Table of Contents
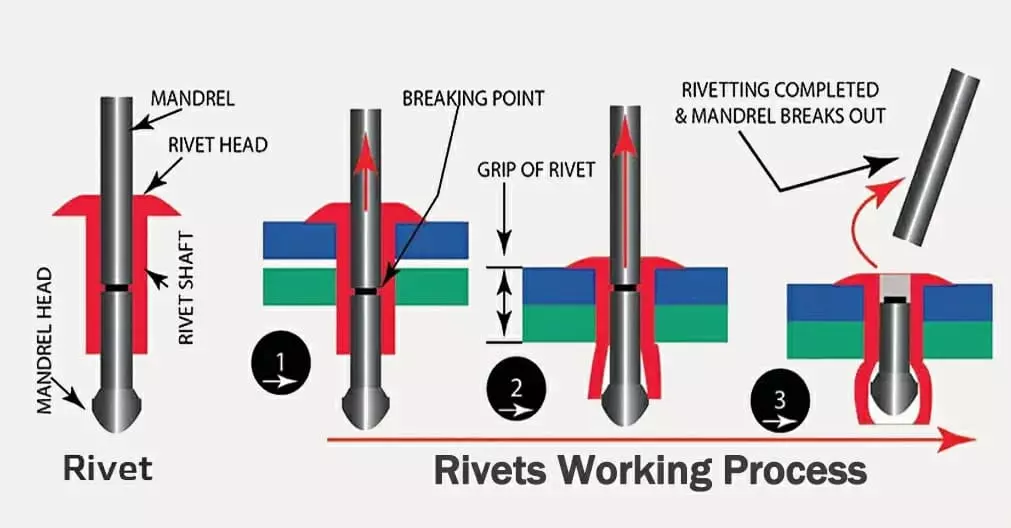
Breaking strength of rivets determines the strength needed to break a rivet. Through this comprehensive guide, you will learn the basic definition of rivets breaking strength, the factors that influence it, and the conditions under which it is applied in a scenario.
Table of Contents
The Breaking Strength of Rivets - Define
The breaking strength of rivets is the maximum stress value that rivets can withstand before fracture occurs when subjected to external forces, usually determined through experimental testing. It is the core index to measure the reliability of rivet connection, which directly affects the bearing capacity and safety of the structure.
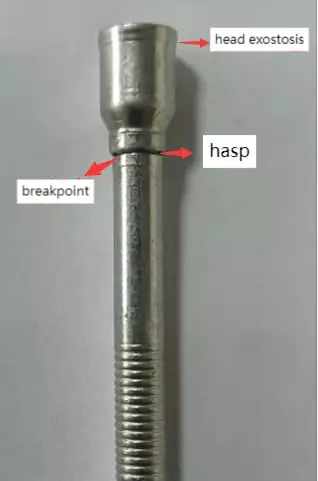
The Importance of Breaking Strength in Connection Performance
- Preventing Sudden Failure: Inadequate breaking strength can cause rivets to suddenly fracture under load, triggering structural disintegration. For example, the aerospace industry requires rivets with high shear strength to withstand dynamic loads in flight.
- Load carrying capacity assurance: In bridge or building steel structures, rivets need to resist both shear and peel forces. Studies have shown that the shear strength of solid rivets is slightly lower than that of bolts, but their ability to deform plastically provides a cushion against brittle fracture when overloaded.
- Environmental adaptability: In corrosive environments (e.g., ships, chemical equipment), fracture strength needs to be evaluated in conjunction with corrosion resistance. For example, the stress corrosion fracture risk of stainless steel rivets needs to be controlled by material selection and surface treatment.
What are the Factors that Affect the Breaking Strength of Rivets?
The factors affecting the breaking strength of rivets can be summarized in the following five categories.
I. Material and manufacturing factors
Material Properties
The chemical composition, grain size and heat treatment process of rivets directly affect their strength and toughness. For example, LY10 aluminum alloy is commonly used for aviation rivets because of its high shear strength (235 MPa) and plasticity. The presence of microporosity, inclusions or grain boundary brittle phases (e.g. hydrogen embrittlement white spots) can significantly reduce the fracture strength. In addition, improper heat treatment (e.g., quenching and holding time too long) may lead to coarse grains or overcooking, triggering cracking in subsequent processing.
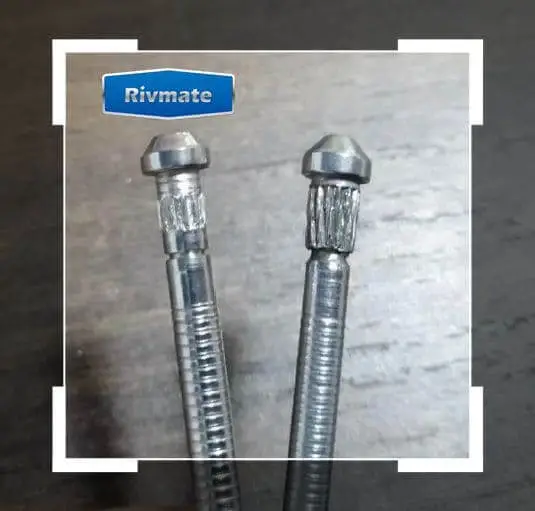
Manufacturing Defects
If the rivet processing process produces folding cracks (such as chamfer folding caused by improper upsetting process), surface scratches or dimensional deviations, it will become a source of stress concentration and accelerate crack expansion. For example, a nail due to the installation of the chamfer at the formation of folding cracks, followed by stress corrosion fracture in a corrosive environment.
II. Mechanics and load factors
Mounting hole coaxiality deviation will lead to abnormal bending stresses on the rivet, superimposed on the working shear stress is easy to cause fatigue fracture. For example, an aircraft rivet due to frame and skin mounting hole deviation, resulting in excessive starting stress and fatigue failure.
It should be noted that tensile stress is more likely to cause fatigue rupture than compressive stress, and high-frequency vibration load will accelerate crack expansion. Research shows that the fatigue life of rivets is negatively correlated with the stress level, and the crack expansion cycle is shortened under high stress.
Exceeding design loads (e.g. shock loads or sustained overloads) can also cause rivets to yield or fracture instantaneously.
III. Environmental and corrosion factors
Hydrogen embrittlement or stress corrosion cracking can occur if rivets are exposed to wet, acidic or hydrogen-containing environments. For example, brittle fracture occurs under sustained loads after corrosion at the chamfer of a weld stud.
Low and medium strength steels have a toughness and brittleness transition temperature (TK), below which the material changes from ductile fracture to brittle deconstructive fracture. If the rivet is used in low temperature environment, need to consider the low temperature performance of the material to match.
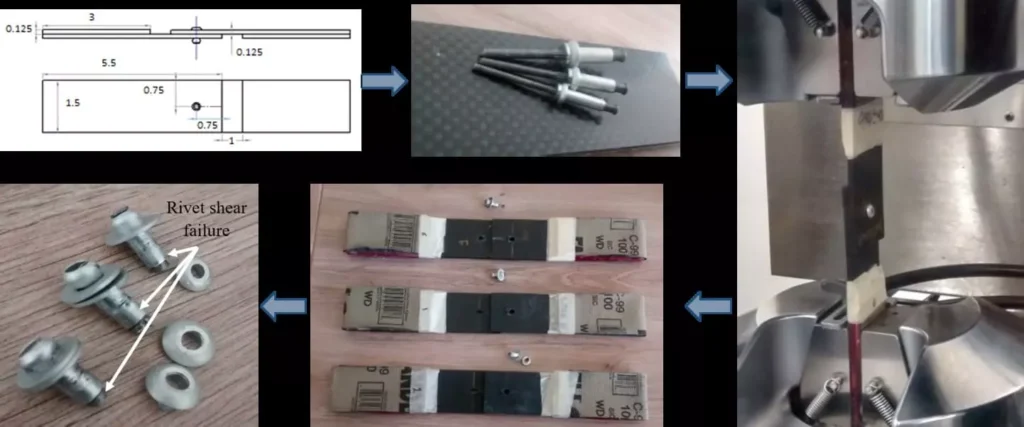
IV. Design and process factors
Structural design flaws can also lead to rivet breakage. Improper design of the rivet hole transition area (e.g., too small a radius) can lead to stress concentrations. For example, the rivet head arc transition due to the lack of reasonable transition design and become a source of fatigue, will lead to rivet stress concentration fracture.
v. other integrating factors
- Fatigue Characteristics: Fatigue fracture of rivets is usually characterized by a high percentage (>95%) of the fracture extension zone, and the source zone is characterized by multiple line sources. The quantitative backpropagation of the fracture can estimate the initial stress and extended stress, which provides a basis for improving the design.
- Multi-factor coupling effect: In actual engineering, rivet fracture is often the result of superposition of multiple factors. For example, in one case, the mounting hole deviation (design problem) and airflow vibration (environmental load) together lead to fatigue failure.
Do You Have Any Questions?
Let Us Solve Your Problem
How to Test the Breaking Strength of Rivets
The test method of rivet breaking strength is mainly realized by tensile test. The scientific and reliable nature of the test is ensured by incorporating industry standards and codes. The following is a comprehensive description of specific methods and related standards.
Testing Principles and Core Methods
Tensile Test Principle: Apply axial tensile load to the rivet until it breaks through the universal material testing machine, and record the maximum tensile value to determine the breaking strength. During the test, it is necessary to ensure that the rivet and the fixture are coaxial to avoid bias load affecting the results.
Key test steps
- Sample preparation: Randomly take representative rivet samples, check the appearance of no cracks, loose and other defects, record the number.
- Equipment calibration: Use universal material testing machine (such as KZ-DSC-20 type), calibrate the force transducer and displacement transducer to ensure that the accuracy meets the national standards.
- Fixture Selection: Customized high-strength steel fixture, matched with rivet size, to prevent slipping or damage to the sample.
- Parameter setting: Test speed is usually 5 mm/min, test temperature is controlled at room temperature (20~25℃), upper limit of force value is set according to rivet specification (e.g. 700N).
- Data recording: real-time monitoring of the force curve and displacement, recording the maximum tensile value and fracture location, taking photos of the deformation for analysis
Industry Standards and Codes
- ASTM F606/F606M: General Test Standard for Mechanical Fasteners, Including Tensile Test Methods.
- ISO 898-1: Requirements for mechanical properties of bolts, screws and studs, partly applicable to rivets test
Test equipment and key parameters
Core Equipment
- Universal material testing machine: such as KZ-DSC-20 type, support tensile, compression and other modes, equipped with high-precision sensors.
- Customized fixture: need to be designed according to the shape of rivets, made of rust-proof high-strength steel to ensure stable clamping.
Do You Have Any Questions?
Let Us Solve Your Problem
The Breaking Strength of Rivets Considerations in Practical Applications
In the construction and automotive sectors, the breaking strength of rivets is a core indicator of structural safety and durability. The following are key factors to consider when selecting rivets for different applications.
Construction
Building structures (e.g. bridges, steel structures) need to choose rivets according to the type of load. Bridges subjected to alternating stresses need to prioritize the selection of rivets with high fatigue strength (e.g. ML30CrMnSiA steel rivets), while ordinary building structures can choose lower-cost carbon steel rivets.
If your project is in a wet or coastal environment, in order to avoid stress corrosion fracture, prefer stainless steel or galvanized rivets.
In addition to this, the riveting process and structure should also be designed. Rivet spacing and margins need to be designed according to code requirements. Rivet spacing ≥ 3d (d for diameter), side distance ≥ 1.7d (convex head) or ≥ 2d (countersunk head).
Automotive
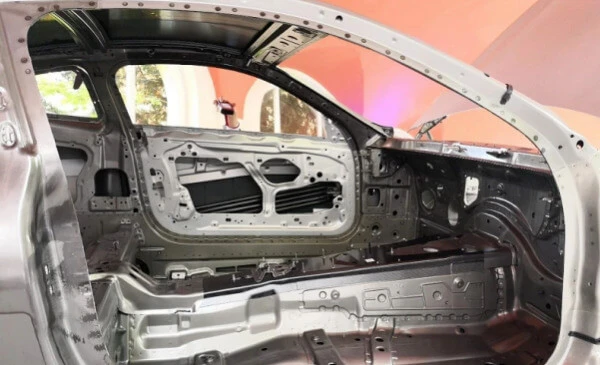
There are many types of materials that need to be riveted in automobiles. So the joining of dissimilar materials needs to be considered. Aluminum alloy, carbon fiber and other lightweight materials need to use self-pierce rivets (SPR) or BOM rivets, through the ring groove locking technology to achieve high shear resistance, to avoid breakage due to the difference in material hardness.
The vibration environment of the car is also a key consideration. BOM rivets are recommended for areas where vibration is frequent, such as automobile chassis.
Automotive body rivets need to meet the fatigue test of the automotive program. Generally need to meet the hard hitting test standard of 50kg or more.
Rivet Breakage Failure Case Study
Cadmium brittle fracture (liquid metal embrittlement)
Fracture of aero-engine 30CrMnSiA countersunk head rivets, with fracture along the crystalline fracture pattern and cadmium residue detected.
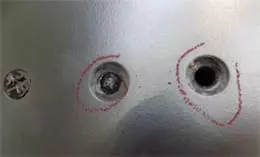
reasons
Rivet cadmium-plated layer melts at high temperatures, cadmium diffusion along the grain boundaries to weaken the bond, superimposed on the working stress leads to brittle fracture.
fatigue rupture
Bearing cage rivets after 400 hours of use nail head off, fracture showing fatigue strips and micro-motion wear marks; aircraft 15a frame and skin connection rivets fatigue fracture, fatigue zone accounted for more than 95%.
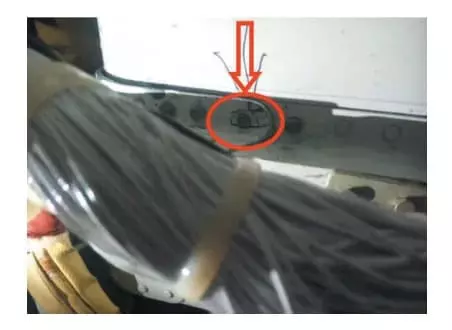
reasons
Excessive assembly clearance leads to micromotion wear, or mounting hole coaxiality deviation triggers abnormal bending stresses and superimposed vibration loads.
Material and workmanship defects
A gasoline engine clutch rivets fracture, metallurgical testing found that the grain boundaries three carburite chain distribution; riveting machine rivets cracking due to insufficient material strength or header process parameters.
reasons
Excessive material inclusions, improper heat treatment or riveting temperature control errors.
Custom Riveting Solutions for Your Project
By reading this guide, I’m sure you already have a good understanding of the basics of the breaking strength of rivets. This includes the factors that influence it, the problems that occur in its actual use.
A qualified and suitable rivets for your needs can bring you great economic benefits, and vice versa can be bad for your business. If you want to customize a professional riveting solution for your project, please contact our engineers.
Rivmate is the leading rivet manufacturer in china. get the rivet samples for testing now.