The Ultimate Guide to Different Rivet Material Properties
Table of Contents
Different rivet material properties create different riveting effects. It is vital to choose the right rivet material for the situation.
This blog will be centered around rivet materials properties to introduce you to the differences and applications of different rivet materials.
importance of understanding rivet material properties
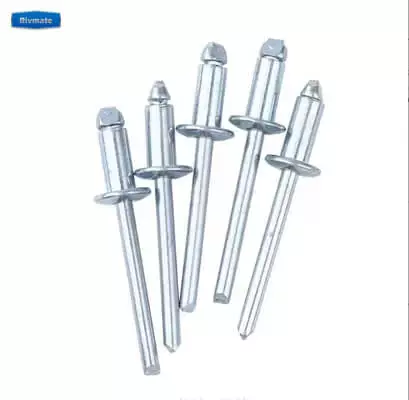
In industrial manufacturing and structural connections, the performance of rivet materials is one of the core factors in determining their service life, connection strength, corrosion resistance and safety and stability. Different rivet materials types not only have significant differences in physical and mechanical properties, but also have a direct impact on their suitability and long-term performance in specific environments.
Why understand the material properties of rivets?
1. Material Determines Connection Strength
The tensile, shear, and expansion grip of a rivet is directly dependent on the strength rating and hardness of the material itself. For example, carbon steel rivets are suitable for heavy-duty structures, stainless steel is suitable for high-vibration scenarios, while aluminum is more suitable for lightweight, flexible connections.
2. Anti-corrosion ability is determined by the material
In outdoor, high humidity, seashore or acid rain environments, the anti-corrosion ability of the material is the guarantee of stable system operation. Improper use of the material may appear in a short period of time corrosion, or even cause galvanic corrosion, damage to the connection substrate. 3.
3. Rivet compatibility is affected by the material
The coefficient of thermal expansion and flexibility of rivets made of different materials are matched differently to the main material. Improper selection may lead to unstable clamping force, riveting inaccuracy, slippage or tearing phenomenon, affecting the reliability of the structure.
4. Cost and engineering suitability need to be weighed
Materials such as aluminum, stainless steel, carbon steel, copper, and alloys vary in price, processability, and supply stability. Understanding performance helps projects make better cost-effective purchasing decisions while meeting functional requirements.
There is a wide range of materials used for rivets in industrial and structural joining applications. There are differences in strength, corrosion resistance, weight and fitment characteristics between the different materials. They are suitable for different environments and engineering needs. The following are common types of rivet materials:
- Aluminum: lightweight, good corrosion resistance, good thermal conductivity, easy processing
- Stainless Steel: high strength, corrosion resistance, high temperature resistance, long life.
- Carbon Steel: high strength, good toughness, low price.
- Copper: good electrical conductivity, ductility, fatigue resistance, excellent
- Monel: super corrosion resistance, acid and alkali resistance, high temperature resistance.
- Nylon / Plastic: good insulation, anti-corrosion, non-conductive, lightweight and non-magnetic
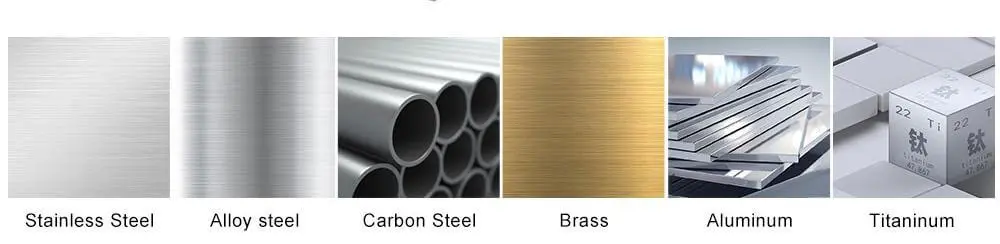
Key indicators of rivet material Properties
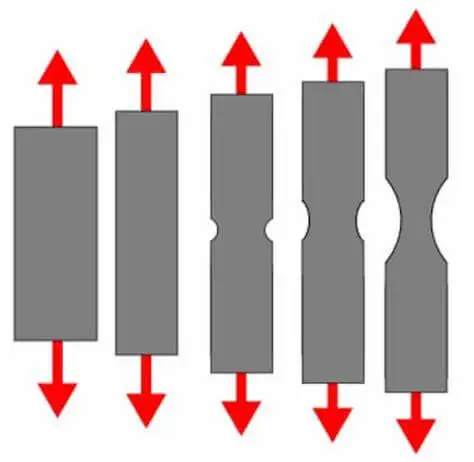
Refers to the maximum stress that the rivet can withstand in the direction of axial tension (unit: MPa or kN). This property determines whether or not the rivet will be pulled off when pulled under force. As
Reference values for different materials:
- Aluminum: 150-250 MPa
- Stainless steel: 450-700 MPa
- Carbon steel: 400-600 MPa
The lateral load carrying capacity of a rivet measures its resistance to damage in the direction of sheet slip. This property is the core indicator of structural rivet connections. The shear resistance of common materials is as follows:
Stainless steel and carbon steel is better than aluminum, copper and other soft materials.
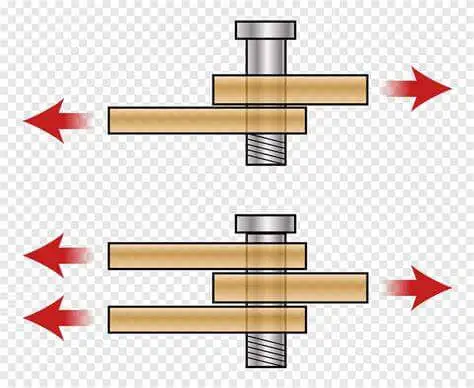
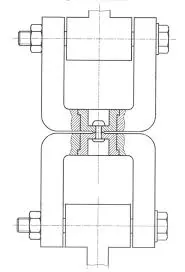
This refers to the clamping or locking force exerted on the connecting plates by the expansion of the rivet. This strength property directly affects whether or not the structure is secure and whether or not displacement or loosening occurs.
In general, the harder the material, the stronger the grip is usually. However, care needs to be taken to avoid pressing through the sheet.
4. Rivet Corrosion Resistance
This characteristic is a measure of a material’s ability to resist oxidation, rust, and chemical reactions in different environments.
Aluminum has a natural oxidized protective film. Stainless steel (304/316) is suitable for hot and humid environments with salt spray; carbon steel requires surface protection.
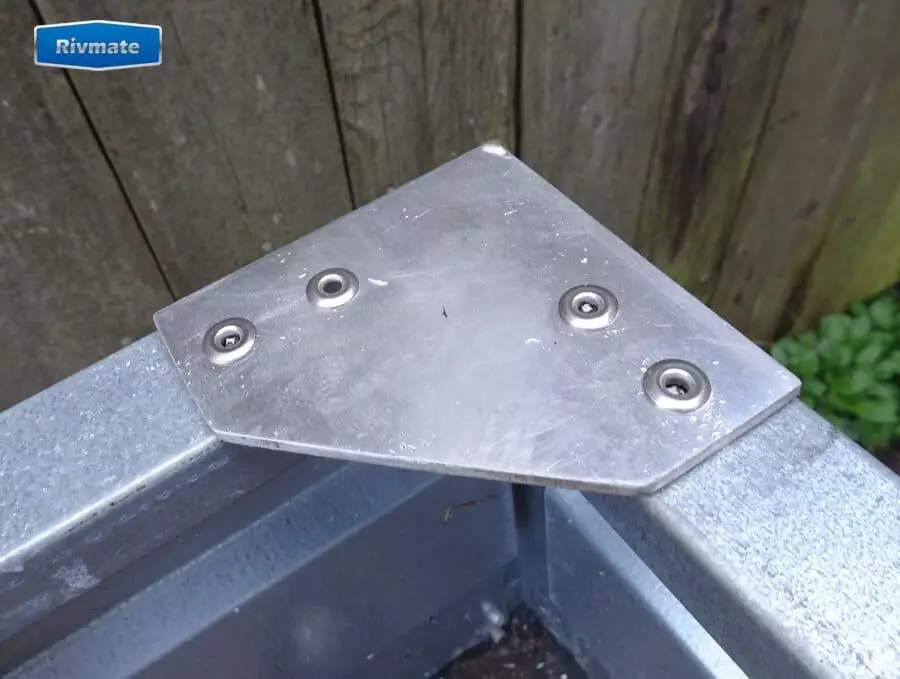
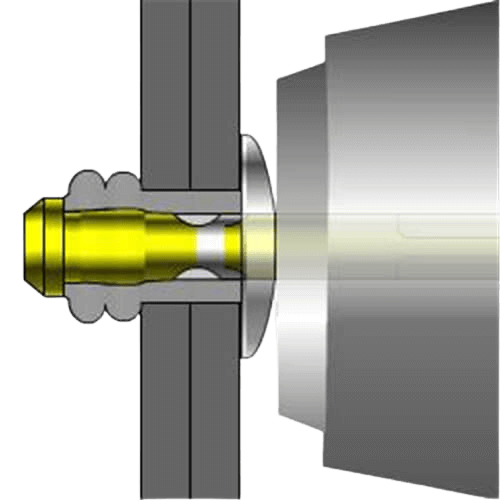
This property is the rate of dimensional change of the rivet material under temperature change. Will directly
affect the thermal suitability of rivets and the main material.
Such as aluminum to aluminum connection, need to avoid thermal stress concentration. And aluminum to steel structure is prone to thermal expansion and contraction differences caused by stress fatigue.
6. Rivet Hardness
Rivet hardness is a measure of a material’s ability to resist press-in and deformation. It is related to the resistance to extrusion and durability after riveting.
- Commonly used Rockwell hardness (HRC) or Brinell hardness (HB) that
- If the hardness is too low, it is easy to deform; if it is too high, it is difficult to process and easy to damage the main material.
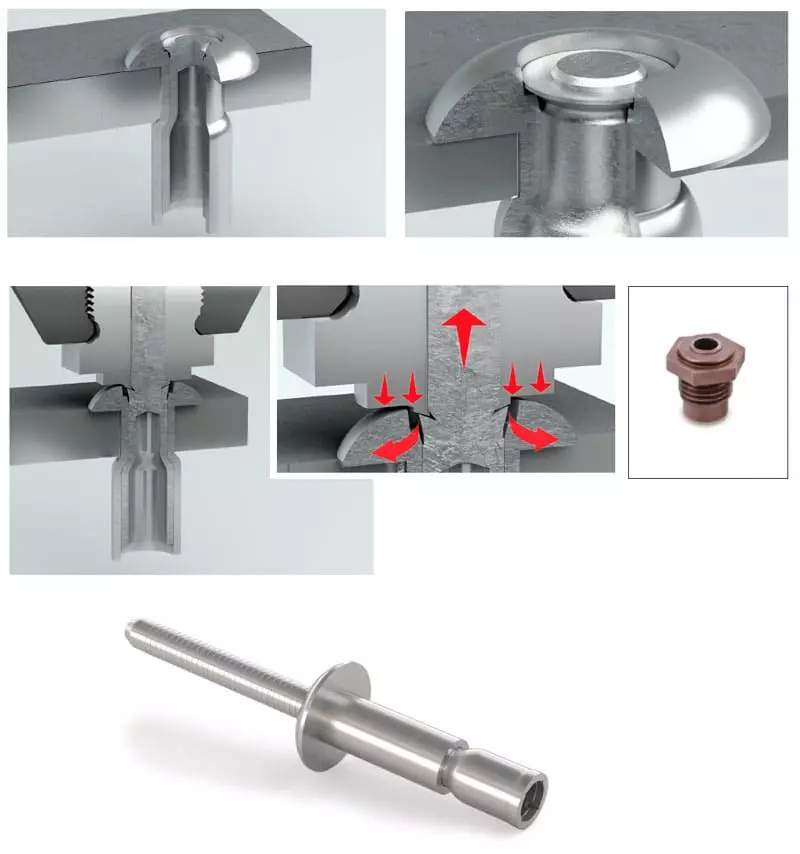
Understanding the above key performance indicators helps to more scientifically select rivet materials that match the application environment, structural requirements and cost expectations. It is the fundamental engineering knowledge for building stable, high-performance connection systems.
Characteristics of different rivet material properties
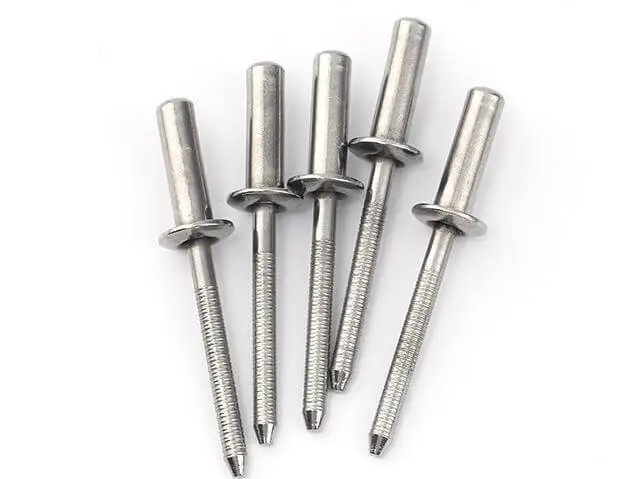
Aluminum is one of the most widely used rivet materials today. This is primarily due to its light weight, ease of processing, moderate cost and natural corrosion resistance. Aluminum naturally forms a protective oxide film in the air, which helps to resist rain and oxidation, and is therefore used in photovoltaic mounting systems, aerospace structures, lightweight automotive parts, and electronic equipment assemblies.
The greatest advantage of aluminum rivets is their good adaptation to thermal expansion. When used in aluminum profile systems, they can avoid loosening of the connection due to thermal expansion and contraction. However, their low mechanical strength makes them unsuitable for use in primary structural connections or load-bearing areas. Therefore there is a risk of fatigue cracking in high vibration or shock environments. In addition, pitting of aluminum may still occur in salt spray environments, and it is recommended that coated or higher protection grade materials be used instead in coastal or industrial areas.
Stainless Steel rivets excel in extreme environments due to their outstanding mechanical strength and corrosion resistance.
The 304 and 316 series stainless steels remain stable over long periods of time under conditions of heat and humidity, salt spray, acids and alkalis, or atmospheric corrosion, and are often used in structures such as marine equipment, power facilities, bridge supports, and industrial machinery housings. Therefore, they are commonly used in marine equipment, power facilities, bridge supports, industrial machinery housing and other structures. In addition, stainless steel rivets also has a very high resistance to shear and tensile capacity, suitable for the main load-bearing connection or long-term maintenance-free work system.
In addition, austenitic stainless steel has non-magnetic properties, to meet the sensitive to electromagnetic interference applications. However, its shortcomings are also obvious: high cost, processing hardness, the installation of high-power riveting equipment, otherwise prone to arbor fracture incomplete or riveted inaccurate. It also has a higher deadweight than aluminum, making it unsuitable for lightweight projects. Due to its electrochemical properties, it is not recommended to mix with aluminum alloy for a long time to avoid galvanic coupling corrosion.
Carbon Steel is a cost-effective material for structural connections. With its good strength and toughness, it is widely used in heavy manufacturing, bracket installation, machining and other fields.
Carbon Steel rivets are stronger than aluminum and are easier to machine and form, making them suitable for mass production and automated assembly, making them one of the main materials commonly used for structural rivets. Through electro-galvanizing, Dacromet or zinc-aluminum coating and other surface treatment, its corrosion resistance can be significantly improved, but its nature still does not have the corrosion resistance of stainless steel level.
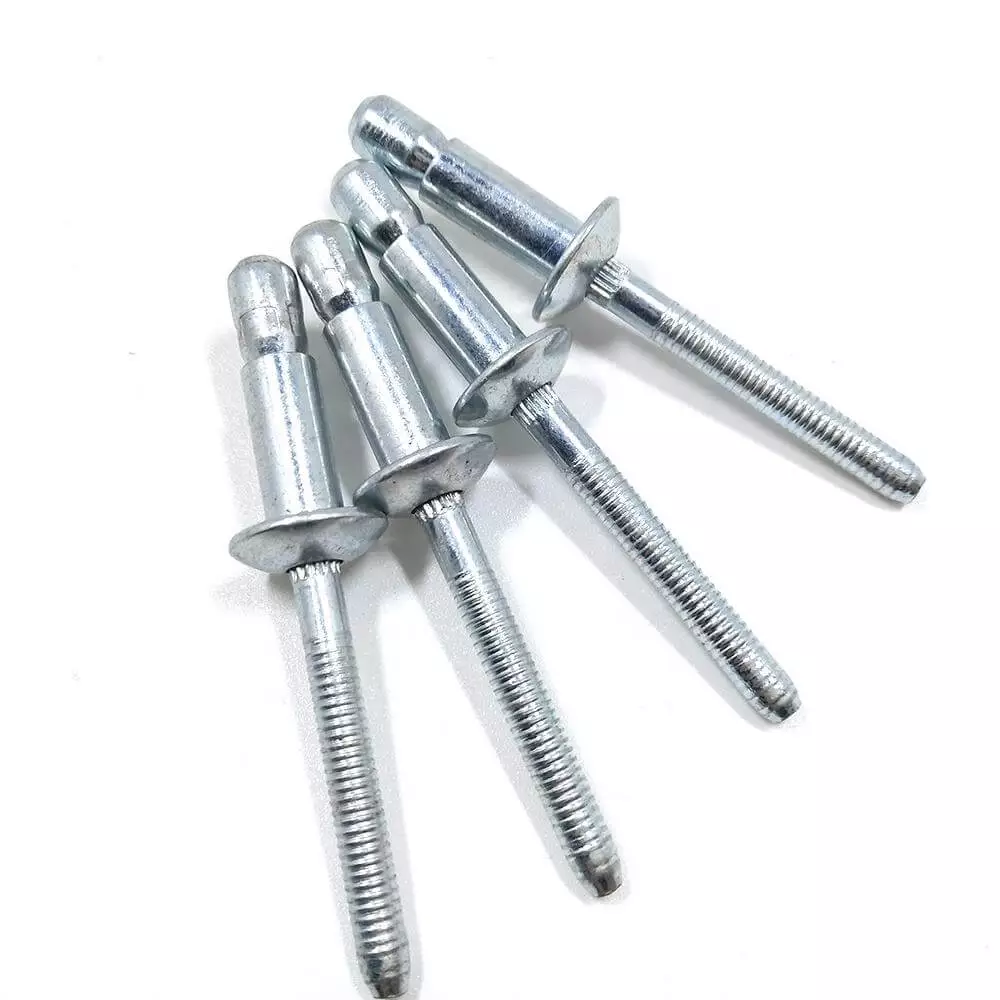
4. Copper Rivets
Rivets made of Copper have unique advantages in electrical systems. Copper rivets work well in connection structures where high electrical conductivity is required. Copper has very high electrical and thermal conductivity, and its flexibility also makes it well adapted to the deformation of parts or soft structures.
Riveting process, copper deformation consistency is excellent, conducive to the formation of a stable grip. However, copper rivets are relatively high cost, less than the strength of carbon steel and stainless steel, mainly for functional requirements rather than load-bearing connections.
Monel rivets represent the value of high-end materials for extreme applications. These rivets have superior corrosion, temperature and fatigue resistance and are used in specialized applications such as offshore engineering, chemical installations, nuclear reactors, military systems, etc. These materials are resistant to corrosive media such as chlorine ions, strong acids and alkalis, hydrogen sulfide, etc. They are far superior to traditional metal materials.
These materials are resistant to corrosive media such as chlorine ions, strong acids and alkalis, hydrogen sulfide and other corrosive media, and their performance far exceeds that of traditional metal materials.Monel rivets are widely used in ships, offshore platforms and sea-wind turbine foundation connections. Despite their excellent performance, they are often used for special projects and are not suitable for general industrial use due to the extremely high cost of the material and the difficulty of processing.
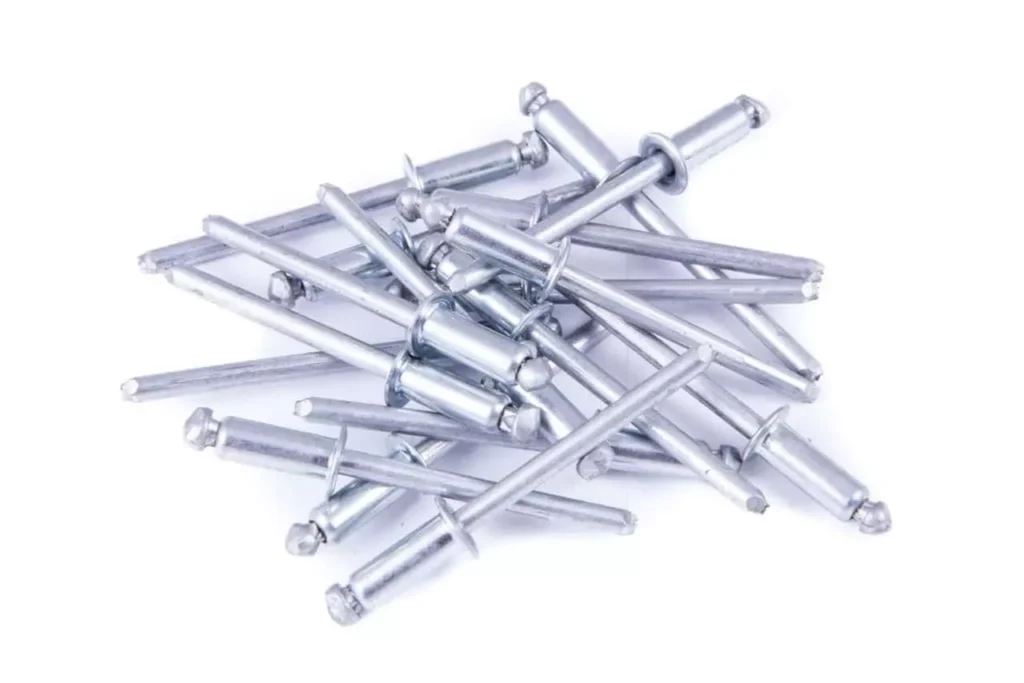
6. Plastic / Nylon Rivets
Plastic / Nylon rivets, on the other hand, are ideal for lightweight and electrical insulation requirements. Their light weight, non-conductive and non-rusting properties perform well in low-strength, non-structural connection scenarios.
Nylon rivets are tough and can be installed without metal tools to avoid damage to the substrate. However, they are unable to withstand large loads and are less resistant to heat, UV light and long-term fatigue. Plastic rivets are not recommended for outdoor, high temperature or long-term load systems.
Recommended Rivet Materials by Application
Application Scenario | Recommended Rivet Materials | Reasons for Recommendation |
---|---|---|
Solar modules and mounting systems | Aluminum / Stainless Steel | Lightweight, corrosion-resistant, matches thermal expansion |
Industrial equipment & steel structures | Carbon Steel / Stainless Steel | High strength, economical (CS), rust-resistant (SS) |
Coastal or high-salinity environments | Stainless Steel / Monel | Excellent corrosion resistance in marine climates |
Electrical devices / grounding points | Copper / Aluminum | Superior conductivity for electrical contact |
Aerospace / lightweight transportation | Aluminum / Nickel Alloys | High-performance, heat and corrosion resistance |
Enclosures, cable trays, boxes | Stainless / Multi-grip Aluminum | Stable fastening, anti-theft, fits various panel thickness |
Appliances / electronics housing | Nylon / Plastic | Lightweight, insulating, rust-free for non-structural use |
BIPV / architectural visible systems | Aluminum / Hidden Stainless | Aesthetic finish, anti-corrosion, tamper-proof connections |
How to choose the right rivet material for your project?
In industrial projects or structural connections, the correct choice of rivet material is very important. This is an important prerequisite to ensure the structural reliability, long-term stability, corrosion resistance and maintenance cost control of the system.
Step 1 : according to the connection substrate matching material, to avoid galvanic corrosion
The rivet material should be as electrochemically compatible as possible with the material being joined. Otherwise, galvanic corrosion can easily occur in humid or salt spray environments. Example:
- Aluminum profile connection → Priority use of aluminum rivets or aluminum body + stainless steel core combination
- Stainless steel plate → stainless steel rivets can be used, but avoid mixing directly with carbon steel
- Galvanized steel structures → carbon steel rivets + Dacromet coating optional, or use aluminum + corrosion-resistant gasket isolation
📌 Special Note: High risk of mixing aluminum and carbon steel, not recommended for bare joints
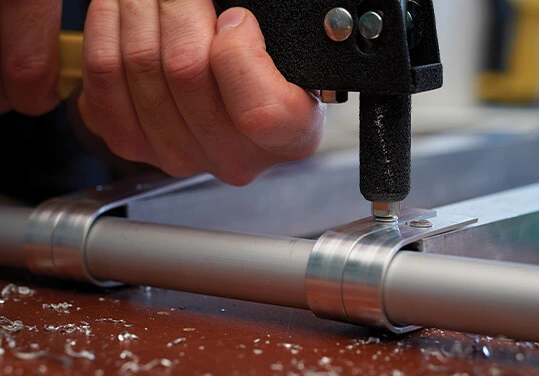
Step 2. consider the use of the environment: corrosion level determines the material grade
Different environments have different requirements for corrosion resistance. Selection of materials need to consider the atmospheric conditions in which the project is located, the influence of water vapor, chemical corrosion sources and other factors.
- Indoor, dry places → carbon steel rivets can be used, economical and applicable
- Ordinary outdoor environment → recommended to use aluminum or galvanized carbon steel
- High humidity, coastal, high salt spray environment → preferred stainless steel or nickel alloy rivets
- Acid and alkali or industrial environments → 316 stainless steel or Monel is recommended.
Step 3. According to the structural function to determine the strength level requirements
According to the structural function to determine the strength level requirements
- Different connection parts bear different loads and stresses, rivets should match the strength of the material:
- Main load-bearing connections / shear parts → recommended use of carbon steel or stainless steel rivets
- Light assemblies / non-load bearing structures → aluminum or plastic rivets can be used.
- Dynamic loads (wind vibration, railroad track) → high fatigue strength materials need to be considered, such as stainless steel or alloy rivets
📌 Rivmate can provide tensile and shear strength test reports to support selection decisions.
Step 4. according to the process conditions and installation methods to consider the processability
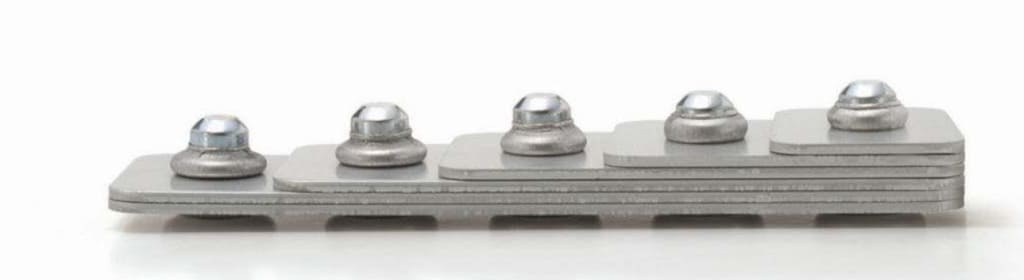
Material riveting processability and equipment matching also affect the use of results:
- Aluminum rivets → simple installation, suitable for most tools, suitable for on-site construction
- Stainless steel rivets → high hardness, need high power pneumatic/hydraulic tool support
- Nylon rivets → can be assembled manually, suitable for light industrial and non-metallic shell connections
- Multi-layer materials or unequal thicknesses → Multi-Grip or Bulb-Tite construction rivets are recommended.
Step 5. Consider system life and certification requirements
Certain systems such as photovoltaic, electric power, and rail transit, need to meet a design life of 25 years + with international certification requirements. The material should have:
- Long-lasting corrosion resistance (≥ 240h salt spray test)
- RoHS / REACH environmental compliance
- ISO 14589 mechanical standard support
- Material certification (MTC) and third-party test reports are available.
Consequences of choosing the wrong rivet materials
If you choose the wrong rivet material for your project, it can lead to a host of bad outcomes. Commonly, failure to consider the joining substrate, galvanic corrosion, load strength or environmental factors often has serious consequences later in the project.
Common problems include:
- Galvanic corrosion: e.g. aluminum profiles with carbon steel rivets, where the aluminum is rapidly corroded and perforated in humid environments.
- Corrosion failure: such as carbon steel rivets used in outdoor or seaside projects, rust and corrosion in a short period of time off the core, connection failure.
- Insufficient strength: such as aluminum rivets used in load-bearing structures, not enough tension and shear force leads to loosening, falling off.
- Thermal expansion mismatch: such as stainless steel rivets connected to aluminum, thermal expansion and contraction frequently triggered by riveting point fatigue cracking.
Rivmate Rivet Material Properties Solutions
Reliable, high-performance rivet material systems for a variety of industrial joining scenarios
Rivmate understands that rivet material selection is critical to system stability, corrosion protection and structural safety. As a result, we offer not only a standardized range of materials, but also a matrix of material solutions for the photovoltaic, electrical, rail, and construction industries to achieve a precise balance of performance, cost, and engineering fit.
Whether your project involves light-duty construction, corrosion challenges, or high-strength connections in complex environments, Rivmate offers a full range of fastening solutions, from the material source to the structural package. Feel free to submit your scenarios or connection drawings and we will recommend the most appropriate rivet material configuration and sample program.
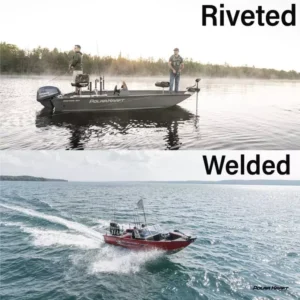
Strength of Welded vs Riveted Ship:A Comprehensive Guide
Strength of Welded vs Riv
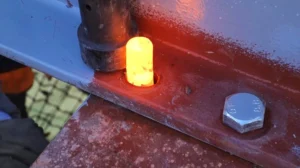
What is the Melting Point of Aluminum Rivets?
What is the Melting Point
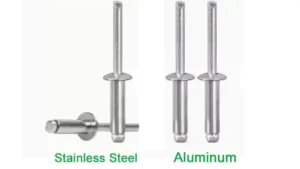
Pop Rivet Strength Stainless vs. Aluminum
Pop Rivet Strength Stainl
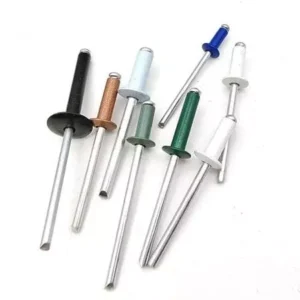
The Comprehensive Guide to Blind Rivet Material Selection
The Comprehensive Guide t