Rivmate Self Piercing Rivet Supplier
SPR Rivet (Self Piercing Rivet)
Provide Security For Your Project With High Sterngth SPR Rivet
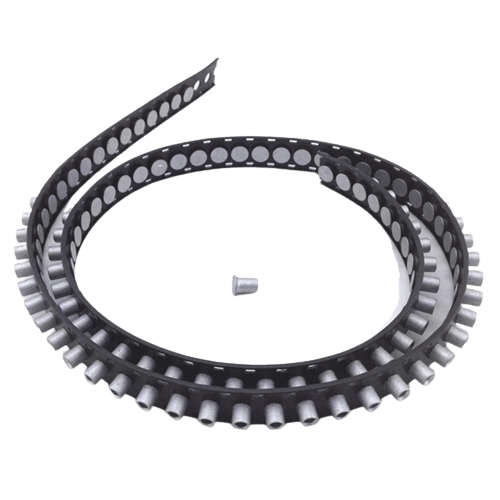
Home » blind rivet supplier » spr
Self Piercing Rivet (SPR Rivet)
Material | Carbon Steel |
Head Type | CSK |
Quality Authentication | IATF16949,ISO14001,ISO45001 |
Surface | Zinc plated/Natural polish |
Size | 3.3 - 5.3 |
Own factory? | YES |
Customized services | YES |
Standard | ISO,DIN7337,IFI114,HUCK,AVDEL etc |
Advantages of Self Piercing Rivet(Spr Rivets)
- At that point in the application, there is no need to cut a hole and you can install it in a random location.
- When using self-pierce rivets, at least 1 surface of the workpiece is flat
- No waste nail cores after installation, saving raw material
- Self Piercing rivets are very easy to install and efficient to install
- Ideal for high volume industrial production
- Does not pollute the environment, environmentally friendly, low noise level
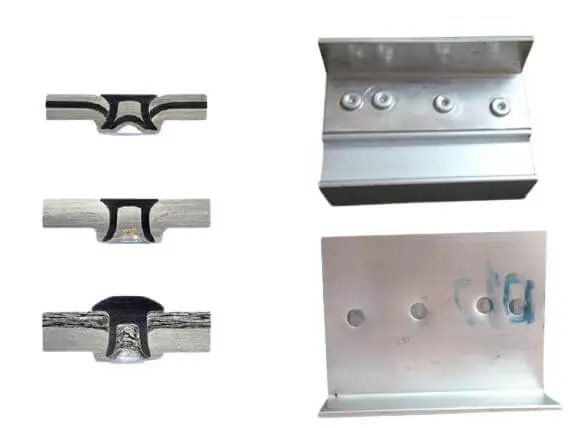
The Technical Specification of Self Piercing Rivet(SPR RIvet)
Part Number | Size | D | L | Quantity |
---|---|---|---|---|
SSPRA53040 | 5.3×4 | 5.3 | 4 | 5000 Only/dsk |
SSPRA53050 | 5.3×5 | 5.3 | 5 | |
SSPRA53055 | 5.3×5.5 | 5.3 | 5.5 | |
SSPRA53060 | 5.3×6.0 | 5.3 | 6 | |
SSPRA53065 | 5.3×6.5 | 5.3 | 6.5 | |
SSPRA53070 | 5.3×7.0 | 5.3 | 7 | |
SSPRA53075 | 5.3×7.5 | 5.3 | 7.5 | |
SSPRA53080 | 5.3×8.0 | 5.3 | 8 | |
SSPRA53090 | 5.3×9.0 | 5.3 | 9 | |
SSPRA53100 | 5.3×10.0 | 5.3 | 10 | |
SSPRA53120 | 5.3×12.0 | 5.3 | 12 | 4000 Only/dsk |
SSPRA33035 | 3.3×3.5 | 3.3 | 3.5 | 10000 Only/dsk |
SSPRA33040 | 3.3×4.0 | 3.3 | 4 | |
SSPRA33050 | 3.3×5.0 | 3.3 | 5 | |
SSPRA33060 | 3.3×6.0 | 3.3 | 6 |
Reply within 12 Hours
Send us a message if you have any questions or request a quote. We will be back to you ASAP!
Location
+86 189 6230 4392
or write
manufacture@world-rivet.com
CONTACT PERSON SEARCH
Custom Surface Treatment
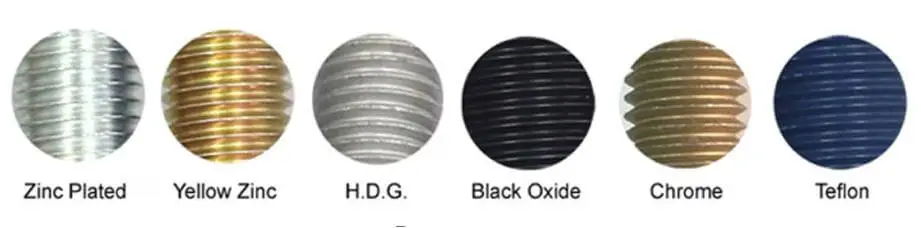
Custom Raw Material
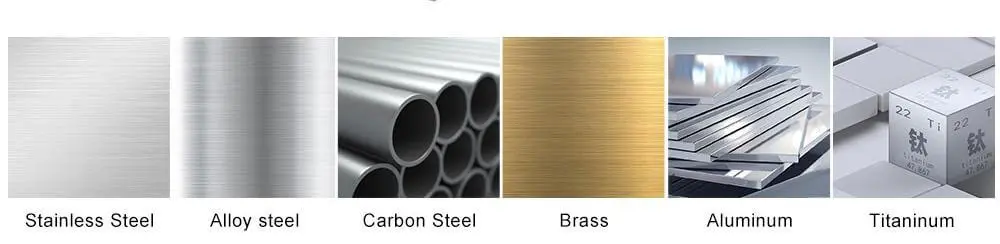
Products Recommended
Fastener Exhibitions
How to Choose Self Piercing Rivets(SPR Rivet)?
I think the specifications of self-pierce rivets are divided into a variety of different types. Such as different types or thickness is not the same, the material is not the same selection of self-pierce rivets standard is not the same.
Some of the self piercing rivets material is the application of alloy steel production. its appearance for the round head ring, their specifications in the middle of the 3.2-5.3, the length of the self-pierce rivets in the 5-13 mm. The size and thickness of the rivets depends on the material to be riveted.
Self-pierce rivets are capable of motor selection based on thickness, material, etc.
- Confirmation of sheet metal part thickness
- It is important to figure out the material in which the self piercing rivets are to be used.
- Selecting the length of self piercing rivets
Confirm the above information to be able to confirm the use of self piercing rivet should be used in the model specifications
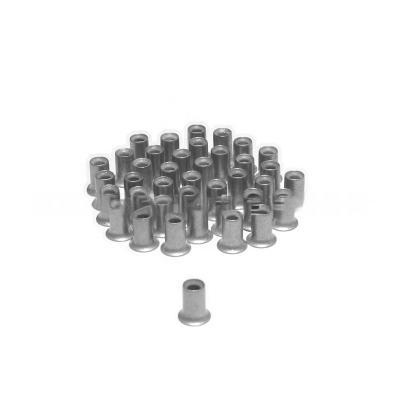
Attention to the Use of Self Pierce Rivets Standard Parts
- Steel or stainless steel fasteners may not be installed prior to anodizing or metal finishing of aluminum alloy panels.
- Do not remove nearby burrs before installing the riveted standard – as removing the burrs consumes the metal material of the standard and the plate.
- Do not over-extrude the molding, which can flatten the top, deform the male threads and bend the plate. Before mass production, the best installation force should be confirmed based on tests.
- Do not attempt to install the standard with a hammer, as the hammer will not easily stabilize the fluidity of the plate and create an interlock with the gallery of the standard.
- Do not install the screws from the top of the head of the standard, they must be installed from the opposite side of the head of the standard, which allows the force house of the standard to face the plate.
- Do not install riveting standards on pre-plated boards.
Self Piercing Rivets(SPR Rivet) in the Automotive Industry
Self Piercing riveting is a tempting joining technique in the automotive industry, especially for materials that are difficult to resistor-bump weld. Aluminum alloy profiles bring challenges to the welding process while relieving the mass of the car body. For example, MIG/MAG welding, which is widely used in automotive general-purpose parts, will face the following difficulties.
- With the use of aluminum alloy profiles, the material thickness is thinner than the original, and it is easy to weld through the steel parts.
- Easy to deform after welding
- Aluminum alloy profiles are more sensitive to heat input and prone to welding cracks.
- Compressive strength of butt welds in the heat affected zone is easily weakened
- Steel and aluminum dissimilar metals are not easy to connect with each other
Touch welding is also facing difficulties: aluminum resistor is smaller than steel, heat transfer coefficient is much better than steel, touch welding needs to use multiples of steel touch welding current; electric level is easy to be contaminated. At the same time, aluminum alloy profile is a high reflectivity material, it is difficult to use laser welding.
Therefore, the main welding methods used in the automotive industry (MIG/MAG welding, touch welding, laser welding, etc.) are no longer sufficient to meet the requirements of aluminum alloy profiles. More advanced joining technologies have to be developed in order not to hinder the development of lightweight automobiles.
And punch riveting process to meet the stainless steel plate or aluminum and other lightweight materials connection requirements. No exothermic reaction in the riveting process; its static tensile strength and fatigue relief are better than the touch welding process, and the plate only in the riveting does not need to turn the hole; process steps to simplify and reduce costs. Can be suitable for automotive body of the production of high efficiency, and effectively overcome the aluminum touch welding produced by the various difficulties.
Self Piercing Rivet
These have prompted the punch riveting porting method to be used more and more in recent years in the production and processing of car bodies. such as the body’s covering parts, window rollers, car trunk windows and so on. This process is suitable for intelligent robotic applications, but due to the need for quite high pressure, the usual riveting equipment exceeds the transportation capacity of intelligent robots. Therefore S.A. Westgate developed a lightweight, sufficiently long C-shaped riveting mechanism. Together with related equipment improvements, the increased adaptability of the self-pierce riveting process has been demonstrated for burned-in automotive parts and body assembly lines.