Table of Contents
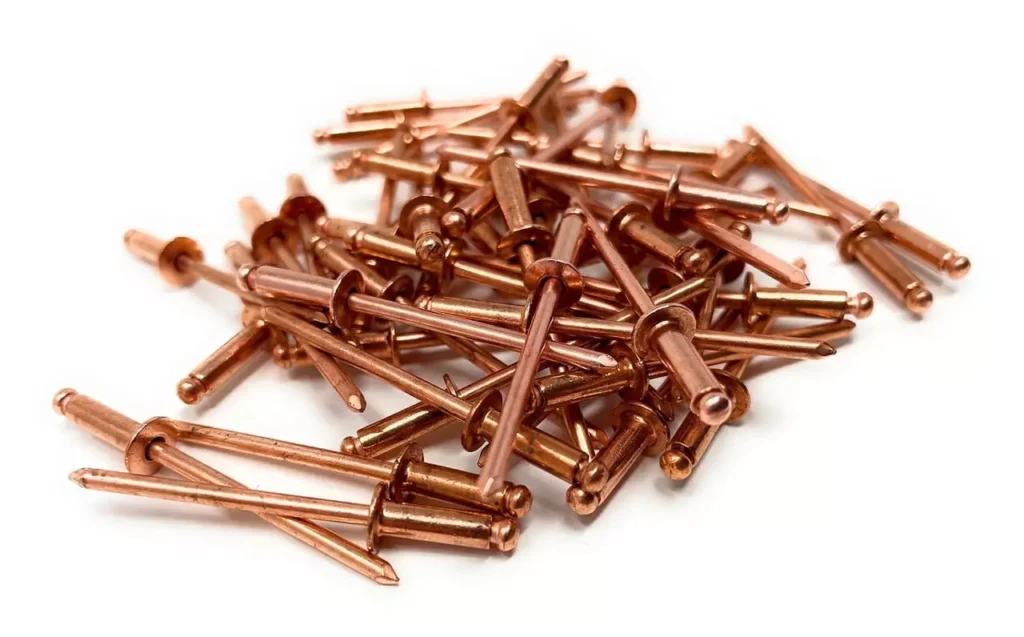
Brass pop rivets and copper pop rivets are two types of rivets often used on copper. So do you know the difference between brass vs copper rivets?
This blog will describe to you brass vs copper rivets by focusing on the differences of brass rivets and copper rivets. including the advantages of using brass rivets and copper rivets and the 4 main differences between them.
Table of Contents
Why Use Brass Rivets?
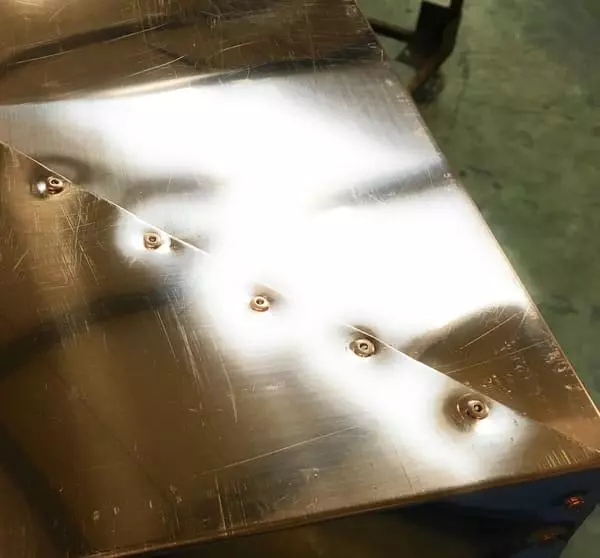
The reasons for using Brass Pop Rivets are centered on their excellent mechanical properties, aesthetic appearance, corrosion resistance and material compatibility. The following are the core benefits of using Brass Pop Rivets:
- Aesthetic Metal Appearance: Brass has a natural golden yellow luster, a smooth surface, and a slow oxidation rate that maintains its bright appearance over time in an untreated state.
- Excellent mechanical strength: brass has higher hardness and shear resistance than aluminum and is also more stable than pure copper. It can provide good tensile strength and shear resistance.
- Stronger corrosion resistance: the zinc content of brass improves its corrosion resistance to humid and neutral environments.
- Suitable for a wide range of base materials: as a neutral metal, brass has a wide range of suitability and good compatibility with a wide range of materials.
- Better price/performance ratio than pure copper rivets: brass rivets are more stable in price and more efficient in processing than copper rivets, which are more costly and prone to oxidation.
Why Use Copper Rivets?
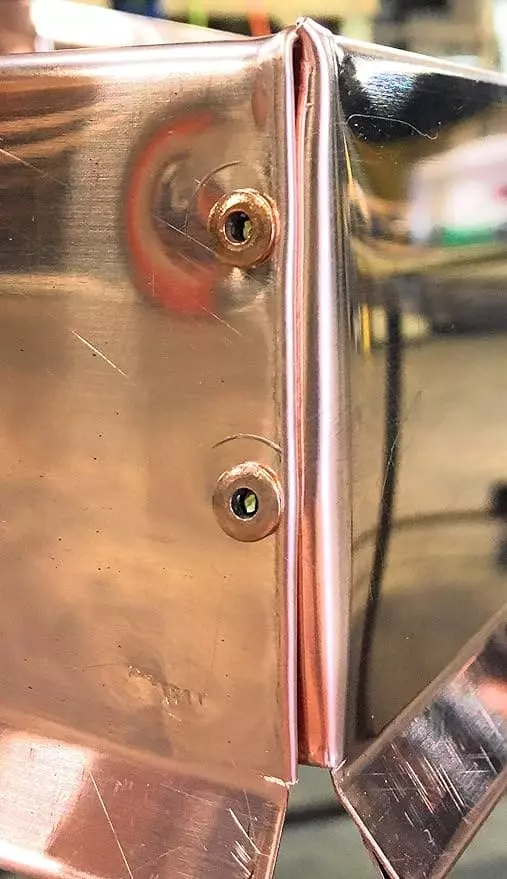
The unique advantages of Copper Blind Rivets are as follows:
- Superior electrical conductivity: copper is the second most electrically conductive metal after silver.
- Extreme corrosion resistance: Copper has excellent self-passivation as it forms a dense oxide film in air, which further prevents corrosion from expanding.
- Good thermal conductivity: copper has an extremely high thermal conductivity (about twice that of aluminum).
- Outstanding deformability and vibration resistance: copper is softer, the deformation is uniform when the core is pulled and broken, and the tail expansion molding is fuller, which can effectively absorb vibration and dynamic shock and prevent loosening.
- Good material compatibility (especially copper to copper).
- High environmental protection and recyclability.
Do You Have Any Questions?
Let Us Solve Your Problem
Brass vs Copper Rivets - 4 Differences
Although both Brass Pop Rivets and Copper Pop Rivets belong to the copper-based category, they differ significantly in terms of composition, performance, application scenarios and cosmetic finishes.
I. Brass vs copper rivets: Material composition and structural differences
Brass rivets, made from copper and zinc alloys, are harder, have good tensile and shear properties and are suitable for medium strength structural connections. In contrast, copper rivets are usually made of pure or oxygen-free copper, which is a softer, more ductile material that is better suited to irregular deformations or for joining softer base materials.
Copper is more prone to uniform, smooth expansion and deformation during riveting, whereas brass requires higher tensile strengths and is suitable for precise installation with a consistent rivet gun.

Comparison Item | Brass Pop Rivet | Copper Pop Rivet |
Material Content | Copper + Zinc alloy (Cu-Zn), higher hardness | Pure copper (>99% Cu) or oxygen-free copper, more ductile |
Metal Color | Bright yellow, glossy | Reddish-brown or orange-red, oxidizes easily |
Strength | Higher tensile and shear, harder | Softer, better deformation, more expansion-friendly |
Conductivity | Good (moderate) | Excellent electrical conductivity |
Workability | Harder, needs more pull force | Easier to form and break, ideal for manual or medium-load tools |
II. Brass vs copper rivets: Differences in Performance and Usage Scenarios
1. Conductivity and suitability for electrical applications
In terms of conductivity, copper blind rivets perform significantly better than brass blind rivets. copper is almost second only to silver as a high quality conductor, suitable for use in electric power, electronics, electrical equipment and other scenarios that require high conductivity, such as busbar connections, grounding terminals, copper wire clamping, etc. Although brass also has a certain degree of conductivity, but more Although Brass also has a certain degree of conductivity, but it is more suitable for mechanical connection or the appearance of the higher requirements of the occasion.
2. Corrosion resistance and environmental adaptability
Copper rivets have the ability to naturally form a protective oxide film and can be used stably for long periods of time in marine, humid and acidic environments, making them particularly suitable for corrosion-resistant connections in outdoor, industrial or electrical enclosures. On the other hand, brass rivets are prone to “dezincification corrosion” due to the presence of zinc and prolonged exposure to air and moisture, and their long-term corrosion resistance is not as good as that of copper rivets, especially in salt spray or acidic environments.

3. Decorative and Aesthetic
Brass rivets are widely used in middle and high-end decorative products such as furniture, decorative hardware, vintage lamps and other decorative products due to its golden color and stable metallic luster. Its appearance is not easily tarnished and can maintain its bright color without treatment.
Copper rivets, on the other hand, have a reddish-brown or orange-red color and are prone to oxidization and blackening or the formation of a patina, which is not conducive to maintaining a bright appearance, but meets the demand for natural aging for vintage styles or craft projects.
4. Processability and Tool Compatibility
Copper blind rivets are suitable for fast assembly with medium strength rivet guns due to their softer material, clear core breaks and higher installation efficiency.
Brass rivets due to the higher hardness, especially in the larger diameter rivets, often require higher tension, recommended with pneumatic or electric rivet guns, and in high-frequency operations to regularly check the clamping jaw wear.
Conclusion
Performance Aspect | Brass Pop Rivet | Copper Pop Rivet |
Stress Control | Higher mechanical strength, suitable for mid-load | Lower stress, better for delicate or soft material fastening |
Electrical Use | Limited, usable for non-critical connections | Ideal for grounding, busbars, electrical contacts |
Corrosion Resistance | Zinc content offers some protection, may weaken over time | Stable self-oxidizing barrier, better long-term resistance |
Anti-Vibration | Stiff after set, average vibration resistance | Retains some flexibility, better anti-loosening |
Surface Appearance | Keeps gloss longer, less prone to discoloration | Tends to oxidize unless treated |
Compatibility with Automation | Suitable for standard automated assembly | Better suited for manual or low-speed riveting |
III.Brass vs copper rivets: Differences in areas of application
- Copper rivets are mainly used in electrical, electronic, outdoor corrosion protection, electrical grounding, corrosion-resistant fastening and other functional areas.
- Brass rivets are more inclined to structural connections, aesthetic appearance, the assembly of metal decorative parts, as well as light load mechanical structure fixed.
4. Processability and Tool Compatibility
- Due to the volatility of the price of copper itself, copper rivets are typically more costly and more sensitive to material protection during processing, making them suitable for specialized markets.
- Brass rivets, as a more versatile and cost-controlled solution, are more widely available in the market and are suitable for bulk purchasing and standardized assembly.
Do You Have Any Questions?
Let Us Solve Your Problem
Brass vs Copper Rivets FAQs
How does the Corrosion Resistance of Brass Rivets Compare to Copper Rivets?
Brass rivets have good corrosion resistance in normal indoor environments, but in wet or highly corrosive environments, copper rivets perform more consistently and their natural oxide film resists corrosion over time.
Are brass rivets available for outdoor or marine environments?
Not recommended. Brass rivets are prone to dezincification and corrosion in salt spray and acidic environments, copper rivets are better suited to such conditions of use.
Can brass rivets be used to join copper or aluminum parts?
Not recommended. Mixing dissimilar metals may initiate galvanic corrosion; brass with brass, copper with copper, and aluminum with aluminum are recommended.
Which rivet is more durable in high humidity or corrosive environments?
Copper rivets are better suited to such environments, with their naturally occurring oxide layer providing long-term protection against corrosion or failure.
Wholesale Brass and Copper Pop Rivets from Factory
Brass pop rivets and copper pop rivets are both very commonly used blind rivets. by reading this post, I am sure you already know the main difference between them. If you want to buy both types of pop rivets at factory price, please contact us!
Rivmate – Leading Brass Pop Rivets and Copper Pop Rivets Manufacturer in China!
Get Rivets Quote
You may also find these topics interesting
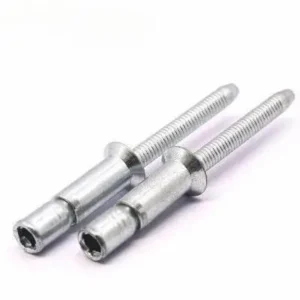
What is the Difference Between Countersunk Rivets and Regular Rivets? – Rivmate Expert Guide
What is the Difference Be
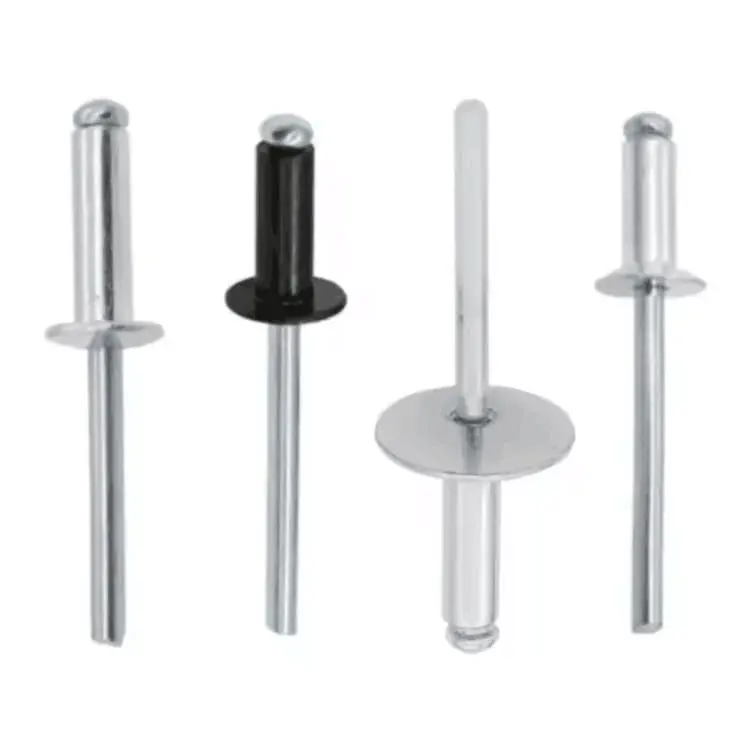
Buy Open Type Blind Rivets
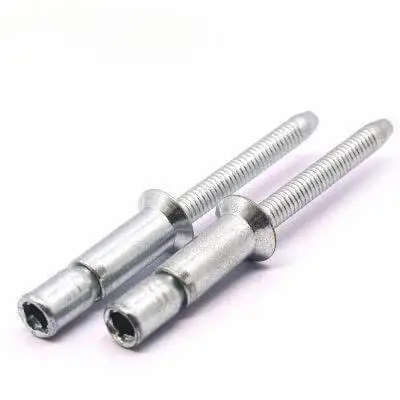
Buy Structural Blind Rivets
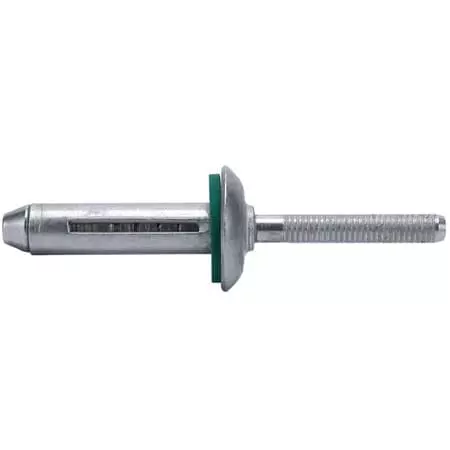