Table of Contents
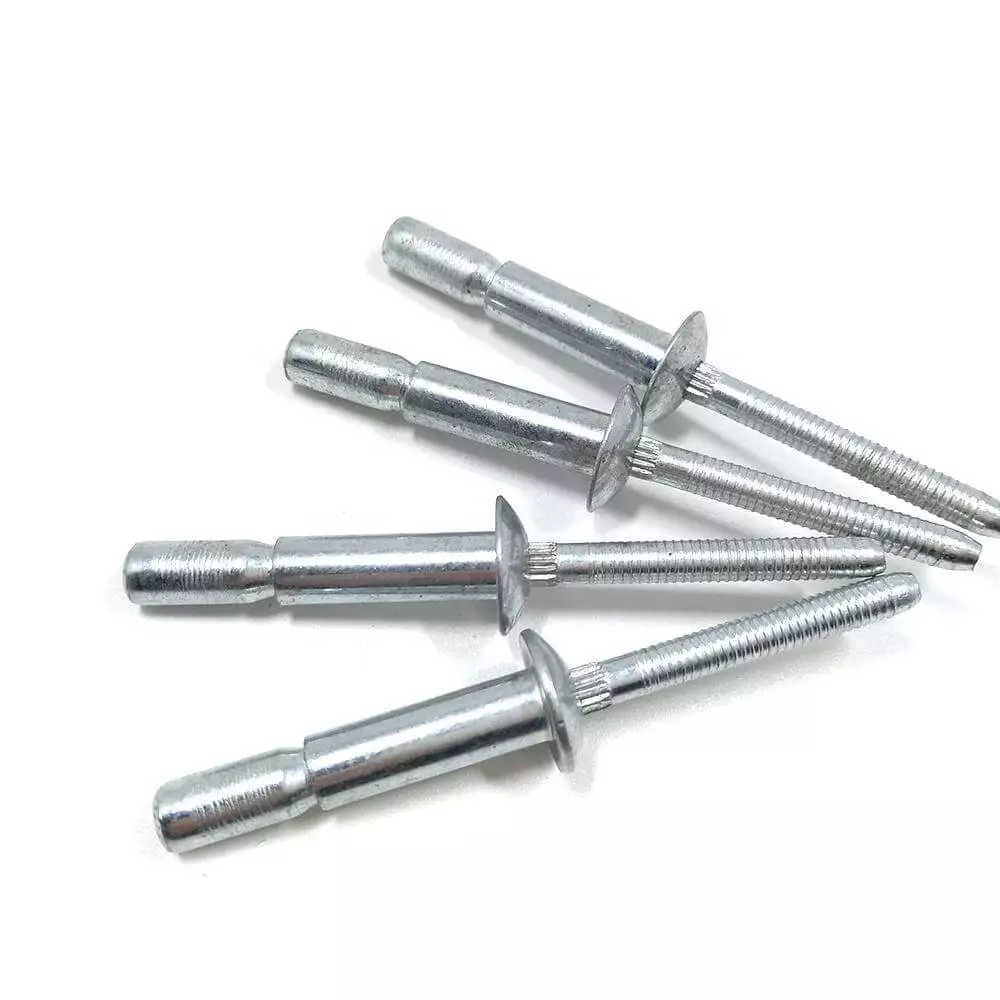
This article explains stainless steel vs aluminum pop rivets in detail. Including the definition of stainless steel pop rivets and aluminum pop rivets, material composition, applications, benefits, and differences between them. If you want to know how to choose the right rivets for your project, this article can also help you.
Table of Contents
What Are Stainless Steel Pop Rivets?
Stainless steel pop rivets are a type of blind rivets made of stainless steel material. Stainless steel pop rivets can provide higher strength and longer service life than regular pop rivets. And stainless steel pop rivets have excellent corrosion resistance and longer service life.

Stainless steel pop rivets play an important role in applications that require high strength and corrosion resistance, such as construction, automotive, marine, aerospace and heavy industry.
Types of Stainless Steel Pop Rivets
Blind Rivet generally consists of two parts: 1. rivet body 2. rivet mandrel. in order to achieve better riveting effect, generally these two parts of the manufacturing material is different. The following are the material combinations of stainless steel blind rivets:
- 304&316 stainless steel mandrel / 304&316 stainless steel body
- stainless steel mandrel / aluminum body
- 420 stainless steel mandrel / 304 stainless steel body
Characteristics of Stainless Steel Pop Rivets

- Durable: Even when used for a long time in harsh environments (such as oceans, chemical plants, high humidity areas), stainless steel blind rivets will not rust or corrode.
- Good compatibility: Stainless steel blind rivets can be used in steel, stainless steel, aluminum, plastics, composite materials and other substrates connection.
- Stable connection: Blind rivets will form a permanent fixing after riveting is completed, with high resistance to vibration, suitable for dynamic loading conditions.
- Aesthetics: Stainless steel blind rivets have a very smooth surface after riveting. Because the stainless steel material has a metallic texture, aesthetically pleasing.
What are Stainless Steel Rivets Used for?
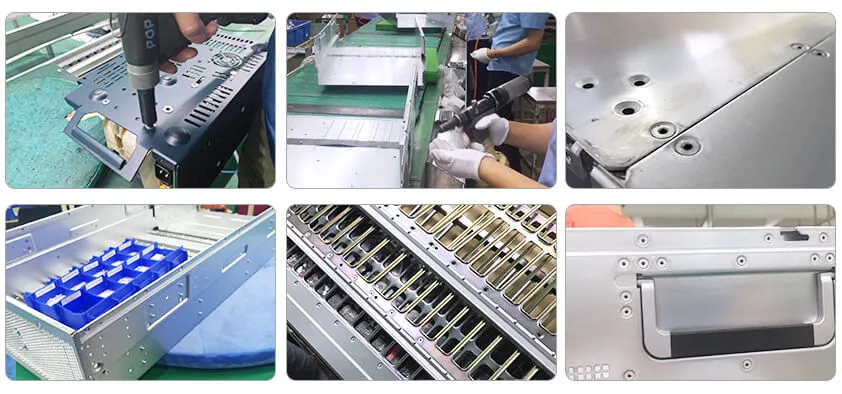
- Construction and infrastructure: fixed curtain walls, door and window frames, decorative panels.
- Ship and marine engineering: installing cabins, deck equipment, protective covers.
- Automotive and transportation equipment: fixing body panels, chassis, door hinges.
- Aerospace: cabin panels, bracket assembly connections.
- Household appliances: washing machine, refrigerator shell, internal bracket fixing.
- Industrial equipment: metal frame, bracket mounting.
Will Stainless Steel Rivets Rust?
Under the vast majority of conditions of use, stainless steel blind rivets will not rust. The corrosion resistance of Stainless Steel Blind Rivets is excellent for most environments.
So why stainless steel blind rivets will not rust?
Because the corrosion resistance of stainless steel is mainly due to its chromium content (usually ≥ 10.5%), chromium and oxygen in the air will be combined to form a dense passivation layer on the surface, which can effectively prevent oxidation and corrosion.

As we mentioned above, stainless steel blind rivets will not rust under normal conditions of use. So what are the circumstances in which stainless steel blind rivets may occur rust?
- Surface damage
- Chloride attack in the environment: In environments with high salt content (e.g. seashore, salt spray environments) or when exposed to chemicals (e.g. chloride solutions), the passivation layer may be damaged by chloride ions.
- Electrochemical corrosion: When stainless steel rivets are in contact with other metals (e.g. carbon steel), electrochemical corrosion is formed in humid environments.
- Surface contamination: construction or transportation process, the surface is contaminated with iron filings, dust or other pollutants, may induce corrosion.
- Use of poor quality stainless steel materials
What Are Aluminum Pop Rivets?
Aluminum blind rivets are a type of blind rivets made of aluminum alloy. Blind Rivets made of this material are designed for joining lightweight materials. Aluminum blind rivets are used a lot in applications that require lightweighting.
Types of Aluminum Pop Rivets
The following are combinations of common aluminum blind rivets:
- Carbon Steel Mandrel / Aluminum Body
- Aluminum Mandrel / Aluminum Body
- 304 & 316 Stainless Steel Mandrel / Aluminum Body
Prons of Aluminum Pop Rivets
- Lightweight: Aluminum is lightweight and suitable for application scenarios where overall weight is a requirement. For example, aluminum blind rivets are often used in automotive manufacturing.
- Strong corrosion resistance: Aluminum has good resistance to oxidation and moisture, suitable for outdoor or humid environments.
- Good thermal and electrical conductivity: Aluminum can be both mechanically connected and electrically conductive in specific application scenarios.
Applications of Aluminum Pop Rivets
Because aluminum blind rivets have many characteristics that blind rivets made of other materials do not have, aluminum blind rivets are also very widely used. The following are common application scenarios for aluminum blind rivets:
- Aerospace: for the assembly of lightweight aluminum alloy body parts.
- Automotive industry: used in thin sheet metal connections such as automotive doors, fenders and roof frames.
- Construction: used in the fixing of curtain walls, decorative panels and aluminum doors and windows.
- Electronic equipment: suitable for the assembly of light equipment housings and internal components.
- Household & Furniture: used in aluminum-framed furniture, decorative parts and household equipment assembly.
- Industrial equipment: used in the attachment of metal enclosures, equipment supports and pipe support structures.
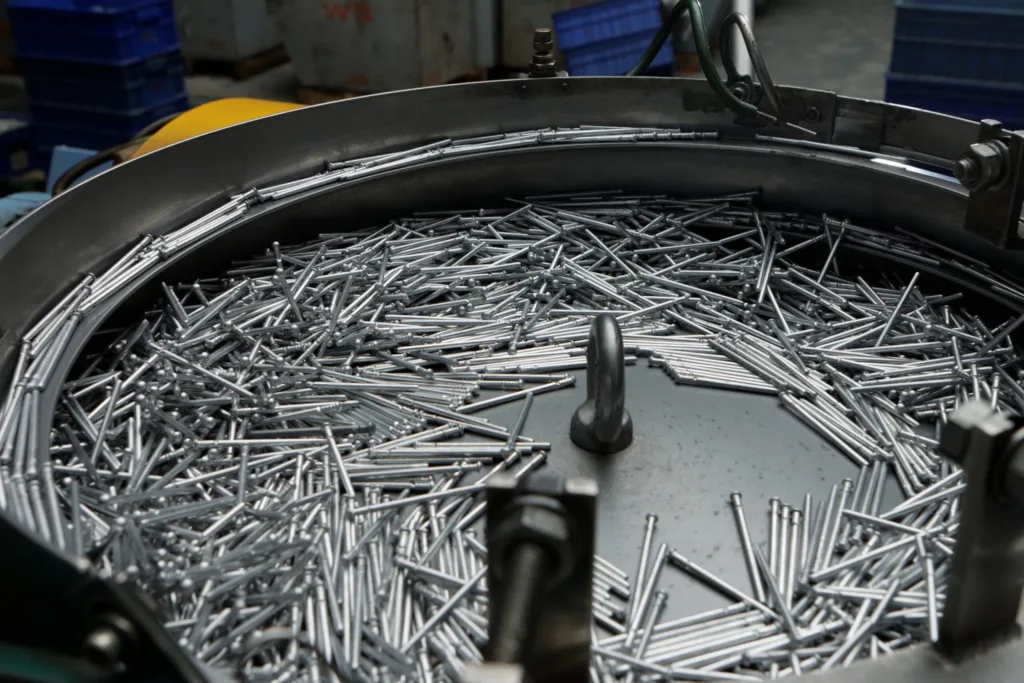
Contact Our Engineers Today
We provide you with high quality rivets, including customized services.
Stainless Steel vs Aluminum Pop Rivets: Differences of Them
Comparison Item | Stainless Steel Blind Rivets | Aluminum Blind Rivets |
Strength | High strength, excellent tensile and shear resistance, suitable for high-load applications. | Lower strength, suitable for light to medium loads. |
Weight | Heavier due to higher density. | Lightweight, ideal for weight-sensitive applications like aviation. |
Corrosion Resistance | Excellent corrosion resistance, especially 316 stainless steel, suitable for marine and chemical environments. | Good corrosion resistance but less effective in saline or chemical environments compared to stainless steel. |
High-Temperature Resistance | Retains performance in high-temperature environments, suitable for extreme conditions. | Poor high-temperature resistance; strength decreases significantly at elevated temperatures. |
Durability | Long-lasting, ideal for harsh environments and high-vibration applications. | Shorter lifespan, suitable for general environments and non-critical structures. |
Ease of Installation | Harder material requires higher pulling force tools, making installation more challenging. | Softer material, easier and quicker to install with lower pulling force tools. |
Aesthetic Appeal | Smooth and polished surface, resistant to wear and corrosion, maintains good appearance over time. | Attractive but prone to scratches or discoloration due to oxidation. |
Cost | Higher cost, suitable for demanding applications requiring superior performance. | More economical, cost-effective for mass usage. |
Galvanic Corrosion | Risk of galvanic corrosion when in contact with dissimilar metals; requires isolation. | Lower galvanic corrosion risk, better compatibility with aluminum substrates. |
Electrical Conductivity | Moderate conductivity, requires additional treatment for electrical applications. | Good electrical conductivity, suitable for electrical connections. |
Applications | High-strength and harsh environments: marine, chemical equipment, automotive, industrial machinery, fireproof doors, etc. | Lightweight and general environments: aviation, appliances, furniture, aluminum structures, decorative fixtures, etc. |
Stainless steel blind rivets:
- Advantages: high strength, corrosion resistance, high temperature resistance, long life, suitable for harsh environments and high strength demand scenarios.
- Disadvantages: heavier weight, higher price, installation difficulties.
Aluminum blind rivets:
- Advantages: light weight, low price, easy to install, suitable for lightweight demand and ordinary environment.
- Disadvantages: strength and corrosion resistance than stainless steel, relatively short service life.
What's Stronger, Stainless Steel or Aluminum?
Obviously, stainless steel blind rivets are much stronger than aluminum blind rivets. This is because stainless steel is much stronger and harder than aluminum.
How to Choose Stainless Steel Pop Rivets or Aluminum Pop Rivets?
It is likely that many business owners do not know how to choose the best Blind Rivet for their business. They have questions about whether to choose stainless steel blind rivets or aluminum blind rivets. Next I will explain this question by looking at some of the most commonly considered aspects!
1. Strength Requirements According to Application Scenarios
- High strength requirements (e.g. carrying heavy loads, withstanding high Ferrari or shear forces) : stainless steel blind rivets are recommended. Because the strength of stainless steel blind rivets is relatively high, ideal for high loads and critical parts of the connection.
- Medium and low strength requirements (such as light structural connections) : aluminum blind rivets with moderate strength, suitable for light applications, economical and practical.

2. Depending on the Corrosive Environment
Stainless steel blind rivets are highly resistant to corrosion, especially 316 stainless steel. If your project is in a corrosive environment such as wet, chemical, salt spray or marine, stainless steel blind rivets are the best choice.
While aluminum blind rivets have better oxidation resistance and are suitable for general indoor environments or low corrosive occasions.
3. Depending on Weight Requirements
Aluminum blind rivets are lightweight and can effectively reduce the overall weight of a structure. Stainless steel blind rivets, on the other hand, are heavier but provide greater strength and stability.
4. Depending on Temperature Requirements
If your project is in a high-temperature environment, such as near an engine or high-temperature industrial equipment, then you should choose stainless steel blind rivets with excellent high-temperature resistance.
If your usage scenario is in a constant or low-temperature environment, aluminum blind rivets will be sufficient to meet the requirements.
5. Based on Budget
Aluminum blind rivets are relatively inexpensive and suitable for high volume use. If your project budget is limited, then aluminum blind rivets may be more suitable.
Stainless steel blind rivets are more expensive, although they have better strength and corrosion resistance.
If you want to learn more about rivet cost, read this article “how much do rivets cost ”.
6. Depending on the Application Scenario
- Ships, chemical equipment, bridges, outdoor facilities : Stainless steel blind rivets
- Aerospace, lightweight equipment, household appliances : Aluminum blind rivets
- Automobile bodies, industrial equipment, mechanical fixtures : Stainless steel blind rivets
- Doors and windows, lightweight frames, decorative connections : Aluminum blind rivets
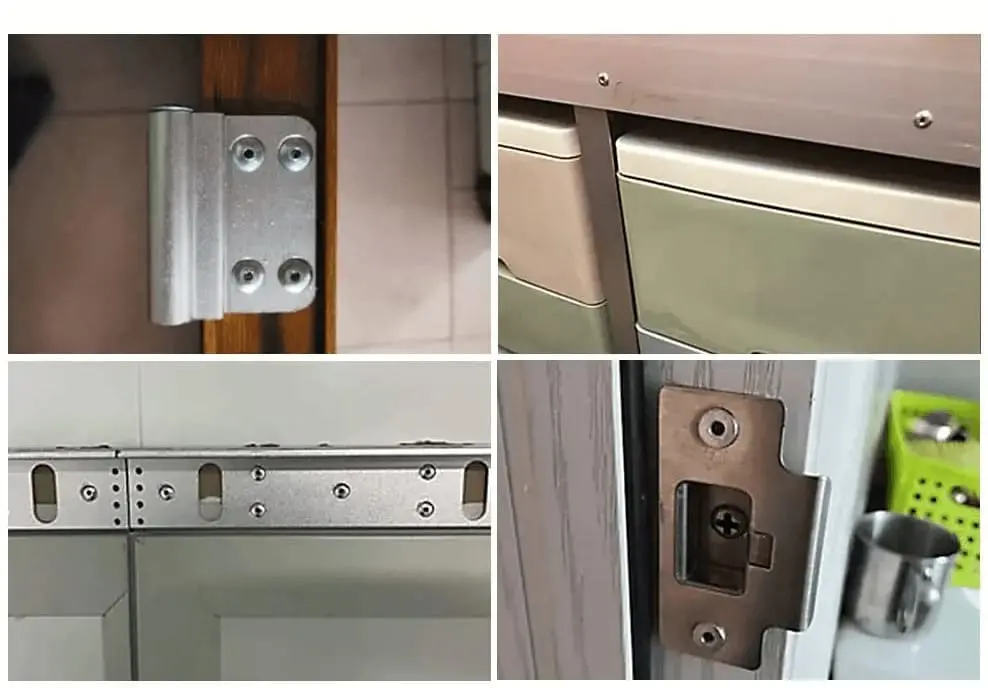
Rivmate Rivet - Enhance Your Business
Stainless steel vs aluminum pop rivets is a concern for many people. Through this article, I am sure you have a clear understanding of the difference between stainless steel pop rivets and aluminum pop rivets and how to choose. Get a sample of rivets now.
If you want to buy the right rivets in bulk for your project, contact us!
Contact Person Search
Submit Your Sourcing Request
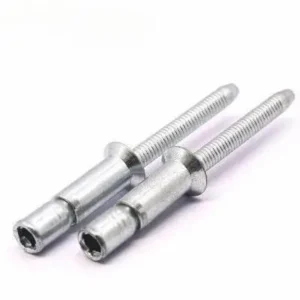
What is the Difference Between Countersunk Rivets and Regular Rivets? – Rivmate Expert Guide
What is the Difference Be
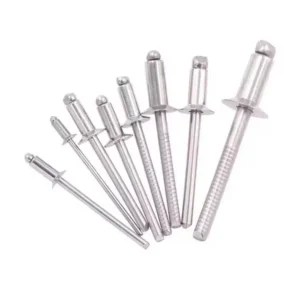
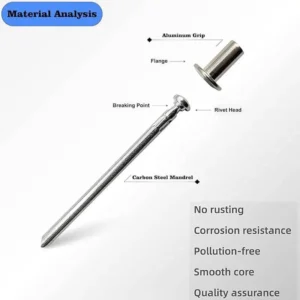