Strength of Welded vs Riveted Ship:A Comprehensive Guide
Table of Contents
In the field of ship structure design and maintenance, the strength of welded and riveted ship connections has always been a core issue in ensuring ship safety and performance. The quality of structural connections directly affects the ship’s ability to withstand wave fatigue, corrosion resistance, and service life.
This article will conduct a comparative analysis of the two primary connection methods—“welded and riveted hulls”. It can help readers gain a comprehensive understanding of their differences in terms of material strength, manufacturing processes, and maintenance convenience.
Why focus on the strength of welded and riveted ship?
Since the late 19th century, shipbuilding technology has undergone significant transformations, shifting from a process primarily based on riveting to one dominated by welding. As a traditional shipbuilding technique, riveting was widely used in the construction of steel structures for battleships and large ocean-going vessels. However, since the mid-20th century, welding technology has gradually replaced riveting as the mainstream connection method for modern ship hull structures due to its advantages in lightweight design, high continuity, and improved manufacturing efficiency. However, this transition has also brought new challenges, such as residual stresses generated by welding, embrittlement of the heat-affected zone, and the formation of micro-cracks.

In modern times, despite the high level of maturity achieved by welding technology, riveting technology still retains its application value in certain ship repairs and historical hull restorations. However, the differences between the two in terms of mechanical properties, aging mechanisms, and reliability under extreme marine environments remain critical technical issues in engineering design, quality assessment, and failure analysis.
What Are the Basics of Riveting and Welding in Shipbuilding?
a. Overview of Riveting Technology
Riveting is a method of using mechanical force to connect two steel plates with metal rivets to form a permanent structure. It was the primary structural connection technology in early shipbuilding. The process involves: pre-drilling holes, heating the rivets, forming them through stamping, and cooling to create clamping force.
In the early 20th century, especially during World War I and World War II, most merchant ships and warships (such as the “Titanic” and “Missouri”) used riveted structures. Common materials include carbon steel and medium-strength structural steel, with rivets typically being solid cylindrical in shape, relying on construction experience to ensure quality.
The advantages of riveting include high connection reliability, controllable process, and strong fatigue resistance. However, it also has limitations such as low construction efficiency, heavy weight, and high labor costs.
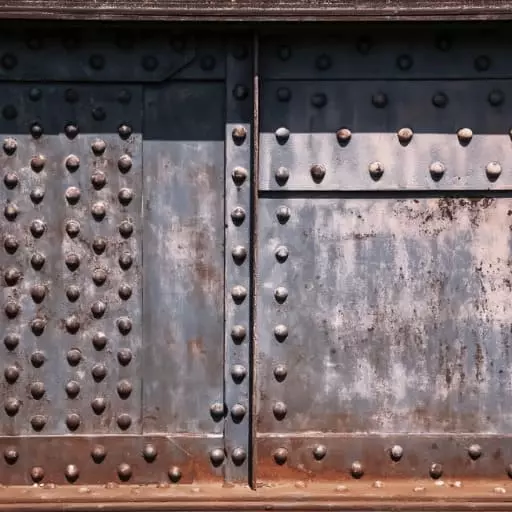
b. Overview of Welding Technology
With the development of arc technology and materials science, welding technology rapidly replaced riveting as the mainstream process in the mid-20th century. Common welding methods include:
- MIG welding (Metal Inert Gas Welding): suitable for thin plates, high efficiency, and high automation;
- TIG welding (Tungsten Inert Gas Welding): high precision, suitable for stainless steel and aluminum alloys;
- Manual Metal Arc Welding (SMAW): Flexible operation, suitable for on-site maintenance and medium-to-thick plate connections.
The primary advantages of welding over riveting include better structural continuity, higher overall stiffness, weight reduction, material savings, and labor savings. Disadvantages include: significant thermal effects on weld quality, susceptibility to stress concentration, and high technical requirements for operators.
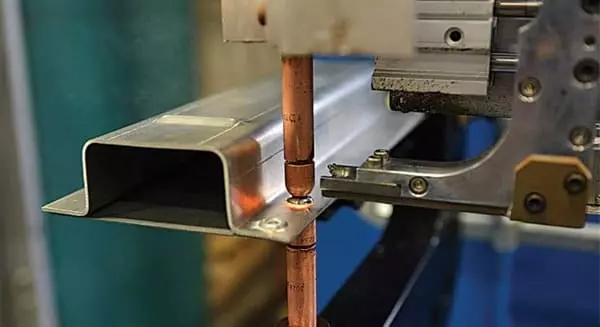
c. Technological Evolution Timeline: Transition from Riveting to Welding
- Mid-to-late 19th century: Riveting was the primary method for constructing steamship structures;
- 1910s–1940s: Riveting was widely used in warships and ocean-going vessels during wartime;
- 1950s onwards: Welding technology was standardized and gradually replaced riveting, being applied to main ship types such as oil tankers, warships, and container ships;
- After the 1970s: Modular shipbuilding became widespread, and automated welding technologies (such as welding robots and laser welding) developed rapidly;
- Currently: Welding has become the mainstream connection method, with riveting used only for minor repairs, cultural relic restoration, or special design requirements.
Strength of Welded vs Riveted Ship:What Are the Differences?
I. Differences in Structural Response under Static and Dynamic Loads
Under static loads, welded structures typically exhibit higher overall strength and stiffness due to their continuous connections and absence of sectional weakening. However, under dynamic loads (such as wave impact, propeller vibration, and navigation loads), structural rigidity may instead lead to stress concentration, particularly at welded joints.
In contrast, riveted structures, though slightly less rigid, possess a certain degree of flexibility due to their point-like, discrete connections, enabling them to absorb part of the local stress under dynamic loads and exhibit better load-distribution capabilities. This is particularly evident under conditions of repeated impacts or irregular waves, where the structural response is more moderate.

II. Stress concentration and crack propagation in welded joints
The strength of welded joints is typically higher than that of the base material, but their heat-affected zones (HAZ) are prone to stress concentration and microcrack initiation points. Especially in areas such as thick plate joints, large transverse welds, and corner welds, geometric discontinuities and metallurgical changes can reduce local fatigue strength. If stress is not properly distributed, microcracks may rapidly propagate under high-cycle cyclic loads, leading to sudden structural failure.
Additionally, residual stresses generated during welding can compound external working loads, reducing fatigue life, especially in seawater corrosion environments where weld zones are more prone to becoming initiation points for stress corrosion cracking (SCC).
1. Stress Concentration and Microcrack Initiation in the Heat-Affected Zone (HAZ)
The heat-affected zone is the region adjacent to the weld where the base material undergoes thermal cycling but remains unfused. The microstructure in this region undergoes recrystallization, hardening, or softening, often forming non-uniform structures such as martensite or bainite, leading to:
- Increased local hardness, reducing fracture toughness;
- Discontinuous microstructure, prone to initiating initial defects;
- Concentration of residual stresses from processing, reducing material plasticity.
2. Residual Stress Superposition Effect
The welding process involves high-temperature melting and rapid cooling, introducing residual tensile and compressive stress fields in the weld center and surrounding materials. Typical characteristics include:
- Residual tensile stresses in the weld zone can reach 60–80% of the base material’s yield strength;
- Tensile stresses and actual working stresses act in combination, causing the critical strain for crack initiation to be reached prematurely;
- Compressive stress zones may release stress in the opposite direction under subsequent vibration or corrosion, causing structural stress fluctuations.
3. Fatigue Crack Propagation Path and Rate Control
Once microcracks initiate, their propagation behavior is influenced by multiple factors including material toughness, plate thickness, and load frequency:
- Under high-cycle fatigue conditions (>10⁶ cycles), cracks propagate at a stable rate along the weld toe (the interface between the weld and the base material);
- If an external corrosive medium (such as seawater or electrolyte) is present, it can easily induce stress corrosion cracking (SCC);
- Crack propagation rates follow Paris’s law:
Δa/ΔN = C(ΔK)ⁿ, where ΔK is the range of stress intensity factors.
Experiments show that in welds where residual stress elimination measures have not been taken, cracks enter an uncontrollable growth zone after 10⁵–10⁶ cycles, causing a sharp decline in the remaining structural life.
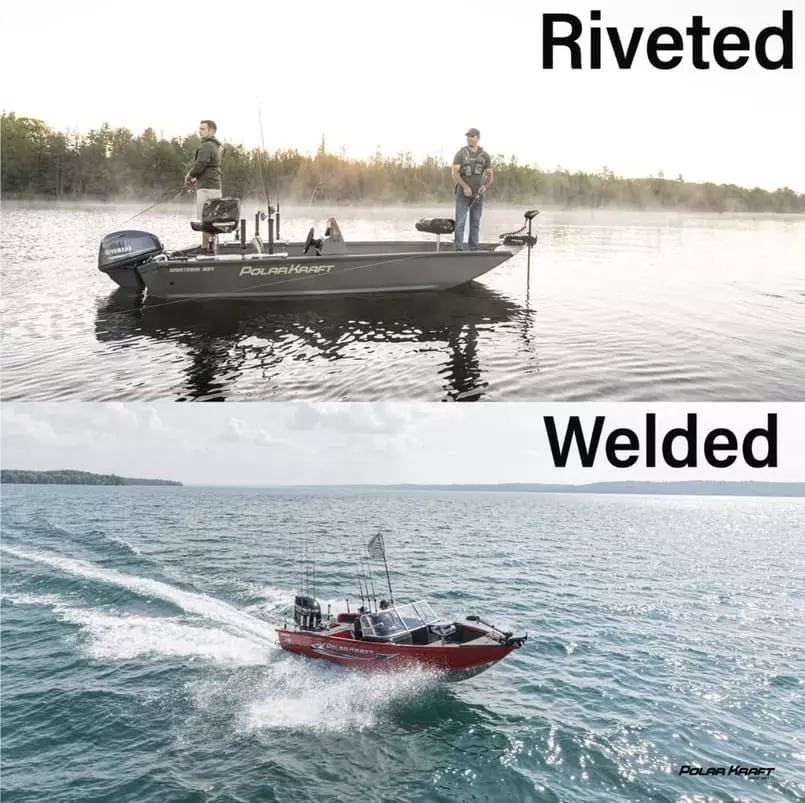
III. Stable Performance of Riveted Structures in Terms of Fatigue Life
Although riveting is a traditional process, it demonstrates stable durability under repeated loads and high-cycle fatigue conditions. The reasons are as follows:
- Rivet connections allow for slight displacement, which helps relieve stress.
- Rivets compress steel plates to create local preload, enhancing interface friction and effectively suppressing fretting;
- The failure of a single rivet does not immediately affect the overall structure, providing higher redundancy.
In wartime naval vessels and early merchant ships, riveted hulls demonstrated longer fatigue life and impact resistance, making them suitable for operating environments with drastic changes in speed and complex conditions.
IV. Comparison of corrosion resistance and sealing performance
Welded structures inherently offer superior sealing performance. Due to the formation of continuous joints through metal fusion, welded joints generally exhibit excellent watertight and airtight properties before cracking, making them particularly suitable for areas with stringent sealing requirements, such as fuel tanks, ballast tanks, and hull sections below the waterline. Under proper welding techniques and effective protective measures (e.g., coatings, cathodic protection), welded structures demonstrate strong corrosion resistance.
The weld zone is also a sensitive point for localized electrochemical corrosion. Especially in cases of weld spatter, slag inclusion, coating damage, or brittle transformation of the heat-affected zone, microcells may form, leading to pitting or crevice corrosion. Additionally, improper alloy combinations (such as stainless steel welded to carbon steel) may also cause galvanic corrosion.

In contrast, riveted structures have natural gaps and contact surfaces, which can serve as pathways for seawater infiltration and retention. Once coatings are damaged or rivets become loose, moisture can circulate within the interlayers, leading to typical crevice corrosion or oxygen difference battery corrosion. This is also the root cause of common issues such as rivet rust expansion, rivet loosening, and plate seam bulging in older riveted ships during their later service years.
However, riveting also has certain redundancy advantages: even if individual rivets corrode and fail, the overall connection structure will not immediately collapse, demonstrating a certain degree of fault tolerance. Additionally, riveted areas often use thick coatings or gap-filling materials to enhance protective performance, making them suitable for non-sealed compartments or deck attachment connections.
How to Choose Between Welded and Riveted Structures in Ship Design?
a. Structural Selection Preferences for Different Ship Types and Applications
In modern shipbuilding engineering, welding has become the mainstream connection process, but whether it will completely replace riveting still depends on the specific ship type, mission attributes, and service requirements:
- Commercial cargo ships and oil tankers: Emphasizing large-scale modular construction and structural rigidity, these vessels prioritize fully welded structuresto reduce weight, enhance cargo efficiency, and accelerate construction speed.
- Warships and destroyers: In terms of high-speed maneuverability and impact resistance, higher requirements are placed on structural fatigue strength and local redundancy. A hybrid design of main structure welding + local riveting reinforcementis generally adopted to enhance damage resistance and maintainability.
- Passenger ships and ferries: Emphasize comfort and safety redundancy, with high requirements for compartmentalization, fireproofing, and vibration suppression. Welding is primarily used, but riveting is still applied locally in decorative compartments or historical restoration projects.
- Submarines and special-purpose vessels: Sealing and pressure resistance are critical, necessitating fully welded airtight structures and comprehensive non-destructive testing.
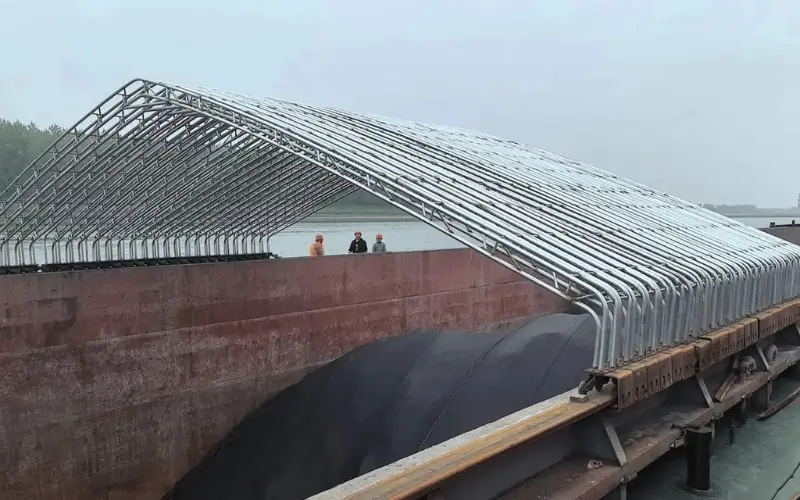
b. Engineering trade-offs between cost, strength, and lifespan
- Welded connectionstypically have lower manufacturing costs, higher material utilization rates, and support automation and modular prefabrication, making them suitable for industrialized mass production;
- Riveted connectionshave higher per-point costs and rely heavily on manual labor, but offer unmatched advantages in terms of fatigue lifespan and multi-point redundancy.
During the design phase, the relationship between the three must be balanced based on the service life, maintenance frequency, and load type. For example, for civilian ships with tight schedules but moderate service lives, welding is the preferred option; while military high-reliability platforms may use localized riveting to extend the service life of critical components.
c. Construction Cycle, Maintainability, and Long-Term Cost Considerations
- Welded structures have shorter construction cycles and higher automation levels, making them suitable for modern shipyard production processes. However, once welds crack or corrode, on-site repairs are challenging and require highly skilled personnel and specialized equipment;
- Riveted structures are relatively easy to repair, with damaged sections capable of being replaced individually, making them suitable for field repairs or emergency situations where welding equipment is unavailable;
- From a lifecycle costperspective, welded structures may incur higher maintenance costs, particularly in harsh environments (such as polar regions, tropical climates, or highly corrosive waters), which impose stricter requirements on surface protection and crack monitoring.
What Are the Future Trends in Welded vs. Riveted Ship Construction?
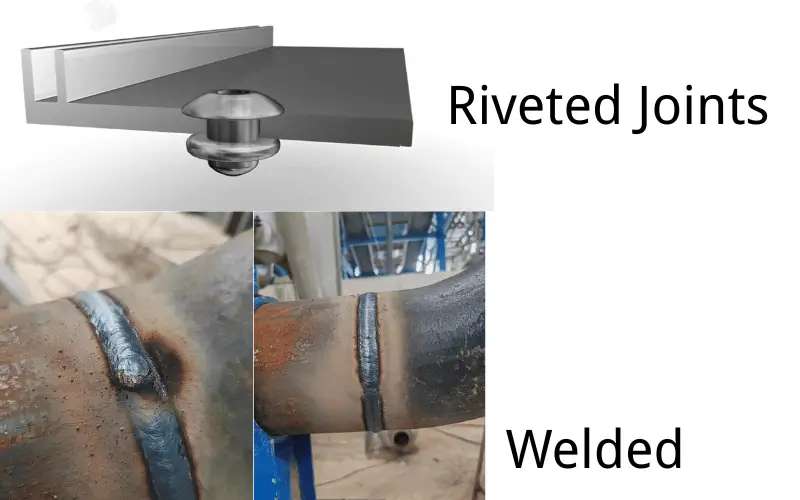
With the rise of multi-functional ships and complex platforms, single connection processes are no longer able to meet the comprehensive requirements of structural diversity, reliability, and maintainability. In recent years, more and more shipyards have begun to explore a composite structure strategy of “welding + riveting.” For example, continuous welding is used in high-stiffness areas such as the main keel and main beams of ship compartments, while riveting/screw fastening methods are retained or reintroduced for compartment partitions, non-structural attachments, and easily maintainable areas.
Additionally, with the advancement of smart manufacturing technology, automated welding equipment has become the mainstream construction method, particularly in modular shipbuilding, enabling efficient and consistent weld quality control:
- Laser welding, friction stir welding (FSW), and multi-axis arc welding robots are widely used for welding thin plates, irregular structures, and high-strength steel materials;
- Digital welding monitoring systems significantly reduce human error and defect rates through real-time temperature control, stress feedback, and visual tracking.
Sustainable shipbuilding
Under the global trend of carbon neutrality, the impact of connection processes on energy consumption, material recycling, and manufacturing carbon footprints has increasingly become a design constraint:
- Although welding has high material utilization, it has high heat input and energy consumption, especially in thick plate welding, where carbon emissions are significant;
- Riveting has lower energy consumption but high material addition rates and structural weight, which are unfavorable for fuel efficiency and emission reduction goals;
- Modern shipbuilding is gradually introducing “green connection” solutions such as removable fastening and non-thermal connections, with screw/clip-on interfaces already achieving preliminary application in equipment-level modules;
- Additionally, the recyclabilityof connection materials themselves (such as stainless steel and high-strength aluminum alloys) has become one of the evaluation criteria, driving the full-chain greening from material selection to connection methods.
In the future, the selection of connection methods will not only be a structural mechanics issue but also a comprehensive reflection of energy efficiency, environmental compliance, and manufacturing intelligence levels.
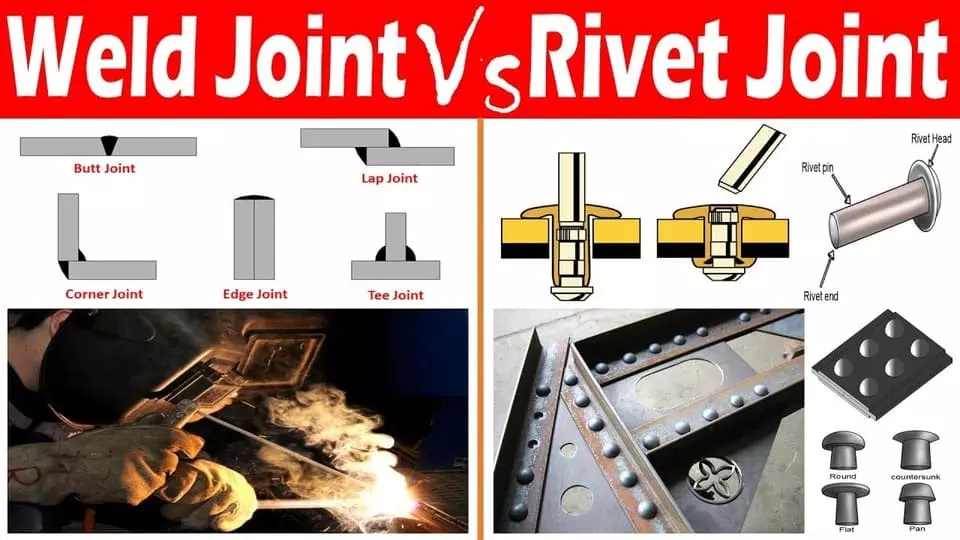
Welded or Riveted Ship: Which One to Choose?
In the contemporary shipbuilding and repair industry, the core logic behind choosing between welding and riveting is primarily based on the following points:
- Structural Strength and Sealing Performance
Welded joints offer superior structural integrity and sealing performance, making them suitable for withstanding high-strength loads and harsh environments; Riveted joints, while structurally stable, have minor gaps compared to welded joints, resulting in weaker sealing performance. - Manufacturing Efficiency and Cost Control
Welding processes have high automation levels, short production cycles, and are suitable for large-scale and rapid shipbuilding, with relatively lower costs; riveting is primarily manual labor, resulting in longer cycles and higher labor costs. - Maintenance and Replacement Convenience
Riveted structures allow for localized disassembly and replacement, with repairs requiring no damage to large structural areas; welding structures are complex to repair and require specialized welding equipment and skills. - Material Adaptability and Durability
Welding has higher material requirements, with some high-strength or special alloys being difficult to weld; riveting has a broader application range, particularly for thin plates or connections between different materials.
Table: Suggestions for Different Roles in Welding and Riveting Selection
Role | Preferred Connection Method | Key Considerations | Explanation & Application Suggestions |
Shipyard | Welding as primary, riveting as secondary | Production efficiency, structural strength, modular construction | Suitable for large-scale, high-efficiency shipbuilding; use riveting in areas requiring maintenance or disassembly to form hybrid joints |
Investor | Welding prioritized | Cost-effectiveness, maintenance cycle, service life | Welding offers better economic value; however, vessels with frequent maintenance needs or special purposes should consider the flexibility and maintainability of riveting |
Maintenance Team | Riveting is more convenient | Ease of repair, technical requirements, work environment | Riveting allows for easier localized replacements; welding repairs require skilled labor and equipment, and should be supported by a professional team to ensure quality |
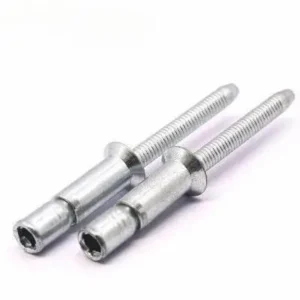
What is the Difference Between Countersunk Rivets and Regular Rivets? – Rivmate Expert Guide
What is the Difference Be
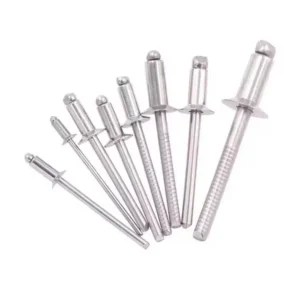
What are Countersunk Blind Rivets Used for?
What are Countersunk Blin
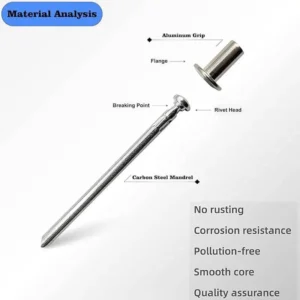
Problem with Rivet Mandrel Breaking
Problem with Rivet Mandre
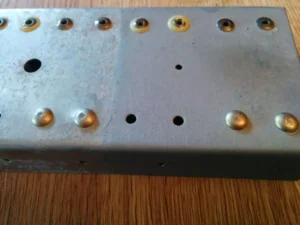
Rivet Corrosion: Causes, Prevention, and Engineering Solutions
Rivet Corrosion: Causes,