Table of Contents
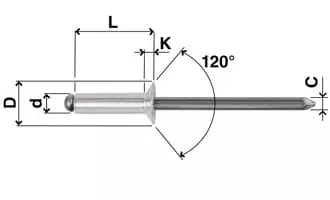
Why is the Countersunk Rivet Head Angle Important? If an inappropriate countersunk rivet head angle is used, it is likely to lead to serious consequences, even connection failure. So choosing the right countersunk rivet head angle is crucial for your business.
By reading this guide, you will learn the basic definition, importance, types and factors to consider for countersunk rivet head angle.
Table of Contents
What is the Countersunk Rivets Head Angle?
The countersunk head angle of a countersunk head rivet refers to the angle of the tapered portion of its head, usually with 100° as the most common standard. Depending on the application scenario and industry standards, there also exist 90°, 120° and other angle designs.
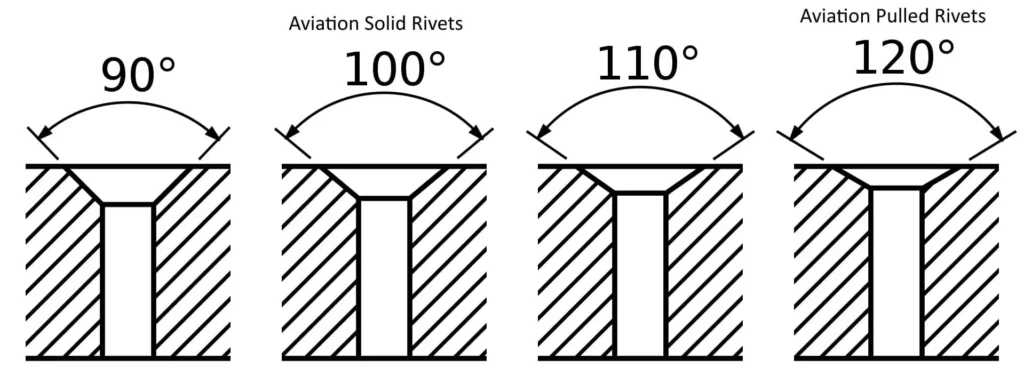
Aerospace uses 100° or 130° countersink angles more often, while 90° in sheet metal working is suitable for softer materials. The countersunk head angle determines how well the head of the rivet fits the surface of the material after riveting. The smaller the angle, the shakier the taper; the larger the angle, the flatter the taper.
The correct choice of countersink angle ensures:
- The surface is flat and free of bulges after riveting.
- Uniformity of force and avoidance of stress concentration.
- Compliance with industry specifications.
Why Is the Countersunk Rivet Head Angle Important?
The countersunk head angle of countersunk head rivets is important because it directly affects the structural performance of the riveted joint, the installation effect and the suitability of the application scenario.
1. Ensuring structural strength and load distribution
The countersunk head angle determines how well the rivet head fits the material contact surface. Mismatched angles (e.g., countersunk hole angle greater than rivet angle) will result in only edge contact of the rivet head, resulting in localized stress concentrations and reduced joint strength.
The correct angle (e.g. 90°) allows the rivet head to fit perfectly into the countersunk hole, spreading the load over a larger area and avoiding localized overloads that could lead to deformation of the material or loosening of the rivet.
2. Ensuring surface flatness
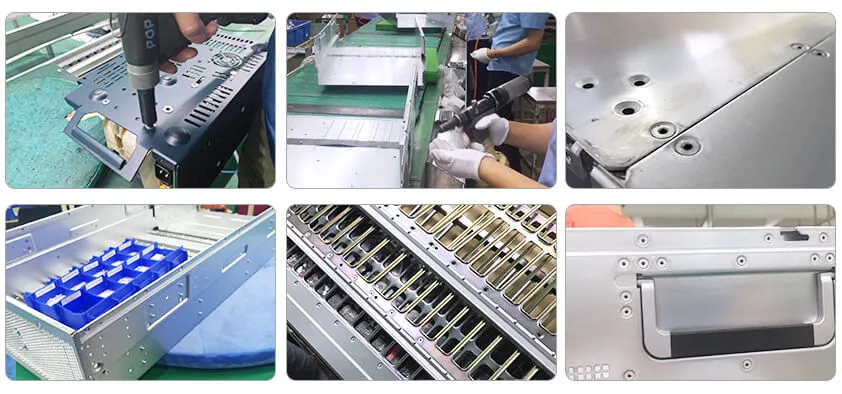
When the countersunk head angle is the same as the countersunk hole angle, the head of the rivet can be fully embedded in the surface of the material for a smooth transition. If the angle deviates (e.g. 90° for rivet angle and 85° for countersunk hole), the head may protrude or sink, affecting appearance and function.
Special scenarios have very high requirements for surface flatness. For example, aircraft skins require rivet heads to be perfectly flush to minimize air drag; electronics housings need to avoid bulges that can affect tactility or assembly.
3. Optimization of the installation process
When the countersunk head angle is matched to the countersunk hole, the rivet is automatically centered during the press-in process, reducing the risk of installation deflection. Angular deviations can cause the rivet to tilt, reducing the reliability of the connection.
If the countersink angle is slightly less than the rivet angle (e.g. 89° vs. 90°), this compensates for machining errors and ensures a tight fit of the rivet head.
4. Adaptation to different material properties
- Soft materials (e.g. aluminum, plastics): using a smaller angle (e.g. 82°) reduces the risk of crushing deformation or cracking of the material during riveting.
- High strength materials (e.g. titanium alloys): a larger angle (e.g. 100°~130°) may be required to balance the material hardness and riveting force to avoid chipping of the countersunk edges.
Do You Have Any Questions?
Let Us Solve Your Problem
Types of Countersunk Rivet Head Angle
There are many types of countersunk rivet head angle to suit different application scenarios and materials.
90° Countersunk angle
90° Countersunk angle meets ISO 1051, GB/T 869 (China), DIN 6797 (Germany), JIS B 1211 (Japan) standards for design.90° Countersunk head rivets are commonly used in machinery, sheet metal fabrication, and building structures.
The characteristics of the 90° Countersunk angle are as follows:
- The most widely used standard angle, easy countersunk hole processing, strong compatibility.
- Flat surface after riveting, suitable for scenes with basic requirements for appearance.
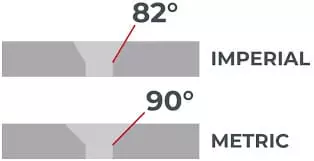
82° Countersunk angle
82° Countersunk head angle in accordance with ANSI/ASME B18.1.2 (U.S.), some aerospace standards. Mainly used on soft metals (e.g. aluminum sheet, copper) or plastic parts. You may see 82° countersunk head rivets in automotive interiors, electronic equipment housings and other scenarios where deformation of the material needs to be avoided.
The features of this countersunk head rivet are as follows:
- Steeper taper reduces the risk of extrusion deformation on soft materials.
- Requires matching 82° countersunk holes, commonly used in the American Standard system.
100° Countersunk angle
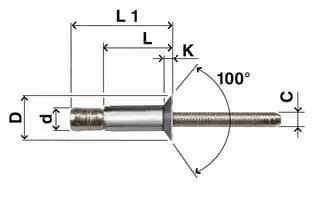
The 100° countersink angle meets NASM/MS (aviation standards), some military specifications. Aircraft skins, spacecraft structures and high-strength alloys are joined using a large number of 100° countersunk head rivets.
These rivets are characterized by a smoother taper and greater load dispersion for high stress scenarios.
120° or 130° countersunk head angle
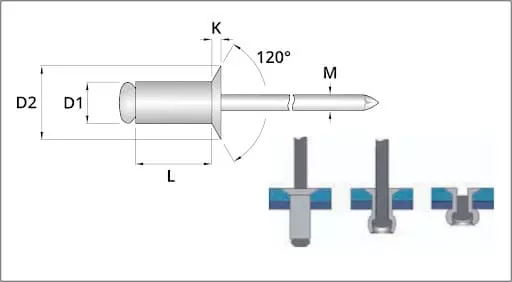
The 120° or 130° countersink angle is customized for special industries (e.g. ships, heavy machinery).
If your project requires the joining of extra thick plates or composites, or if you need extremely low surface projection, then 120° or 130° countersunk head rivets are a good choice.
After installation, the head of the rivet is almost perfectly flush with the surface of the material.
Countersunk Rivet Head Angle Chart
Scenario | Recommended Angle | Rationale |
General sheet metal fabrication (steel/aluminum) | 90° | Low cost, easy processing, and strong compatibility. |
Lightweight aluminum panel connections (automotive) | 82° | Reduces deformation in aluminum, compliant with ANSI standards. |
Aircraft skin riveting | 100° | Distributes aerodynamic loads and meets high-strength aviation requirements. |
Thick composite structures (e.g., marine) | 120°–130° | Ensures flush surfaces to prevent corrosion or drag. |
Do You Have Any Questions?
Let Us Solve Your Problem
Factors to Consider for Countersunk rivet Head Angle
When selecting the head angle of a countersunk head rivet, in order to ensure joint strength, functionality and economy. The following key factors need to be considered:
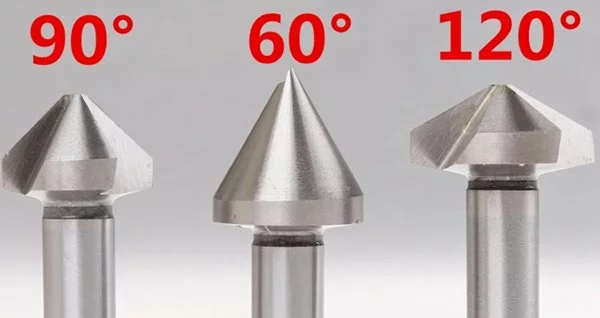
- Material Characteristics: Prefer 82° countersunk head rivets when your project is a soft material. For hard materials, 90° countersunk head rivets or 100° countersunk head rivets are more appropriate.
- Material thickness: Use countersunk head rivets with small angle (82°~90°) for thin plates (<3mm) to avoid penetration or deformation. Thick plates or composite materials use large angle (100°~130°) countersunk head rivets to enhance load carrying capacity.
- Load type: Shear dominated selection of 90° countersunk head rivets. Tensile force dominant selection of 100 ° or greater angle countersunk head rivets.
- Surface flatness requirements: high flatness requirements using 100 ° ~ 130 ° countersunk head rivets, general appearance of the choice of economical 90 ° countersunk head rivets.
Enhance your Business with Rivmate Riveting Solutions
The angle of countersunk head rivets used to join different materials is also different. By reading this guide, I’m sure you already know how to pick the best coutersunk rivet head angle for your project.If there are still questions about this, please contact our engineers.
Please obtain a sample rivet for testing before placing an official order.