Table of Contents
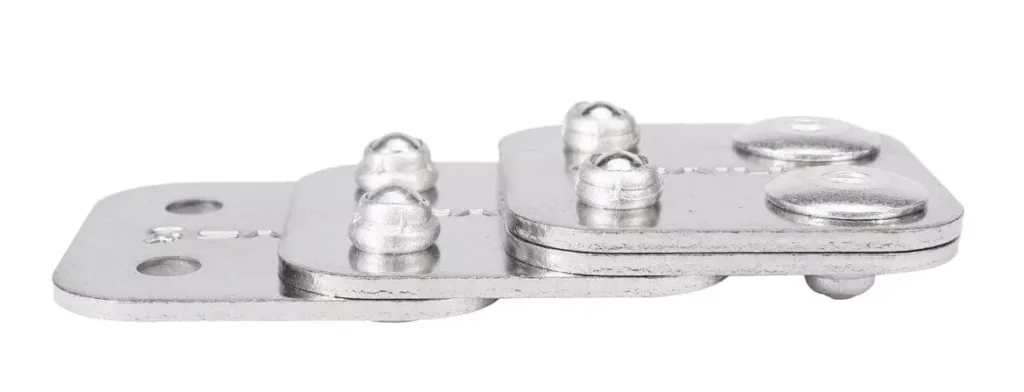
Blind rivet clamping force can directly affect the riveting effect of the blind rivets. So do you know what is the Blind Rivet Clamping Force? What factors affect it.
With this ultimate guide, you will learn everything essential about rivet clamping force.
Table of Contents
Blind Pop Rivet Clamping Force - Basic Definition
Blind Rivet Clamping Force is the constant pressure exerted on the joining material by the expanding deformation of the blind rivet’s tail after installation. This pressure ensures that the material is held tightly in place and is a central source of strength for riveted structures to resist external forces and maintain long-term stability.
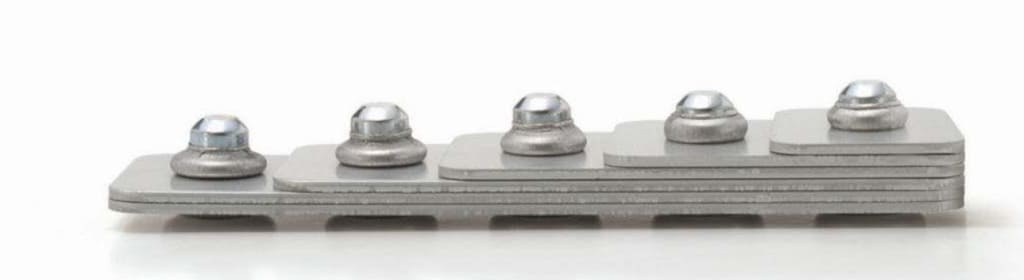
Importance of Blind Rivet Clamping Force
- Ensures a solid connection: Eliminates gaps and prevents loosening due to vibration or load variations by compacting the material contact surfaces.
- Resist separation and deformation: the clamping force acts perpendicularly to the material surface, directly opposing the tensile forces (e.g. stretching, bending) that try to separate the material.
- Enhance sealing performance: In applications where leakage prevention is required (e.g. pipes, housings), sufficient clamping force reduces the gap between materials and enhances the sealing effect.
- Adapt to dynamic environments: In scenarios with high vibration, shock or temperature fluctuations (e.g., automotive, aircraft structures), the clamping force maintains a durable and reliable connection.
- Simplified assembly process: Unilateral mounting creates equalized pressure, making it suitable for tight spaces where double-sided operation is not possible, while ensuring consistent strength.
How to Measure Blind Rivet Clamping Force?
We all know that clamping force is a very important factor for blind rivets. So do you know how to measure the blind rivet clamping force?
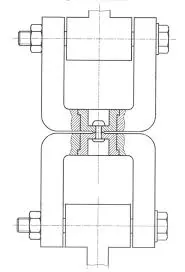
If you want to accurately test blind rivet clamping force, then you need to use a professional laboratory. In the lab, you need to use a tensile testing machine to record the maximum load by applying reverse pressure until the component separates.
- Fix the riveted specimen on the tension machine.
- Slowly apply a tensile force perpendicular to the connection surface and monitor the change in force value.
- The peak force when the rivet fails (pulls out or breaks) is the limit value of the clamping force.
The actual clamping force needs to be combined with the deformation characteristics of the material, usually taking 70-90% of the peak force as a reference value.
Do You Have Any Questions?
Let Us Solve Your Problem
How Does Clamping Force Affect the Blind Rivet Strength?
Blind rivet clamping force directly affects the overall strength and load capacity of the rivet. The following is a detailed analysis:
1. Ability to resist tensile loads
Clamping force through the expansion of the tail of the rivet deformation, the material to be connected to the rivet head and tail between the “blind end” to form a friction resistance to material separation. The greater the clamping force, the stronger the friction between the materials, the greater the tensile strength of the rivet.
2. Resistance to shear loads
High clamping force → material fit tightly → shear force distribution is more uniform, reducing local stress concentration.
3. Stability in dynamic loading and vibration environments
Qualified clamping force provides dynamic load capacity of the rivet.
- Vibration Attenuation: The continuous pressure provided by the clamping force counteracts the relative material displacement caused by cyclic loading.
- Self-locking effect: Similar to bolt preload, clamping force inhibits initial loosening induced by vibration (e.g., automotive chassis, aircraft skins).
- Fatigue Life Improvement: Clamping forces reduce alternating stress amplitudes and delay fatigue crack initiation by eliminating gaps.
4. Synergies under multiple composite loads
In composite stress scenarios (e.g. tensile + shear, bending + torsion):
- Clamping force maintains a rigid material fit and avoids localized stress superposition.
- At frame joints, high clamping forces prevent the accumulation of structural deformation due to multi-directional loads.
How to Optimize Blind Rivet Clamping Force for Different Applications?
Clamping force requirements vary from application to application. For soft materials, if the clamping force is too high, it can easily lead to material damage. The rivet clamping force for structural rivets is much higher than that of standard rivets.
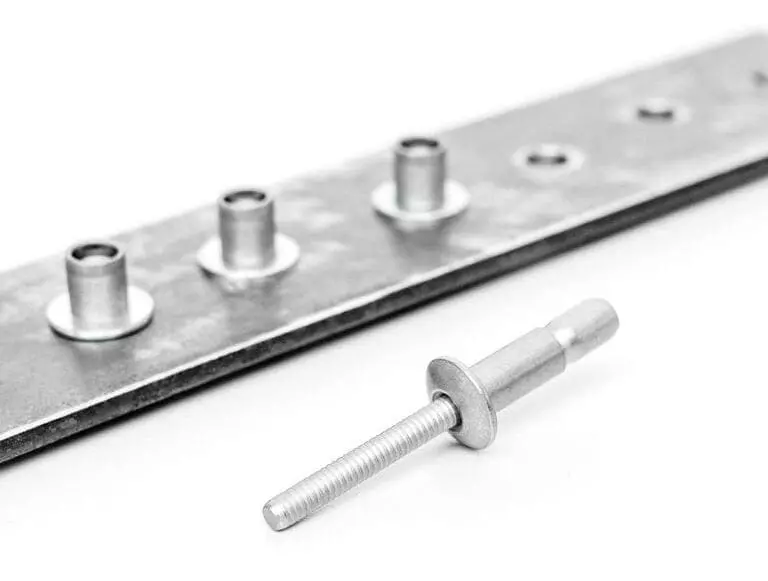
Clamping force optimized for the type of load
Load Type | Optimization Focus | Recommended Rivet Type | Parameter Adjustments |
Static Tensile Load | Maximize clamping force to prevent separation; prioritize tensile strength. | Structural blind rivets (e.g., Rivmate Monobolt Rivet) | Increase diameter (≥5mm), stainless steel material. |
Dynamic Vibration | Prevent loosening; enhance fatigue resistance. | Self-locking rivets (e.g., Avdel® LOK Series) | Multi-lobe tail design; low-friction mandrel coating. |
Shear Load | Enhance shank strength. | Blind lockbolts (high-shear materials) | Thicker shank; mandrel strength matching. |
Composite Load | Balance tensile and shear performance. | Closed-end stainless steel rivets | Double-lock structure; uniform tail expansion. |
Optimization of the clamping force according to the material to be joined
- Soft Substrates (Plastics, Aluminum): When riveting soft materials, rivets tend to crush and lose clamping force. Therefore, you can choose aluminum or mild steel soft rivets to reduce the expansion pressure. Or increase the rivet gasket area to disperse the pressure (such as flat head rivets).
- Hard substrates (steel, composite materials): riveting hard materials, it is easy to occur when the local stress concentration. So you can use high-strength rivets (stainless steel / titanium alloy) and pre-drilled holes to reduce resistance.
- Multi-layer dissimilar materials: If inter-layer sliding occurs, pre-compact the inter-layer gap (pressure fixture-assisted installation).
Do You Have Any Questions?
Let Us Solve Your Problem
Can Excessive Clamping Force Cause Rivet Breakage or Material Deformation?
Yes, excessive blind rivet clamping force can lead to problems such as rivet breakage, material crushing and deformation, and even connection failure.The issues that may arise are listed below:
- Premature breakage of the mandrel
- Neck shear failure
- Rivet head damage
- Soft material dents
- Stress concentration
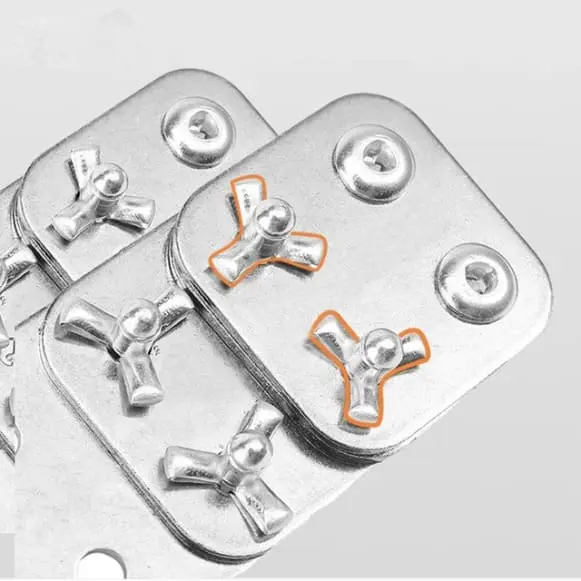
Causes of excessive clamping force
Factor | Impact |
Excessive Tool Force | High-pressure rivet guns or incorrect settings can over-expand the rivet, leading to deformation or fracturing. |
Mismatched Rivet-Material Hardness | Hard rivets (e.g., stainless steel) on soft substrates (e.g., plastic) cause crushing. |
Process Errors | Uncalibrated tools, repeated pulling, or improper installation speed. |
Environmental Factors | High temperatures may unexpectedly increase clamping force post-installation. |
Custom Riveting Solutions for Your Project
Are you wondering how to use give breakout rivets for your project? If this guide doesn’t solve your problem, contact one of our engineers.
Rivmate is a top rivet manufacturer in China. We will provide you with high quality rivet products and affordable price.
Get Rivets Quote
You may also find these topics interesting
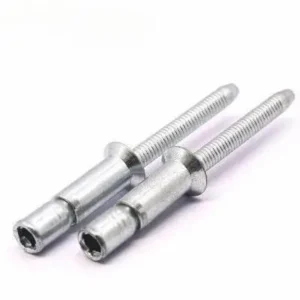
What is the Difference Between Countersunk Rivets and Regular Rivets? – Rivmate Expert Guide
What is the Difference Be