Table of Contents
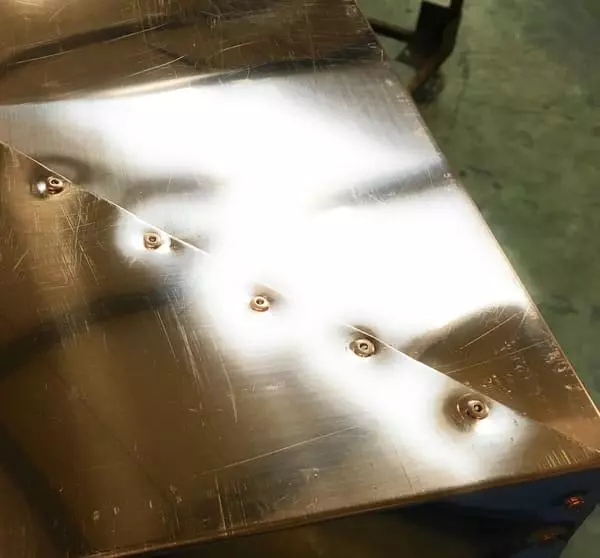
Copper sheets are a frequently used material. However, due to the characteristics of copper, it may cause corrosion when used in combination with other metals. Therefore you need to have a clear understanding of how to riveting copper sheets.
By reading this guide, you will learn about the reasons for riveting copper sheets, the types of rivets that can be riveted with copper sheets, the specific applications of riveting copper sheets, and how they compare to welded copper sheets.
Table of Contents
Why Riveting Copper Sheets?
Riveting copper sheets are particularly common in the architectural, decorative, electrical and craft manufacturing sectors. Here are a few of the main reasons for riveting copper sheets:
- Avoiding thermal effects (compared to soldering): The extremely high thermal conductivity of copper (approx. 401 W/m-K) makes it extremely easy for heat to diffuse when soldering or brazing. This may therefore lead to localized overheating, annealing, and discoloration of the part; difficult control of the weld; and damage to adjacent parts (especially in precision copper parts). Riveting, on the other hand, is a cold joining process that avoids heat affected zone (HAZ) problems.
- Easy on-site operation and maintenance: riveting can be implemented in the environment without electricity and gas source (e.g., construction of building roofs and facades); lower technical dependence on the construction personnel and higher safety compared to welding.
- Compatible with the performance of copper itself: copper is easy to oxidize, not resistant to high temperature impact, welding spot easy discoloration; riveted joints do not destroy the surface integrity, can maintain the original texture of copper or treatment layer; the use of copper rivets rivets, can avoid galvanic corrosion (especially on aluminum or iron material easy to cause corrosive damage).
- Traditional craftsmanship and aesthetics: in architectural copper trim (e.g. church roofs, copper rain gutters), riveting meets the aesthetics of traditional coppersmith craftsmanship.
- Safer in certain electrical situations: Copper is often used as a conductor in electrical engineering, and soldering can change the conductivity due to overheating. Riveting can provide mechanical fixing support without affecting the conductivity; for example, in high frequency applications, electromagnetic interference can occur at the soldering point, whereas mechanical connections are relatively stable.
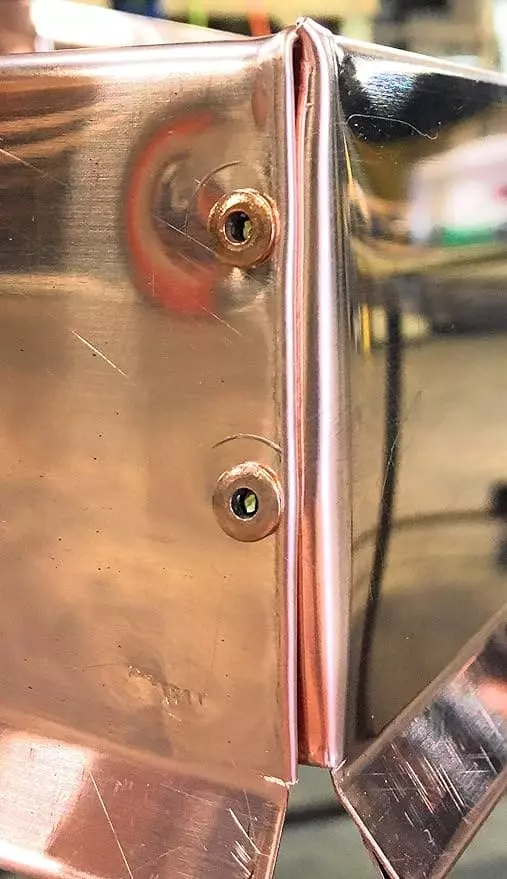
What type of rivet should be used when riveting copper sheets?
When riveting copper sheets, preference should be given to rivets with good compatibility with the copper material, high corrosion resistance and suitable mechanical properties. The following are the recommended types:
1. Solid Copper Rivets
Application: crafts, electrical grounding, building decoration
Advantages:
- Consistent with the copper sheet material, can avoid galvanic corrosion;
- Good ductility, suitable for hand riveting molding;
- High consistency of appearance, can be sanded and polished to blend naturally with the copper surface.
Limitations: low mechanical strength, not suitable for high load connections.
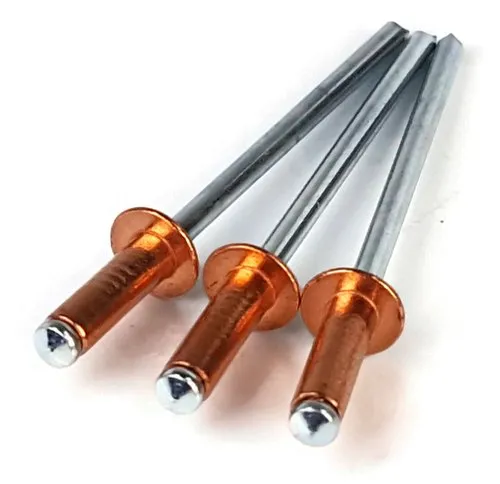
Applicable: structural strength requirements of slightly higher copper sheet connection
Advantages:
- Higher hardness relative to pure copper;
- Good electrochemical compatibility with copper, low risk of corrosion;
- Commonly used in construction, process equipment shells, vibration-resistant connections.
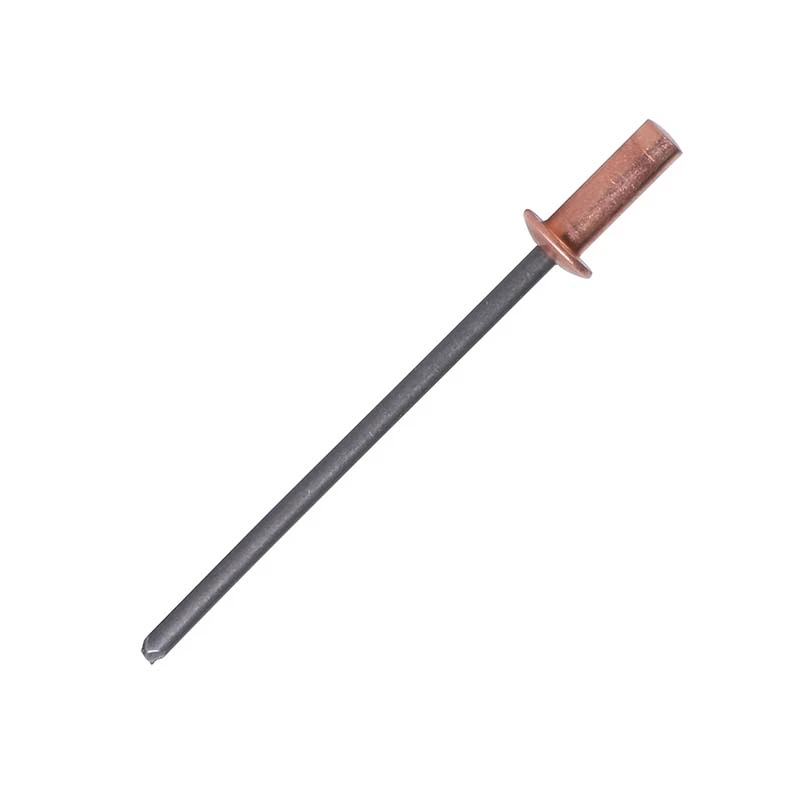
Applicable occasions: unilateral installation environment (such as pipe, box, shell)
Advantages:
- Easy to install, can be used for occasions that can not be operated from the back;
- Enclosed structure prevents liquid or gas leakage;
- No galvanic corrosion is induced with copper sheets.
Note: The rivet mandrel material should be copper or stainless steel to avoid corrosion caused by contact between steel mandrel and copper sheets.
4. Solid Round/Flat Head Copper Rivets
Applicable occasions: traditional copper art, ship restoration, handmade sheet metal
Advantages:
- Can be manually riveted to shape, easy to fine work;
- Compact structure, strong vintage appearance;
- Good conductive and decorative properties.
Do You Have Any Questions?
Let Us Solve Your Problem
Application of Riveting Copper Sheets
- Architectural and decorative works: copper roofing, copper wall cladding, rain gutters and downpour systems, copper cornice decoration, architectural inserts, heritage restoration (e.g. churches, bell towers, historic buildings).
- Craft & Light Manufacturing: copper lamps, decorative items, vintage style home products; artistic sculptures, copper nameplates, machinery casings; handmade bags/furniture with copper trim riveted; antique copper pots and pans with riveted carrying handles or rims.
- Electrical engineering field: copper rows / copper tape bracket fixed; grounded copper sheet structure connection; copper foil riveted fixed to the insulating substrate; high-frequency cables or shielding parts of the mechanical support.
- Special industries (ships, railways, instruments): copper steam piping support; instrumentation grounding copper sheet fixed; special alloy copper parts assembly.
3 Precautions When Riveting Copper Sheets
To ensure the reliability, long-term durability and appearance of the connection, special attention is paid to the following aspects when riveting copper sheets.
Ⅰ. Avoid galvanic corrosion
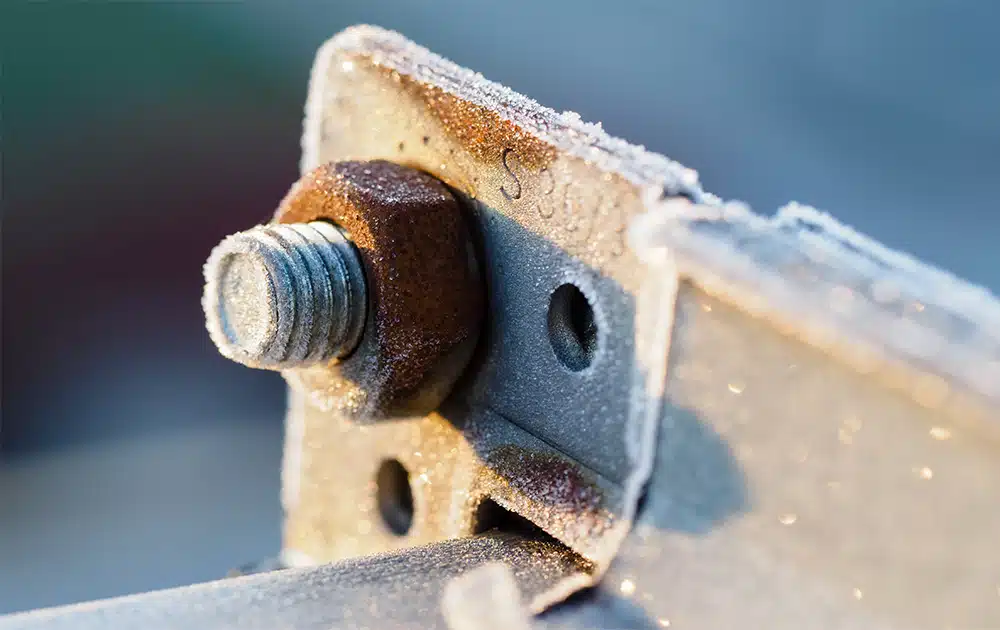
Galvanic coupling corrosion may form when copper material is in contact with other metals (e.g. aluminum, galvanized steel). This can directly affect the internal structure of the copper material, resulting in damage or even failure of the product.
But it is not insurmountable. When selecting blind rivets for your copper sheets, you need to pay special attention to the material of the blind rivets, e.g. choose copper or copper alloy rivets (e.g. brass). Of course it is also possible to insulate the riveted areas with neutral barrier coatings or nylon spacers. In addition to this, you need to avoid direct contact with galvanized parts, aluminum parts and other metals with large potential differences.
Ⅱ. Pre-treatment of copper plate surfaces
Before riveting copper sheets, the operator needs to ensure that the sheets are free of oxides, oil and burrs. As we all know, before using blind rivets, you need to drill holes in the copper sheets, the drilling position should be precise, to avoid redrilling or eccentricity; recommended use of high-speed steel or cobalt alloy drill, hole diameter slightly larger than the rivet diameter 0.1-0.2mm.
Ⅲ. Structure and load direction planning
Copper high ductility, low strength, in order to meet the strength requirements of riveting, riveting point spacing and number of reasonable arrangements.
When installing blind rivets, it is necessary to avoid over-concentration of rivets or too close to the edge, as this can lead to tearing or arching of the sheet. On soft copper sheets, reinforcing shims can be used to disperse localized stresses.
Do You Have Any Questions?
Let Us Solve Your Problem
Is Copper Riveting Superior to Soldering or Brazing?
Criteria | Riveting | Welding | Brazing |
Heat Impact | Cold process, no heat-affected zone | High heat input, causes metal melting and discoloration | Medium heat (450–800°C), lower than welding |
Sealing Performance | Not inherently sealed; may require sealant | Seam is continuous, good sealing | Generally good sealing, suitable for gas/liquid-tight joints |
Strength | Mechanical lock, moderate strength | Fusion bond, high strength | Medium strength, suitable for light load joints |
Surface Integrity | Preserves original finish, minimal distortion | Can discolor or deform copper surface | Minimal surface impact if well controlled |
Aesthetic Appearance | Decorative rivet patterns possible | Welds may require grinding to look clean | Smooth, uniform finish if done correctly |
Corrosion Risk | Low if materials are matched properly | Weld zone may have reduced corrosion resistance | Depends on filler material compatibility |
Material Thickness Suitability | Ideal for 0.4–3mm thick copper | Best for ≥1mm; thin sheets risk burn-through | Best for 0.2–2mm copper sheets |
When is riveting copper sheets preferred?
- Heat-sensitive applications: e.g. plasticized or coated copper, or where the original copper surface texture is to be retained;
- Outdoor/construction sites: no power or air supply is required, flexible operation, and low exposure to the elements;
- Decorative connections: e.g. copper ornaments, architectural façades, lamps, restoration of ancient buildings;
- Copper plate thickness ≤ 2mm, and double-sided or single-sided can be operated can be applied.
Custom Riveting Solutions for Your Copper Sheets Projects
Are you looking for reliable rivet manufacturers and suppliers for your copper sheets project? A qualified and consistent quality blind rivet is very important for your copper sheets project.
Rivmate is a leading rivet manufacturer in China, offering a full range of high quality rivets.
Get Rivets Quote
You may also find these topics interesting
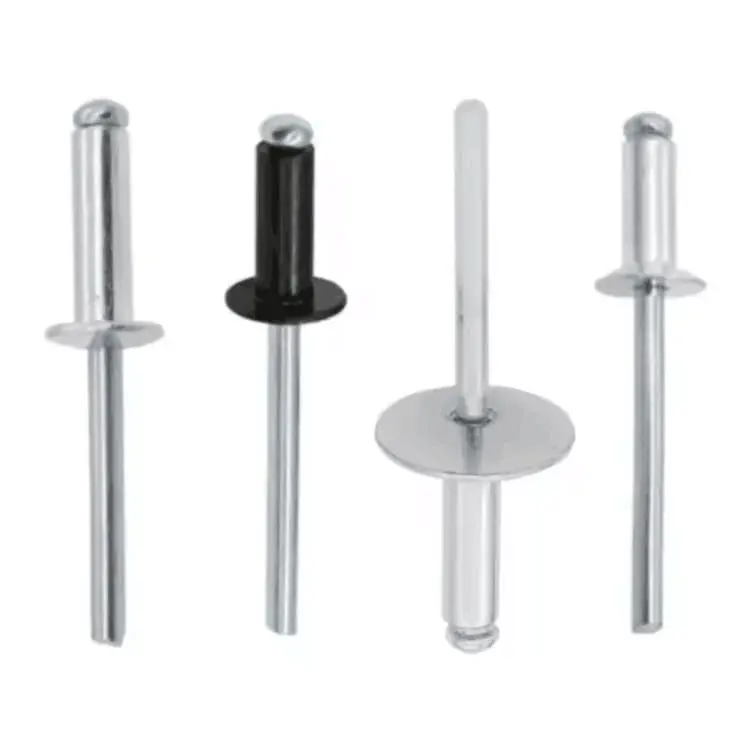
Buy Open Type Blind Rivets
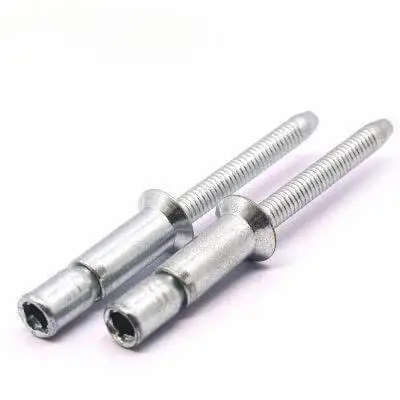
Buy Structural Blind Rivets
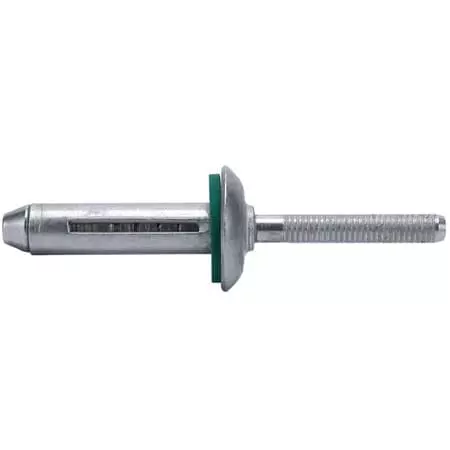