Table of Contents
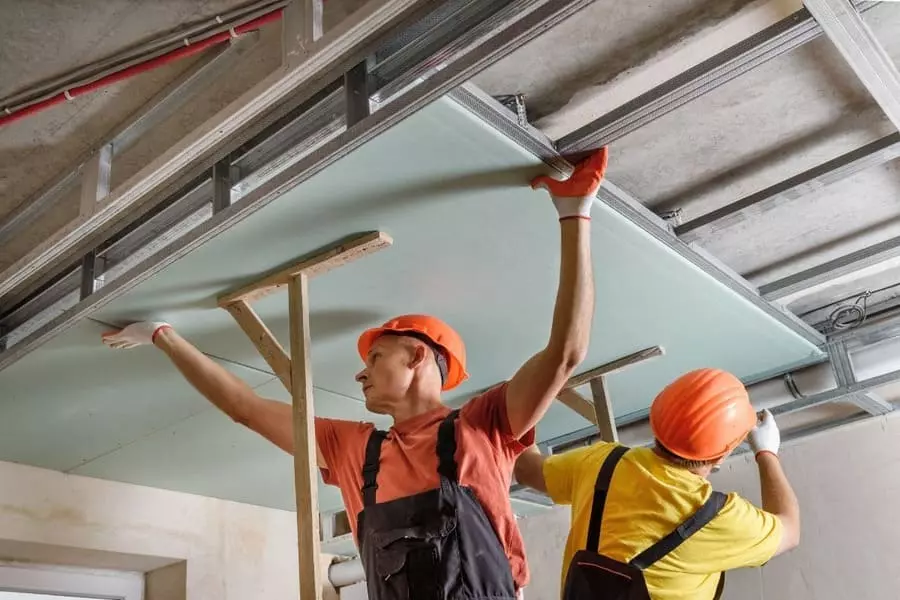
Metal furring is an important part of ceiling construction. Therefore the safety of metal furring is very important. Blind rivets for metal furring offers an excellent solution to increase efficiency while keeping metal furring projects safe.
By reading this blog, you will learn the definition of metal furring, advantages of blind rivets for metal furring, applications and how to choose the right metal furring blind rivets.
Table of Contents
What is Metal Furring?
Metal Furring (metal keel or metal skeleton) is a metal structural component used in construction to support walls, ceilings, or other surface finishes. This structure is usually made of galvanized steel or aluminum alloy. Its primary function is to create voids, level uneven substrates, and provide support for interior and exterior cladding materials (e.g., gypsum board, cement board, metal panels, etc.).
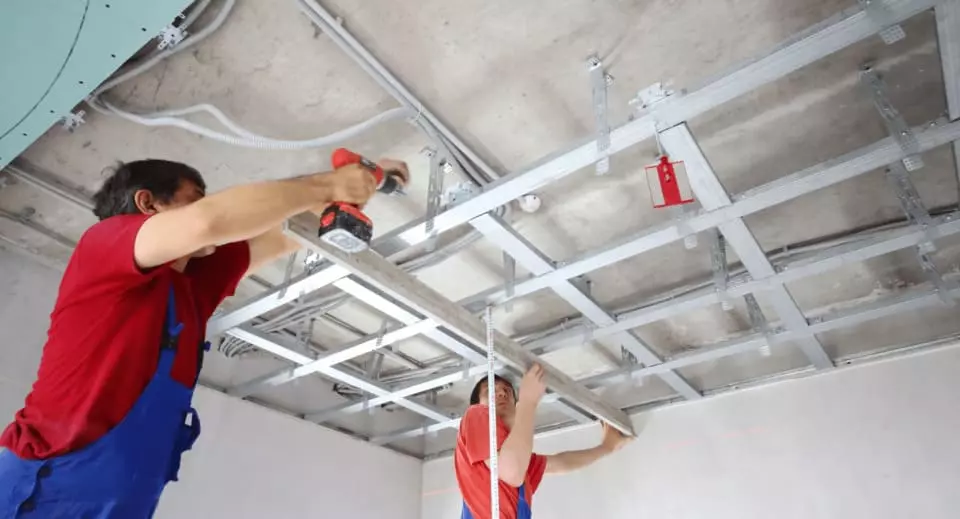
Primary Uses of metal furring
- Leveling Surfaces: used on walls or ceilings to straighten uneven substrates (e.g. concrete walls, brick walls, etc.) and provide a smooth mounting plane.
- Insulate moisture and temperature: reduce condensation infiltration and improve thermal and acoustic insulation performance through the gap (called cavity) between the metal keel and the substrate.
- Conceal piping: wires, pipes or insulation materials can be installed in the cavity to keep the surface tidy.
- Fire & Moisture Resistance: Compared with wooden keel, metal material is non-flammable and corrosion resistant, suitable for high humidity areas (e.g. bathrooms) or places with high fire resistance requirements.
Common Types of metal furring
- C-shaped keel: commonly used for drywall or lightweight partition walls.
- Z Studs: Used for complex structures where unevenness needs to be adjusted.
- Metal Studs: Similar to wood studs, but made of lightweight steel, used to frame partition walls.
- Hat Channel: Hat-like in cross-section, commonly used in suspended ceiling systems to provide effective load-bearing and cavity space.
Why Use Blind Rivets in Metal Furring?
1. Unilateral handling capability: efficient fixation in confined spaces
When installing metal studs where the fixing points cannot be reached from the back (e.g. inside a suspended ceiling, inside a wall or working at height), blind rivets allow fixing to be done on one side, making them particularly suitable for concealed work.
Blind rivets are a key option when connecting ceiling studs to the main structure, where workers can only work from below and cannot access the back side.
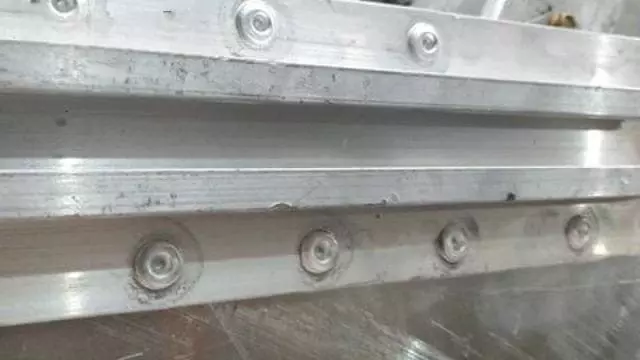
2. High strength and vibration resistance
Blind rivets have high shear strength (such as stainless steel rivets can withstand more than 500-1000 psi load), can firmly fix the keel, to avoid the cladding materials (such as gypsum board, stone) due to the connection point of the loosening and cracking.
Blind rivets are more suitable for high vibration environments than screws, which tend to loosen under long-term vibration, and “rivet” holes through plastic deformation.
3. Material compatibility and corrosion resistance
Metal furring is mostly galvanized steel or aluminum alloy. To prevent galvanic corrosion, blind rivets made of aluminum, stainless steel or galvanized are available.
Rust resistance is especially important in high humidity environments such as bathrooms and kitchens. And blind rivets can significantly extend the life of the keel system.
4. Rapid installation and cost savings
Rivet installation requires only a rivet gun. It eliminates the need for drilling, tapping or welding steps (the latter requires specialized equipment and skills) and improves construction efficiency by more than 50%.
For example, compared to welding a single node takes 2-3 minutes, blind riveting takes only 10-20 seconds, significantly reducing labor costs.
5. Lightweight and flat surfaces
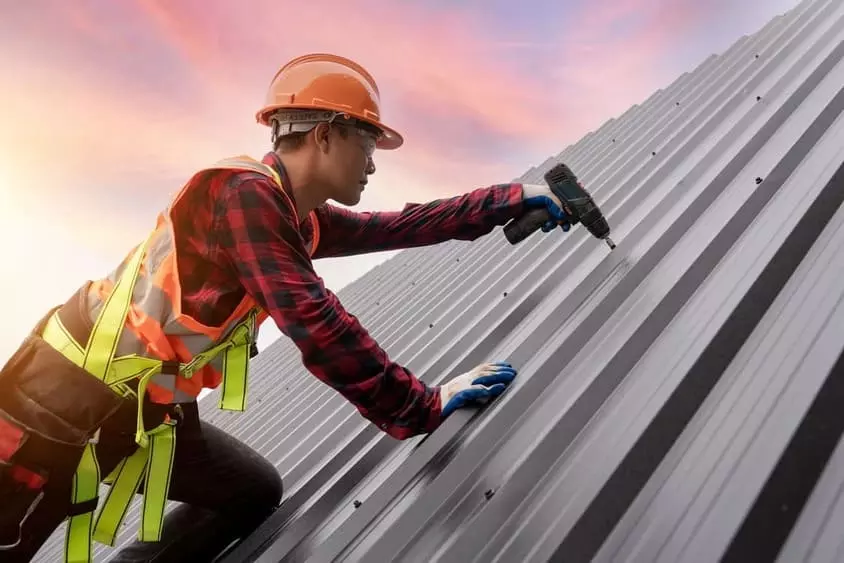
Blind rivets are lightweight and do not add burden to the keel system. And the head of the rivet is flattened to provide a smooth joint. This facilitates the fit of subsequent cladding materials (e.g. thin sheet metal) and avoids uneven surfaces caused by protruding screws.
6. Permanent fixation and regulatory compliance
The connection provided by blind rivets is a permanent one. Requirements such as fire rated partitions do not allow for random dismantling, so this is fully compliant with building safety codes. In addition, some fire rated blind rivets (e.g. stainless steel or special coatings) can be used in conjunction with metal studs to meet building fire standards.
Do You Have Any Questions?
Let Us Solve Your Problem
Applications of Blind Rivets for Metal Furring
The application scenarios of blind rivets in metal furring are mainly based on their characteristics of single-sided riveting, high clamping force and vibration resistance. The following are common application scenarios.
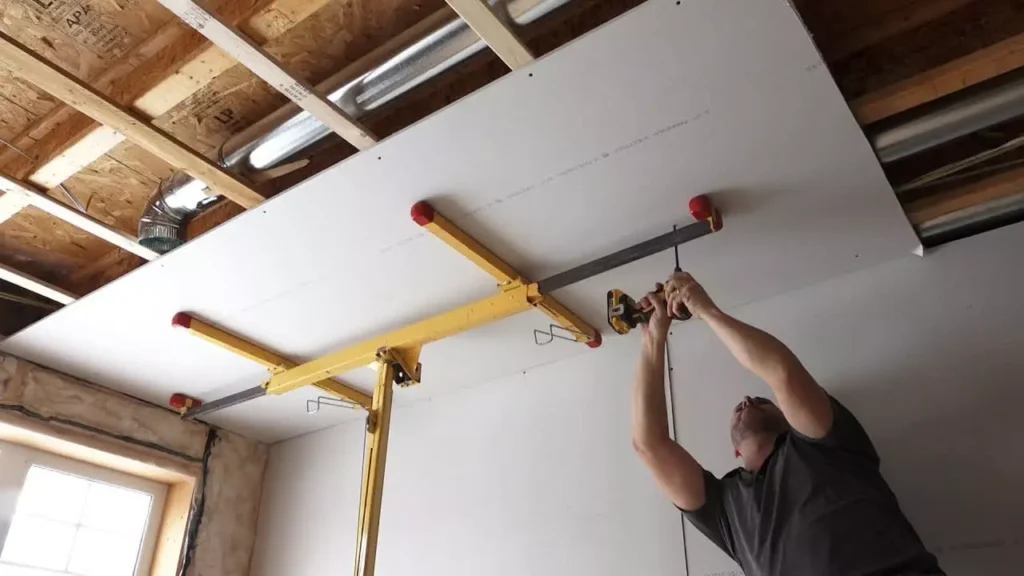
- When fixing gypsum boards, metal panels or other cladding materials to metal keels.
- In the transverse or longitudinal splicing nodes of light steel keel frames, blind rivets can quickly connect the keel members and enhance the overall structural stability.
- Fixing of suspended components in non-high stress areas such as ceiling light fixtures and pipe supports.
- Fixing of metal ventilation ducts with keel frames.
- In the temporary positioning of the metal support frame of the curtain wall, core-pulling rivets can be used as a fast installation of transitional connectors.
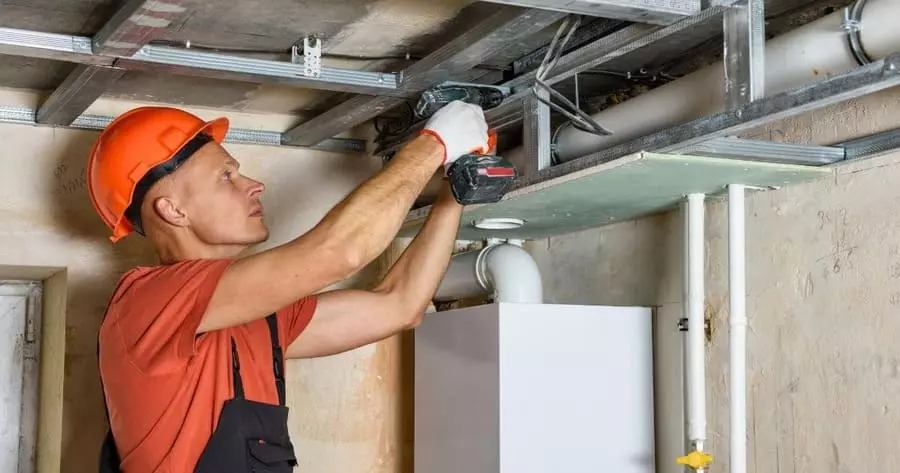
How to Choose Blind Rivets for Metal Furring?
Step 1: Determine material compatibility
First you need to determine the material of the metal furring.
- Galvanized steel: use galvanized steel, stainless steel (such as 304/316) or aluminum blind rivets to avoid galvanic coupling corrosion between materials.
- Aluminum alloy: priority with aluminum or stainless steel blind rivets (need to add insulating gaskets to isolate dissimilar metal contact).
It should be noted that: if the cladding is weathering steel plate, the rivets should be selected with high rust resistance (e.g. passivated stainless steel).
Step 2: Define the load type
Vertical joints (such as metal plate splicing) need high shear performance (choose structural rivets, such as BOM Rivets series, shear strength of 15KN). And the negative wind pressure area of the roof is preferred to use large flange head blind rivets (tensile strength ≥ 8KN).
Step 3: Evaluate operating conditions
If the installation environment is narrow, then small diameter rivets (e.g. 1/8″ hole) and short shank rivet guns (e.g. straight shank type) are required.
If the metal furring is located in a high-temperature environment, heat-resistant aluminum bronze rivets (operating temperature ≤ 200 ° C) should be selected; in wet areas, sealing type rivets (with EPDM rubber ring, such as AVDEL® Monobolt) should be selected.
Step 4: Calculate the sandwich thickness
Formula: Rivet length = total thickness of the jacket + 0.5 x nail sleeve expansion allowance
(Example: Jacket 3mm, recommended rivet clamping range 2.5~3.5mm, length selection 6-8mm).
Recommended Selection Reference Table
Application Scenario | Rivet Type | Recommended Specifications | Compliance Standards |
Light steel frame partition wall splicing | Aluminum blind rivets | Ø4.8mm × 12mm length | ASTM B316 (Aluminum Rivet Wire) |
Metal roof wind uplift nodes | Stainless steel structural rivets | Ø6.4mm × 20mm length | ISO 15977 (Mechanical Lock Rivets) |
Humid area ceilings | Sealed rivets | Ø5.0mm × 15mm length | DIN 7337 (Sealed Blind Rivets) |
Fire-rated partitions | Ceramic-coated steel rivets | Ø5.0mm × 18mm length | UL 1479 (Fire Endurance Test) |
Do You Have Any Questions?
Let Us Solve Your Problem
Frequently Asked Questions (FAQs)
Rivet pulls off mandrel or nail sleeve not fully expanded
This phenomenon can lead to excessive clearance between the metal keel and the substrate due to a broken but insufficient clamping force of the nail bar after riveting.
As long as through the thickness gauge (such as vernier calipers) measured value of the sandwich, select the length of the specifications for the “sandwich thickness +5mm” rivets can be solved.
Improperly protruding or recessed rivet head
Countersunk head rivets are not fully embedded in the plate, or the spacing between the convex head rivets and the keel is out of tolerance (allowable deviation ± 0.3mm).
- Pre-chamfer using a stepped drill bit (chamfer depth = plate thickness x 0.3).
- Adjust the riveting force until the nail head is flush with the surface but does not crush the plate (refer to ISO 15978 standard, carbon steel rivet limit crush force 8KN).
Rivet slippage or breakage under shear force
The cladding material disengages from the keel under wind loads and the rivet holes expand and deform.
This problem can be solved by using structural blind rivets (shear strength ≥15KN) or by reducing the rivet spacing from the conventional 400mm to 200mm.
Custom Riveting Solutions for Your Metal Furring Project
The safety of the metal furring is very important for the renovation and construction of the house.Therefore.Therefore, howTherefore, how can youTherefore, how to make your metal Therefore, it is crucial to know how to choose the right blind rivets for your metal furring project.
Please ask us for rivet samples for testing before placing a formal order. This way you can be sure that the blind rivets are perfectly suited to your project.
Get Rivets Quote
You may also find these topics interesting
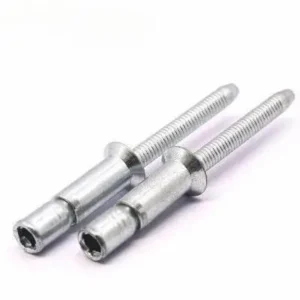
What is the Difference Between Countersunk Rivets and Regular Rivets? – Rivmate Expert Guide
What is the Difference Be