The Complete Guide to Zinc Plated Blind Rivets
Table of Contents
The surface of Zinc Plated Blind Rivet is covered with a zinc metal coating through an electroplating process. As a result, the corrosion resistance, surface stability and range of environments in which it can be used are greatly enhanced. In addition, the conditions and methods of use of Zinc Plated Blind Rivets are the same as those of ordinary Blind Rivets.
This blog will focus on zinc plated blind rivets. Including its definition, benefits, applicable types, applications, and purchasing costs.
what are zinc plated blind rivets?
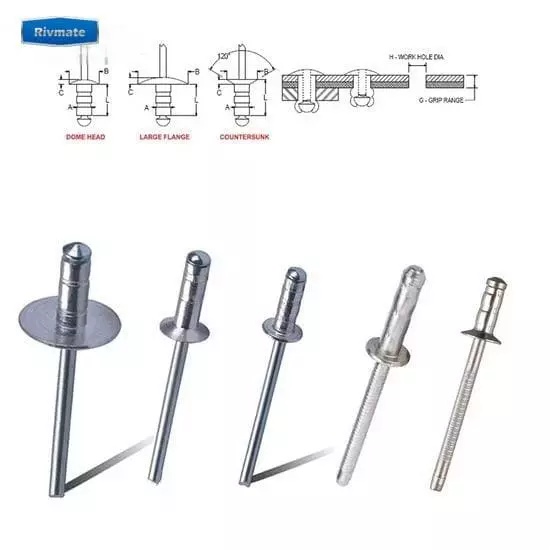
Zinc Plated Blind Rivet is a fastener with a zinc metal coating applied to the surface of a carbon steel blind rivet through an electroplating process. This finish was selected to improve the corrosion resistance, surface stability and environmental range of blind rivets. These rivets are identical in construction to standard blind rivets and can be used to make permanent connections to sheet metal, profiles or housings by one-sided operation, and are commonly used in construction, equipment, and electrical assemblies.
Zinc plated blind rivets offer significant corrosion resistance advantages over ungalvanized blind rivets. In wet, lightly corrosive environments, zinc plated blind rivets are effective in extending service life and maintaining a consistent appearance.
In addition, the zinc coating slows down oxidized spots and red rust. Exposed carbon steel rivets, on the other hand, are prone to rapid corrosion upon exposure, leading to structural failure or aesthetic degradation. As a result, zinc plate is routinely the preferred solution for cost-effective, basic protection requirements.
Advantages and benefits of blind rivets zinc plating
Zinc plated of Blind Rivets is a common metal protection and enhancement process. By forming a metallic zinc coating on the surface of the rivet (usually electroplated or hot-dip plated), this process accomplishes several important things:
- Corrosion protection: The zinc layer effectively isolates the rivet substrate from direct contact with moisture, oxygen, acid and alkali environments.
- Enhance surface stability: Reduce surface oxidation and corrosion, reduce maintenance and replacement costs.
- Provide basic aesthetics: galvanized surface is blue-white, colored zinc and other natural metal tones, more neat than the original steel.
How much corrosion protection is improved?
Zinc Plating Type | Coating Thickness (μm) | Passivation Treatment | Salt Spray Resistance (No Red Rust) |
---|---|---|---|
Electroplated Zinc (Blue White) | 5–8 μm | Trivalent Chromium (Blue White) | 72–96 hours |
Electroplated Zinc (Yellow/Color) | 8–10 μm | Trivalent Chromium (Iridescent) | 120–168 hours |
Thick Zinc Plating (Heavy Duty) | ≥12 μm | High-performance passivation + seal | 240–300 hours |
Hot-Dip Galvanized (rare for rivets) | ≥30 μm | No passivation needed | ≥500 hours (not suitable for small parts) |
Estimated percentage upgrade (compared to untreated carbon steel rivets)
Ungalvanized rivets: red rust can appear within 24 hours in high humidity or salt spray environments.
After galvanized treatment:
- Ordinary blue-white zinc can enhance the corrosion protection time to more than 3-4 times;
- Colored zinc treatments enhance protection up to 5-7 times;
- High-performance passivation/sealing solutions can be upgraded by more than 10 times (theoretical 300+ hours without red rust).
What types of blind rivets are galvanized?
Blind Rivet materials suitable for Zinc Plating are mainly carbon steel, followed by some copper alloys. Stainless steel and aluminum are not recommended for zinc plating due to poor plating suitability.
Material Type | Zinc Plating Suitable | Compatibility Notes | Recommended Level | Typical Applications |
---|---|---|---|---|
Carbon Steel | Yes | Excellent plating adhesion, ideal for barrel or rack plating | ★★★★★ | Industrial fasteners, enclosures |
Alloy Steel | Yes (with precautions) | Risk of hydrogen embrittlement; requires controlled process | ★★★★☆ | Structural or high-strength riveting |
Copper / Brass | Conditionally | Can be plated, but nickel/tin preferred for appearance or conductivity | ★★☆☆☆ | Internal joints, non-visible parts |
Stainless Steel | No | Poor adhesion, peeling risk; not recommended | ★☆☆☆☆ | Use as-is without plating |
Aluminum / Alloys | No | Very poor adhesion; high galvanic corrosion risk | ★☆☆☆☆ | Use anodizing or painting instead |
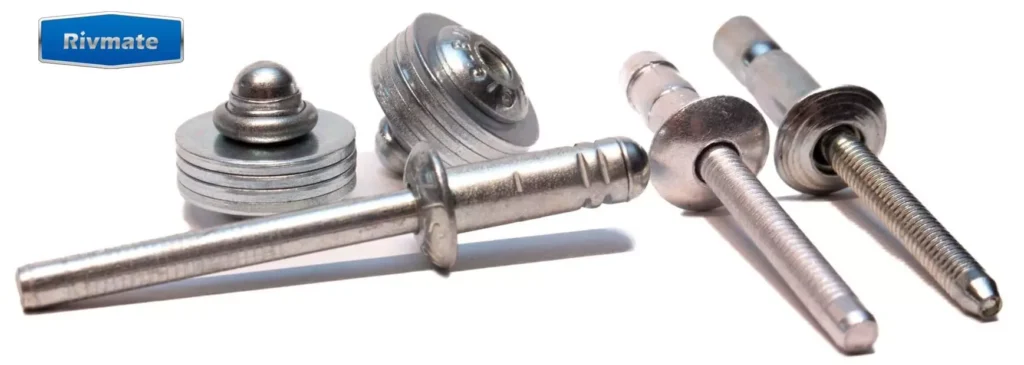
Blind Rivets Zinc Plated Thickness and Standard
zinc plated thickness
The thickness of the galvanized layer for blind rivets is set according to the environment in which the rivets are used, the level of corrosion protection required, and the processing technology (e.g. electroplating, hot-dip plating).
There are three common ways to zinc plated blind rivets:
- Electro-galvanized: coating thickness 5-12 μm. This is the amount of galvanization used for standard rivets and is suitable for indoor or medium humidity environments.
- Heavy Zinc: Plating thickness of 12-15 μm. This is required for high corrosion resistance and requires control of dimensional tolerances and plating uniformity.
- Hot-Dip Galvanizing: Plating thickness ≥ 30 μm. This thickness is rarely found on rivets and is suitable for large structural parts.
standard
There are three main international standards for zinc plated blind rivets: ASTM B633, ISO 4042 and ROHS/REACH.
Rivmate is proud that its zinc plated blind rivets are fully compliant with these standards.
Precautions:
- The higher the plating thickness, the more difficult it is to control the dimensional tolerances, especially in the grip area;
- Roller plating is suitable for small-size high-volume rivets, but the plating may be slightly uneven, thin edge area;
- Plating adhesion is closely related to the quality of pretreatment, pickling and descaling and activation must be standardized.
Recommended Use: Choose Zn5-Zn8 (5-8μm) for general industrial use. For structures with a moderate risk of corrosion or in wet environments, thickness grades of Zn12 (12μm) and above are recommended.
Industry applications for galvanized blind rivets
zinc plated blind rivets are used in a large number of applications in several industrial sectors due to their cost-effectiveness and wide range of applications. If your application is a scenario where there are basic requirements for structural strength but the corrosion protection level is not extremely high, then zinc plated pop rivets are a good choice.
✅ Main application industries
- Home appliance manufacturing: used in the shell, bracket and internal connection parts of air conditioners, refrigerators, microwave ovens and washing machines.
- Industrial equipment and sheet metal manufacturing: power distribution cabinets, operating boxes, machinery shrouds, bracket assembly, etc.
- Metal furniture and building materials components: iron cabinets, shelves, aluminum profile joints, light box frames, etc.
- Vehicles and transportation equipment: trailer guards, bus interior parts, door structures, and other non-load-bearing areas.
- Assembly-type low- and medium-voltage electrical products: switch panels, radiators, wire bridges, etc.
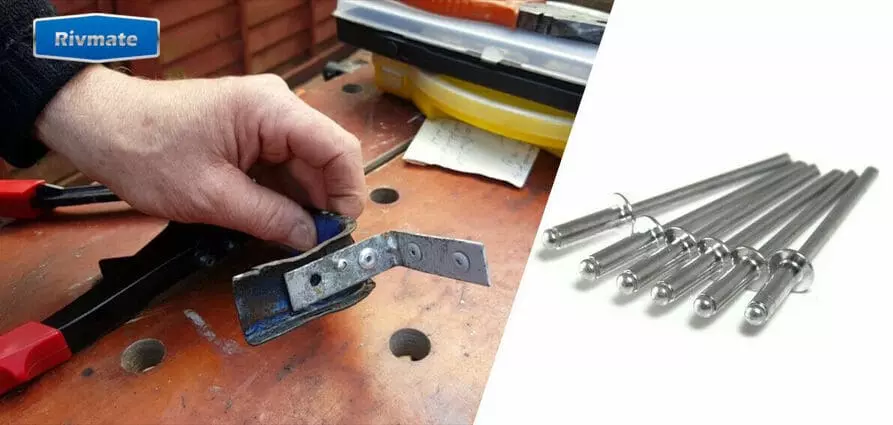
⚠ Basic requirements for the installation environment
- Suitable for indoor, light industrial, low corrosive environments;
- Can be used in relatively humid environments, but prolonged flooding or high salt spray conditions should be avoided;
- Not recommended for use in exposed seashores, acid and alkali corrosive areas or high temperature chemical environments;
- For outdoor use, thick zinc plated + colored zinc passivated versions should be used or upgraded to stainless steel/aluminum anodized rivets.
Are there galvanic corrosion problems?
Galvanic corrosion may occur when using zinc plated rivets on aluminum, copper, and stainless steel. This phenomenon is more pronounced if the application environment is humid.
Since zinc has a lower electrode potential than many structural metals, it acts as a “sacrificial anode” in galvanic couples, accelerating its own corrosion in order to protect adjacent metals. This is likely to lead to early failure of the rivet or the spread of corrosion spots.
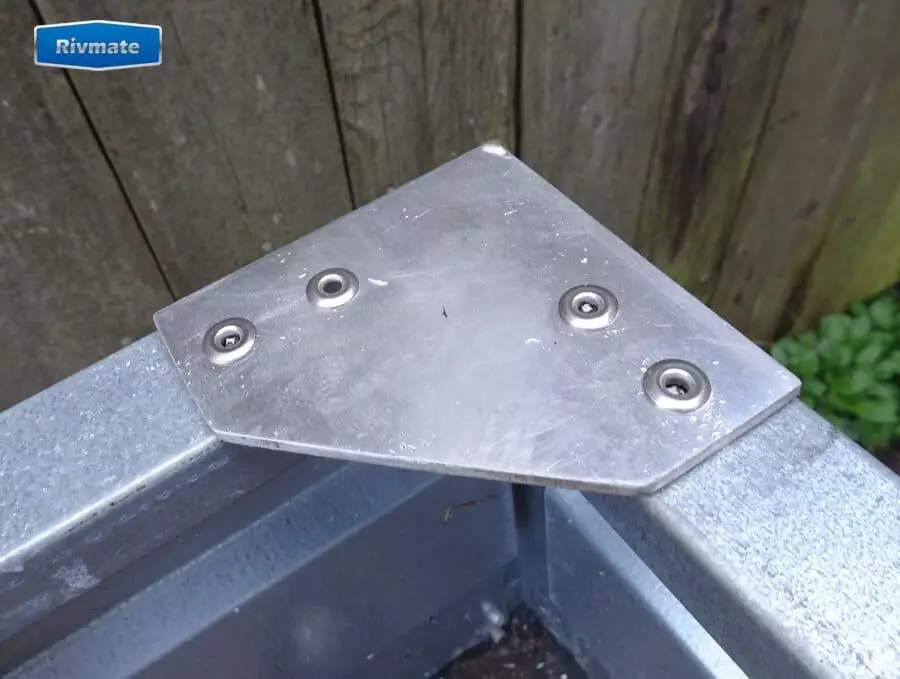
In order to avoid galvanic corrosion, it is recommended to take the following measures from the design and process:
- Try to choose the rivet material close to the potential of the connected material, such as carbon steel plate with carbon steel zinc plated rivets.
- Use insulating gaskets, plastic washers or anti-corrosion coatings in the assembly structure to block the direct contact between metals.
- Seal riveted areas to prevent moisture from entering the gap and creating an electrolytic environment.
Purchasing cost of galvanized rivets
Compared to stainless steel rivets, zinc plated rivets typically cost 30% to 50% less. The raw materials used in the manufacture of zinc plated rivets are generally low cost carbon steel, low energy processing, and the electro-galvanizing process is well established and suitable for volume roll plating. Galvanized rivets are a cost-effective choice for general industrial applications where corrosion resistance is not particularly demanding. If your usage scenario is for high-volume assemblies, one-off structural components or non-exposed joints, zinc plated rivets will be more suitable for you.
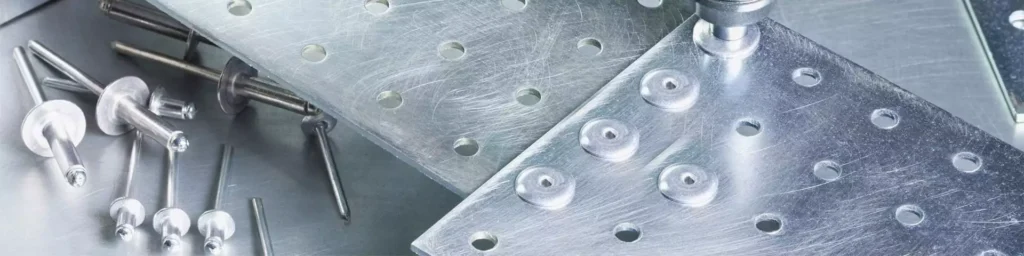
Zinc plated rivets also offer a cost advantage over nickel plated rivets, with typical unit cost savings of approximately 20-30%. The higher price of nickel and plating requirements make nickel-plated rivets more suitable for products that require electrical conductivity, aesthetics or greater corrosion resistance. Galvanized rivets, on the other hand, while slightly less attractive in terms of appearance and long-life protection, are adequate for most low to medium corrosive environments, making them a practical solution that balances performance with budget.
wholesale zinc plated blind rivets from Rivmate
Why would you choose to use zinc plated blind rivets? It is a combination of cost and performance options. Therefore, the quality and price of galvanizing is very important. You need to get the best value for money riveting solution from the rivet manufacturer!
Rivmate — The Leading Blind Rivet Manufacturer and Supplier in China.
You can get solutions from Rivmate that will fully meet your needs and satisfy you. Contact our engineers and get a sample rivet for testing!
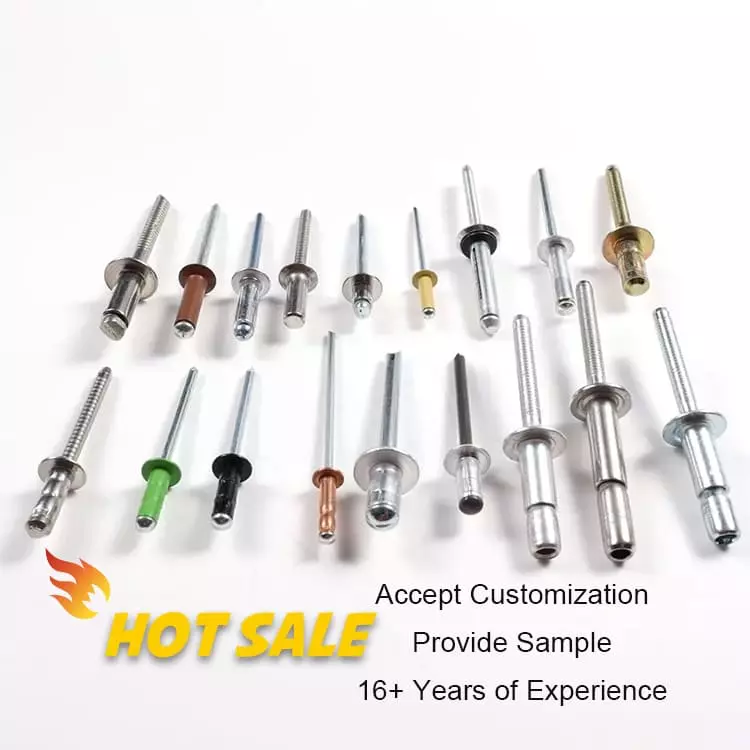
Share:
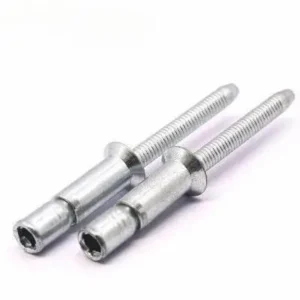
What is the Difference Between Countersunk Rivets and Regular Rivets? – Rivmate Expert Guide
What is the Difference Be
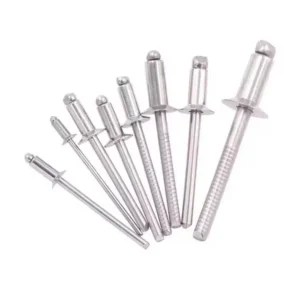
What are Countersunk Blind Rivets Used for?
What are Countersunk Blin
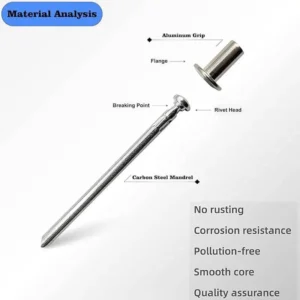
Problem with Rivet Mandrel Breaking
Problem with Rivet Mandre
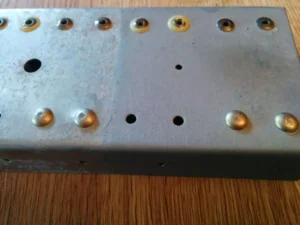
Rivet Corrosion: Causes, Prevention, and Engineering Solutions
Rivet Corrosion: Causes,