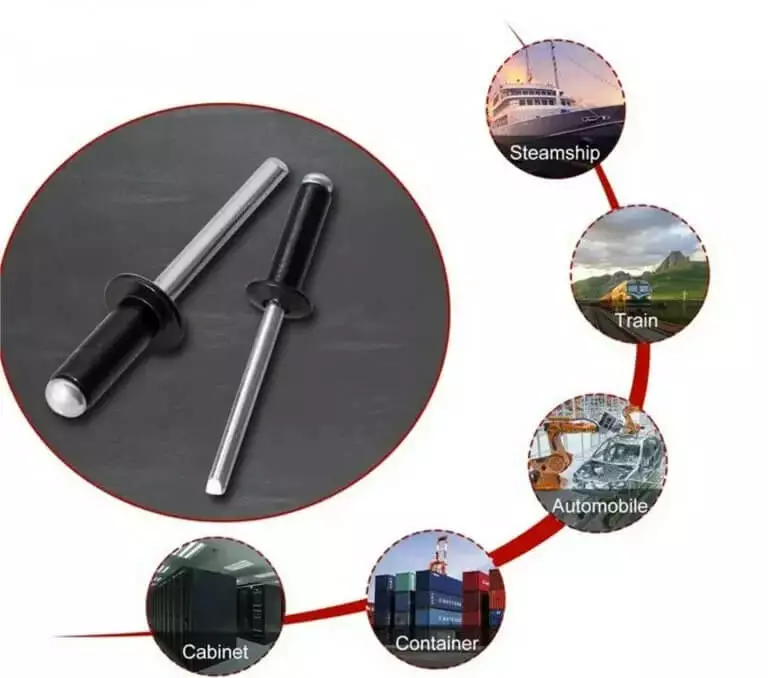
Best black anodized pop rivets pick and match advice
In practical applications, the selection of the best Black Anodized Pop Rivets should take into account the substrate material, environmental conditions, load requirements and appearance consistency. The following is a list of recommended options:
Application Scenario | Recommended Rivet Body Material | Mandrel Material | Diameter (Typical) | Grip Range | Key Advantages |
---|---|---|---|---|---|
Indoor Electronics (Chassis, Panels) | Aluminum (Black Anodized) | Aluminum | 3.2mm / 4.0mm | 1.0–6.0mm | Lightweight, aesthetic, easy to install |
Outdoor LED Fixtures, Camera Housings | Aluminum (Black Anodized) | Stainless Steel | 4.8mm | 1.5–9.5mm | Corrosion-resistant, outdoor-ready |
Building Facades / Cladding Systems | Aluminum (Black Anodized) | Stainless Steel | 4.8mm / 6.4mm | 3.0–12.0mm | High strength, visual uniformity |
Automotive Interiors / Bracket Mounting | Aluminum (Black Anodized) | Steel | 4.0mm | 1.0–5.0mm | Balanced strength and cost control |
Outdoor Structural Components | Stainless Steel (Black Coated) | Stainless Steel | 4.8mm / 6.4mm | 4.0–10.0mm | Maximum durability, excellent corrosion resistance |
Consumer Electronics (Visible Assembly) | Aluminum (Black Anodized) | Aluminum | 3.2mm | 1.0–3.5mm | Excellent appearance, tight color control |
Other Selection Points:
- Color difference control: Prefer batch anodizing, control the thickness of oxide film within 10-15μm, to ensure the stability of color difference.
- Clamping material matching: avoid electrochemical corrosion, aluminum with aluminum/stainless steel with stainless steel is preferred.
- Matching of installation tools: Match with appropriate manual or pneumatic rivet guns to ensure clean core breakage and avoid affecting the appearance.
Why do we recommend black anodized pop rivets?
Black Anodized Pop Rivets combine corrosion resistance, high strength and an attractive black appearance. Black anodized blind rivets are an excellent choice if your business or riveting project requires a uniform appearance and long-term durability. In applications such as electronic equipment, architectural finishes and outdoor structures, the anodized finish of black anodized pop rivets ensures that the color will not fade or flake, enhancing the overall product quality and longevity.
For matching suggestions, sample testing or technical support, please contact us. We can provide standard or customized solutions for your application, helping to optimize assembly efficiency and costs.
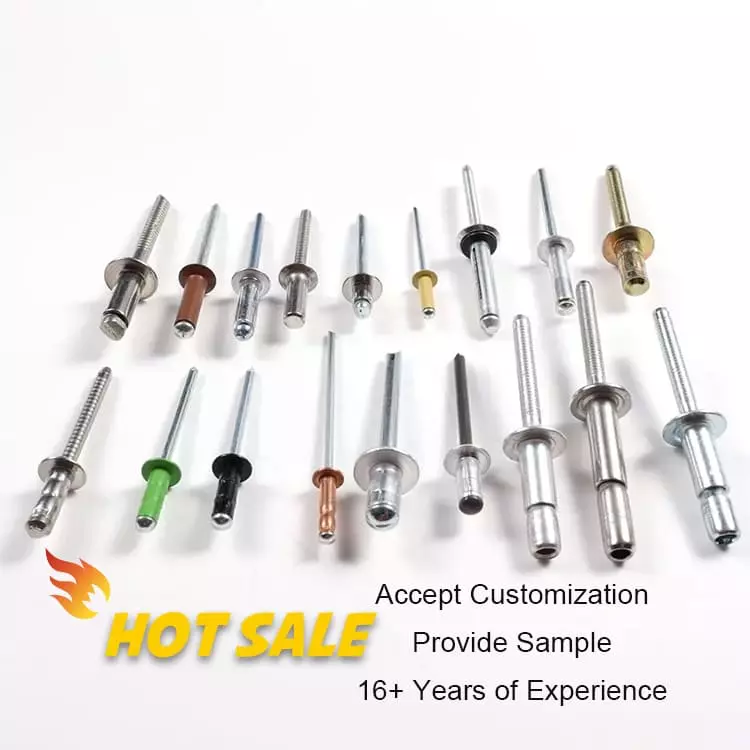
Share:
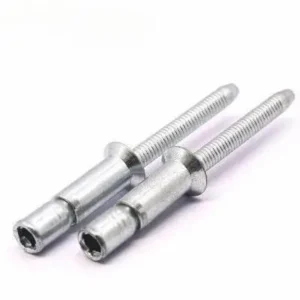
What is the Difference Between Countersunk Rivets and Regular Rivets? – Rivmate Expert Guide
What is the Difference Be
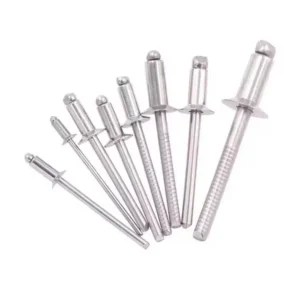
What are Countersunk Blind Rivets Used for?
What are Countersunk Blin
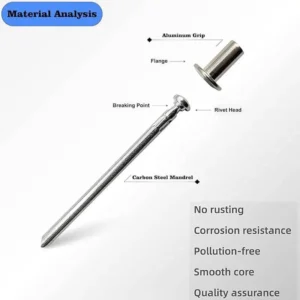
Problem with Rivet Mandrel Breaking
Problem with Rivet Mandre
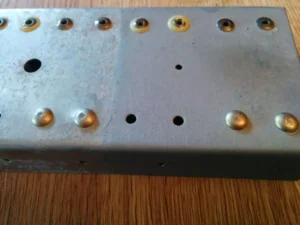
Rivet Corrosion: Causes, Prevention, and Engineering Solutions
Rivet Corrosion: Causes,