Table of Contents

How Do I Choose The Right Size Pop Rivet? Do you know what factors you should base your choice of the most suitable pop rivets on? Are you overwhelmed by all this, don’t worry, this article will solve all your questions about how do i choose the right size pop rivet!
Table of Contents
How to Choose The Right Size Pop Rivet for Your Project?
Choosing the right size pop rivets for your project is very important. The right pop rivets can ensure the success of your project! So, how should we choose the right pop rivets for your project? Please read the following carefully and trust me, you will get the answer you want!
1. Determine the Thickness of the Material
Before choosing the size of the pop rivets, you need to check the total thickness of the material being joined. Thickness here refers to the total thickness of all the materials to be joined, this includes the thickness of any overlays or coatings.
For example, if you need to join two sheets, each of which is 1.5mm thick, then the total thickness of the two sheets would be 3mm.
2. Select Pop Rivets Diameter

How do you choose the best diameter for pop rivets? You need to evaluate the load requirements.The diameter of the pop rivets directly affects the strength and durability of the connection. Let’s read on.
Load Requirements
There are two general types of loads: shear and pullout. These two force types represent the lateral and axial forces to which pop rivets are subjected, respectively.
- Shear force: the force generated by the relative sliding between two pieces of material
- Pulling force: the force generated by two pieces of material trying to separate.
Common application scenarios for load strength are listed below:
- Low load applications: joining of lightweight plastics or thin metal sheets
- High load applications: Heavy metal structures or high stress areas
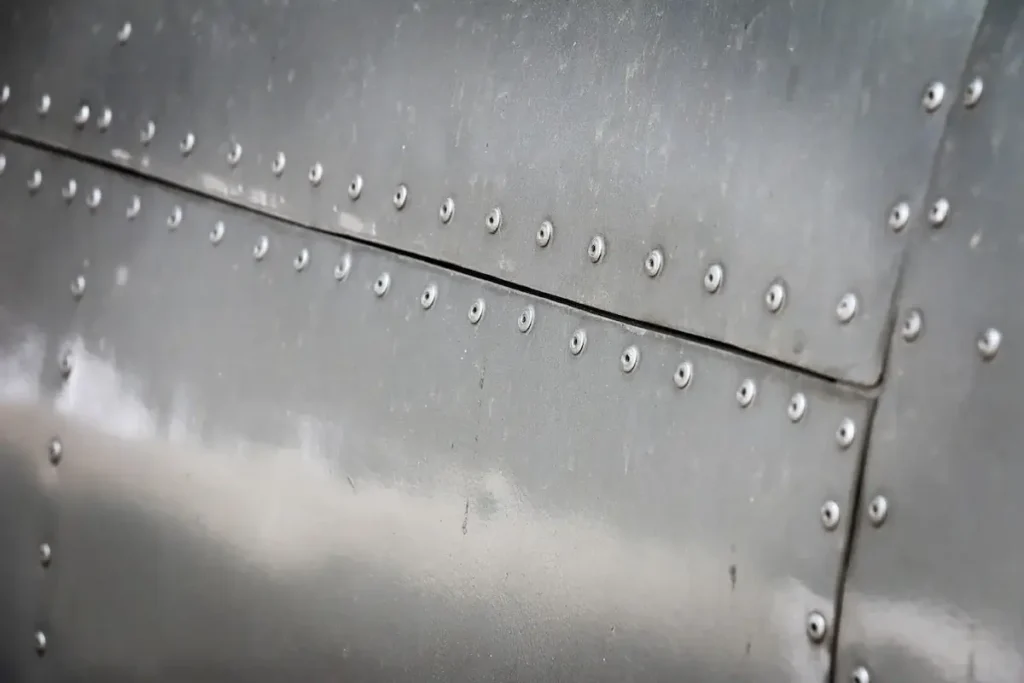

Scenarios for Different Pop Rivet Diameters
- 3/32″ (2.4 mm): for light duty and low load applications.
- 1/8″ (3.2 mm): for medium duty applications, widely available.
- 5/32″ (4.0 mm): for medium to high duty applications.
- 3/16″ (4.8 mm): for high load applications, provides increased strength.
- 1/4″ (6.4 mm): for very high duty applications, providing maximum strength and stability.
Pop Rivets Diameter | Total Material Thickness Range |
---|---|
3/32″ (2.4 mm) | 0.5 – 3 mm |
1/8″ (3.2 mm) | 0.5 – 4 mm |
5/32″ (4.0 mm) | 0.5 – 5 mm |
3/16″ (4.8 mm) | 0.5 – 6 mm |
1/4″ (6.4 mm) | 0.5 – 9 mm |
Select the Length of the Pop Rivets
We determined the thickness of the material being joined and the diameter of the pop rivet in the first and second steps, respectively. Next we need to determine the length of the pop rivets.
So how do you choose the right rivet length for your project? Based on practical experience, the length of the rivet should be greater than or equal to the total material thickness plus 1.5 times the rivet diameter. Here is the formula:
- Rivet Length = Total Material Thickness + 1.5 x Rivet Diameter

Next I will use an example where the thickness being riveted is 6mm and the rivet diameter is 1/8″ (3.2mm).
Total material thickness = 6mm
Rivet diameter = 3.2mm
1.5 times rivet diameter = 3.2mm × 1.5 = 4.8mm
Recommended Rivet Length = Total Material Thickness + 1.5x Rivet Diameter = 6mm + 4.8mm = 10.8mm
Therefore, a rivet with a length of 10.8mm and a diameter of 3.2mm should be selected to join a 6mm sheet. (Usually take a close standard length such as 11mm or 12mm)
Rivet Diameter | Total Material Thickness | Recommended Rivet Length |
---|---|---|
3/32″ (2.4 mm) | 0.5 – 3 mm | 4.8 mm |
1/8″ (3.2 mm) | 3 – 5 mm | 6.4 mm |
5/32″ (4.0 mm) | 5 – 7 mm | 8.0 mm |
3/16″ (4.8 mm) | 7 – 9 mm | 9.6 mm |
1/4″ (6.4 mm) | 9 – 11 mm | 12.7 mm |
Material of Pop Rivet
Above we have determined the right size rivet for your project. Next we need to confirm what material should be used.
There are several common rivet materials that are used:
- Aluminum
- Steel
- Stainless Steel
- Copper
- Monel
Rivets of different steel qualities are suitable for different environmental conditions. The exact choice of material needs to be determined by the environment in which your project will be used.
Environmental Factor
If your project is in a corrosive environment such as marine, chemical. Then you should choose materials with good corrosion resistance (stainless steel, monel, galvanized steel).
If you are using pop rivets in high temperature environment, you need to use material with good heat resistance (stainless steel/monel). If it is used in low temperature environment. You need to choose a material with good toughness (aluminum).
Mechanical Property
Strength requirements vary from program to program. For high strength applications, use steel or stainless steel, and for medium strength requirements, use aluminum.
Copper or aluminum with high ductility and toughness. Suitable for applications requiring some plastic deformation.
Assessing Costs
- Limited budget: choose steel or aluminum. These two materials are suitable for high-volume production and projects with a limited budget.
- Budget friendly: stainless steel or monel. suitable for high performance and high reliability applications.
Special Application Requirements
Does the project need to be electrically conductive? Use copper, great for electrical and electronic connections.
Your project is medical devices and food processing equipment? Then use pop rivets made of copper with antimicrobial properties! It will fulfill your requirements very well!
Head Shape Determination
The head shape of Pop rivets affects the appearance and connection characteristics after installation. Different head styles are suitable for different applications and requirements. There are three common head styles:
- Dome Head
- Countersunk Head
- Large Flange Head

Dome Head Pop Rivets is the most common pop rivet head shape. Suitable for most applications, this head style provides very good surface coverage. Common application scenarios include sheet metal joining, general purpose metal construction, assembly of household appliances, automotive manufacturing, etc.
Countersunk Head Pop Rivets feature a flat head that sits flush with the surface of the material when installed. It does not protrude after installation and provides good aerodynamics. You can often find countersunk head pop rivets in applications that require a smooth appearance, such as aircraft housings, electronic equipment housings, and furniture manufacturing.

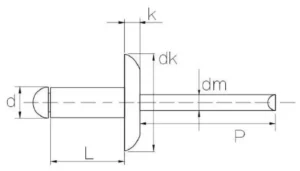
Large Flange Head Pop Rivets have a large head and cover a large area. It is uniquely designed to provide additional surface coverage and made to effectively spread the load and prevent soft materials from being pulled through.Large flange head pop rivets are often used on soft materials such as plastics, wood, composites, etc., acting as a decorative panel fixing.
Color Selection

Some applications have scenarios that require the color of pop rivets. Choosing an appropriate color can enhance the aesthetics and consistency of the connectors.
You can choose the one with the cat that is the same color as the surrounding. Make sure that the overall look is coordinated and consistent. For example, use black pop rivets on a black metal plate.
There are many different colors of rivets, so how are they usually achieved? There are three general ways to change the color of pop rivets:
- Coating and painting
- Anodizing
- Electroplating
You can request your pop rivets supplier accordingly when you purchase pop rivets. Usually pop rivet manfacturer provides customized pop rivets service. If you don’t know how to contact pop rivet manufacutrer, you can contact us!
Preliminary Test
With all of the above information determined, the pop rivets that are appropriate for your program have also been determined for all factors!
It is recommended that you conduct a small test run to ensure that the pop rivets will provide sufficient strength and stability before you officially use them. You can test the actual installation results and load tests to make sure the rivets perform well in real-world applications.
Should Rivets be The Same Size as Holes?

In practice, the diameter of the rivet is not the same as the diameter of the hole. Generally speaking, the hole diameter will be slightly larger than the rivet diameter, so as to ensure that the rivet can be inserted smoothly into the hole and correctly expand to form a solid connection. Please follow our recommended hole diameter ranges and tolerances and use the appropriate drill and drilling method to ensure the quality and reliability of the installation of pop rivets.
Rivet Size Chart and Drill Size Chart
Rivet Diameter | Drill |
mm(inch) | mm |
2.4(3/32″) | 2.5-2.6 |
3.0(7/61″) | 3.1-3.2 |
3.2(1/8″) | 3.3-3.4 |
4.0(5/32″) | 4.1-4.2 |
4.8(3/16″) | 4.9-5.0 |
5.0(6/31″) | 5.1-5.2 |
6.0(15/64″) | 6.1-6.2 |
6.4(1/4″) | 6.5-6.6 |
8.0(5/16″) | 8.1-8.2 |
9.6(3/8″) | 9.1-9.2 |
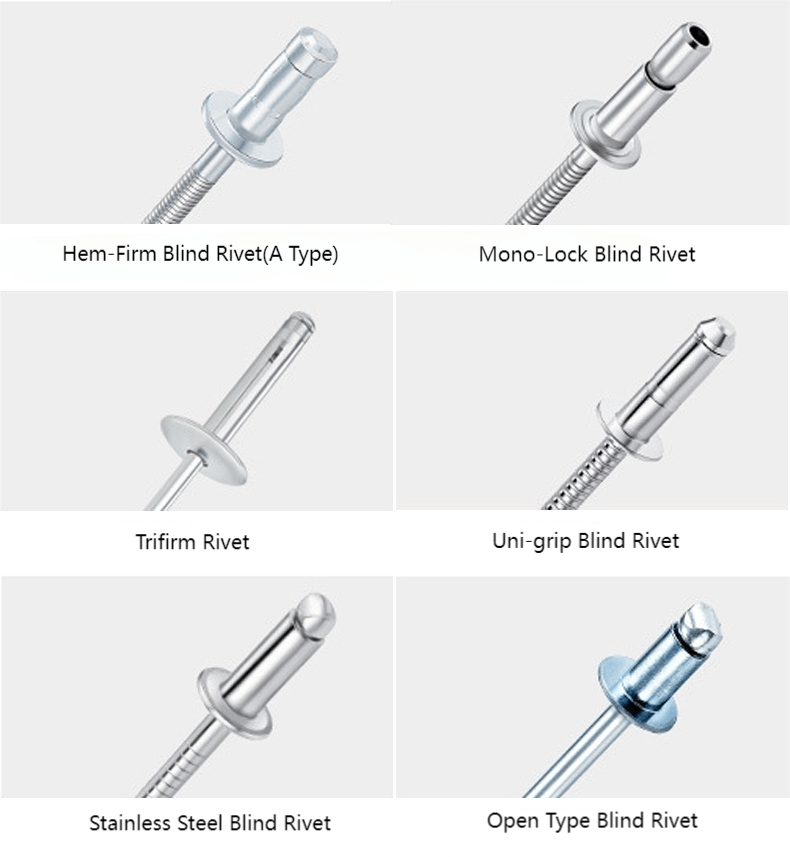
Conclusion
With the above, I am sure you already have a deep understanding of how to choose the right pop rivets for your project. If you still have doubts about this or want to go through our engineers to help you, please contact us!
Before starting your project, you just need to determine the diameter, length, material, head shape and other necessary parameters of the pop rivets. You will then be able to choose the right pop rivets for your project.
Rivmate Can Provide Custom Pop Rivets for Your Project
Are you looking for pop rivet manufacturer who can provide customized pop rivets for you? Rivmate is a top China pop rivet manufacturer and supplier. You can get standard pop rivet, high strength structure pop rivet, customized pop rivet from Rivmate!
Still don’t know how to choose the most suitable pop rivets for your project? Don’t worry, contact our engineer immediately, she will provide you with the most comprehensive and professional pop rivets solutions!