How to Choose Hidden Rivet Fasteners for Solar Mount?
Table of Contents
How to choose hidden rivet fasteners for solar mount?
By reading this blog, you will get to know about the applications, considerations and verification methods of rivet fastener for solar mount. Let’s explore it together!
what are Hidden Rivet Fasteners?
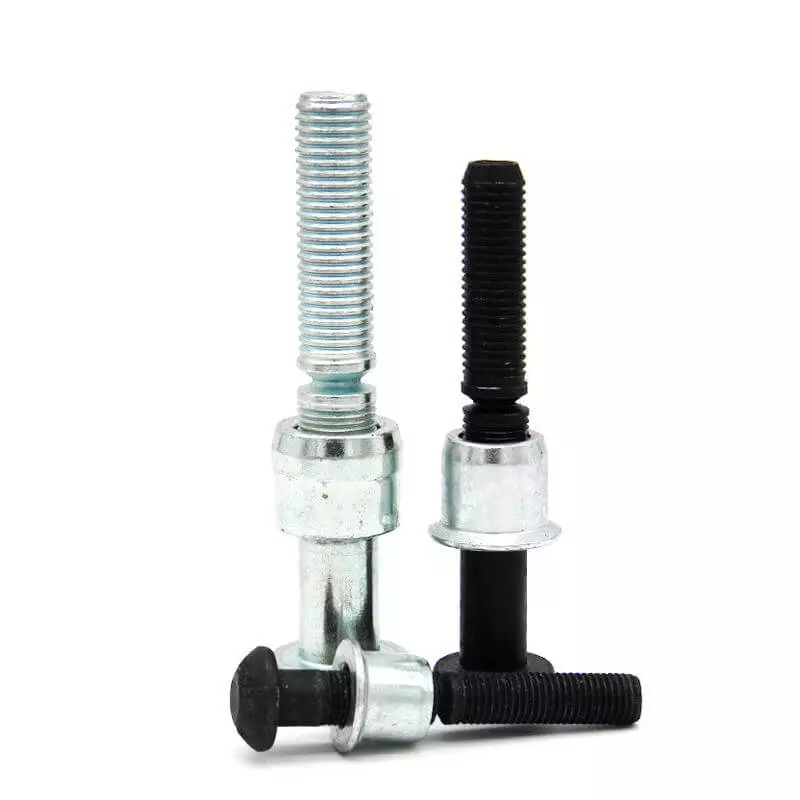
Hidden rivet fasteners are a type of rivet construction that does not expose the mandrel, does not protrude the rivet head, and does not affect the appearance or function of the rivet after installation. These rivets are designed for aesthetically pleasing structures, burglary and tamper resistant applications, or where sealing is required. Its core features include: closed structure, flat head or inline design, and no sharp protrusions after installation. They retain the high strength and permanent locking characteristics of riveted joints.
Why is it critical in Solar Mounting?
The role of hidden rivets is especially critical in Solar Mounting Systems. It is mainly reflected in the following aspects:
1. Aesthetic requirements
Solar Mounting Systems are increasingly used in residential roofs, BIPV building facades, metal roofs and other scenarios. These applications require that external connections are not exposed and do not affect the visual unity of the structure. hidden rivets have a clean appearance after installation and no mandrel protrusions at riveted joints. Hidden rivets have a clean appearance after installation, and are therefore ideal for use in visible areas such as the front of the rail and the surface of the edge press.
2. Anti-theft and anti-tampering
In open roof or ground power plants, exposed rivet mandrels are often used to illegally dismantle components or accessories. Concealed rivets significantly improve the anti-theft factor because the broken core is not exposed and the connection is irreversible. Therefore, they are widely used in inverter shells, cable covers and other parts.
3. Waterproof sealing
Many solar racking components (such as electrical covers, racking bases, junction box support plates) need to be kept sealed and waterproof at the riveting points. While ordinary open end rivets form a water ingress channel when the mandrel breaks, closed end Hidden rivets ensure that the entire connection structure is impervious to seepage, rust and condensation.
4. Safety and construction consistency
Hidden rivets have no exposed metal edges, avoiding scratches to operators or cable lines during construction or maintenance. In addition, the hidden rivets mostly use mechanical locking core or fixed-point broken core structure, installation quality can be seen, high reliability, suitable for automated or semi-automated assembly process.
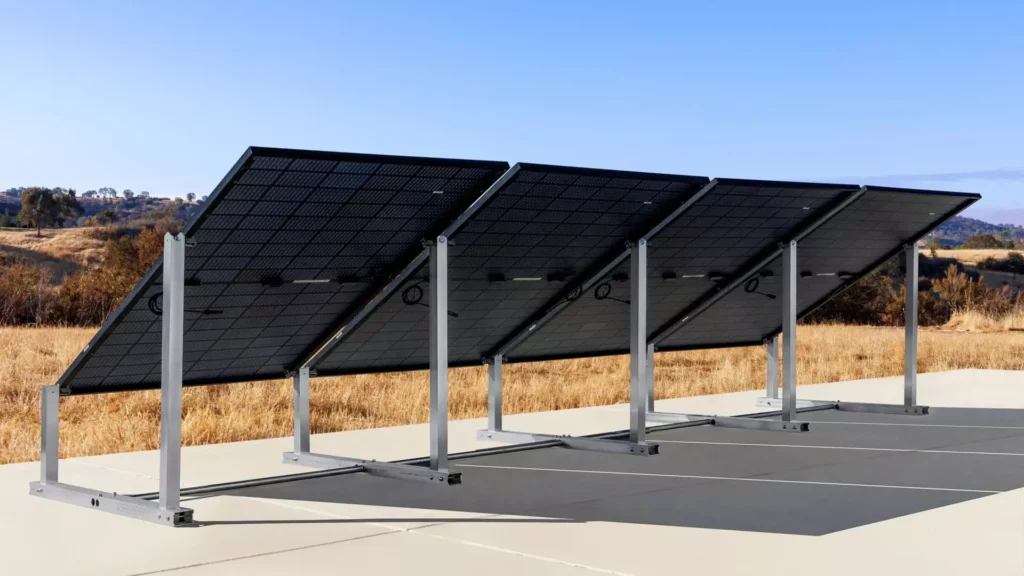
Typical Applications for Blind Rivets in Solar Mount Systems
Blind rivets are riveted fasteners that can be installed from one side. Therefore, they are very suitable for connection scenarios where the backside of the structure is not accessible or the assembly space is limited. At Solar Mounting Systems, blind rivets are used in a variety of critical applications due to their high efficiency, ease of installation, and structural reliability. Blind rivets play an irreplaceable role in industrial grade module installation, power plant construction and distributed roofing projects.
1. Racking rail and roof connection base fixing
When installing solar racking on metal roofs, color steel tiles or concrete bases, the base of the rails usually needs to form a stable, shear-resistant, long-term corrosion-resistant fixed connection with the roof. Since the back of the roof panel is not accessible, blind rivets are ideal.
2. Concealed connection of component side/center blocks to guide rails
In systems where aesthetics or simplicity of installation are important, the component side or center blocks can be attached to the rail from the inside using blind rivets. This allows for concealed locking and eliminates the need for exposed external bolts.
- Recommended Type: Flush-head Closed-End Blind Rivets
- Characteristics: Flush-head is not exposed after installation, no cuts, no water accumulation, especially suitable for residential roofs and visible area installation projects.
3. Quick assembly of accessories such as cable trays, raceways, shrouds, etc.
Solar Mount projects often require a large number of auxiliary accessories. Such as cable trays, cable guide brackets, guards, electrical boxes and so on. These components are large in volume, frequent in operation, and require moderate accuracy, making them suitable for quick positioning and fixing with blind rivets.
- Recommended type: Open-End or Multi-Grip Blind Rivets
- Characteristics: large holding range, high fault tolerance, adaptable to different plate thickness and hole diameter deviation, fast installation, greatly enhance the efficiency of on-site construction.
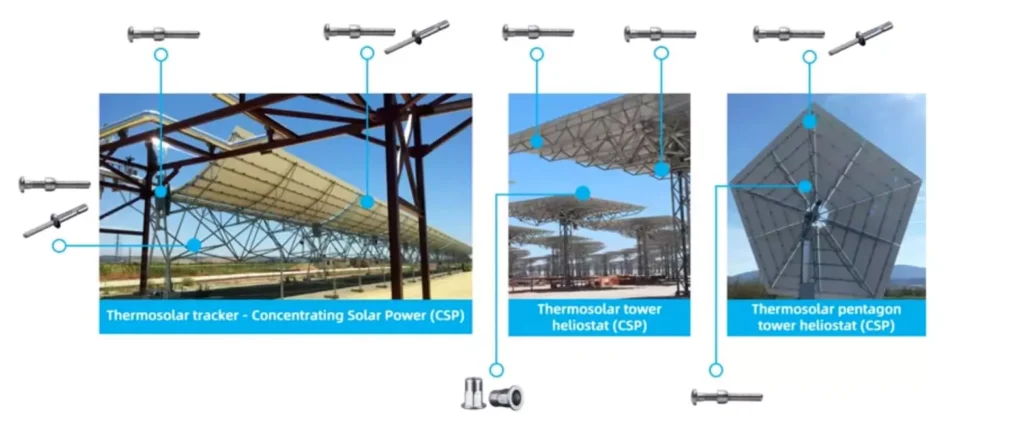
4. BIPV Roof Structure Module Attachment (Invisible Back Assembly)
In building-integrated photovoltaic (BIPV) projects, solar modules are integrated directly onto metal tiles or curtain wall panels. The riveted areas are mostly thin, non-metallic, closed structures. Screws or double-sided operating tools cannot be used in these areas.
- Recommended type: Bulb Tite Blind Rivets
- Characteristics: Tri-fold structure distributes the expansion force, preventing the thin plate from tearing and warping of the surface layer, suitable for aluminum alloy, composite materials and other lightweight structures to be connected.
five core factors to consider when choosing the rivet fasteners for solar mounting
Selecting the right rivet fasteners for Solar Mounting is a critical part of ensuring the structural stability, corrosion resistance, construction efficiency and service life of the entire system. The following are the five core selection factors that must be considered, each of which has a direct impact on the quality of the connection and the operational reliability of the system:
Dimension | Key Considerations | Desired Outcome |
---|---|---|
Structural Type | Is it a primary or auxiliary connection? Single or blind-side access? | Choose structural, blind, or quick-install rivets appropriately |
Material Compatibility | Is the rivet metal compatible with the substrates? | Avoid galvanic corrosion, match thermal expansion |
Corrosion Resistance | Salt spray rating? Need sealed design? | Ensure long-term rust resistance and watertight sealing |
Installation Compatibility | Are tools compatible? Is on-site installation feasible? | Maintain efficiency and consistency in field installation |
Service Life & Standards | Does it meet 25-year PV system lifecycle? Is it certified? | Select products with validated test data and compliance certifications |
Core Factor 1: The type of structure of the connection part
There are also differences in the way different parts of the connection are loaded. The choice of rivet structure is also different:
- The main load-bearing connections (such as rails and roof, bracket column): the need to use high-strength structural rivets (such as Monobolt, Lockbolt), to ensure that the tensile and shear does not loosen.
- Non-load-bearing auxiliary connections (such as cable covers, wiring brackets): can use a wide range of grip, easy to install Multi-Grip or Bulb-Tite rivets.
- Hidden installations or areas where appearance is critical: Flush-head or closed-end rivets are recommended to avoid exposed mandrels.
📌 Suggested Judgment Criteria: Is the location subject to long-term wind loads? Can it be operated from both sides? Is it a visible area?
Core Factor 2: Material Compatibility and Electrochemical Matching
Rivet material must match the connection material to avoid galvanic corrosion:
- Aluminum alloy structure (such as frame/rail): It is recommended to match aluminum body + stainless steel core rivets to ensure the consistency of thermal expansion and corrosion resistance.
- Galvanized steel, color steel tiles, steel beam structure: It is recommended to use galvanized steel rivets or Dacromet treatment to prevent corrosion reaction between aluminum – iron.
- Composite panels, BIPV substrate: It is recommended to use three-flap or soft expansion structure with low expansion pressure to avoid interlayer rupture.
📌 Pit Avoidancer: Carbon steel exposed rivets are strictly prohibited for aluminum profile connections, especially in wet or coastal projects.
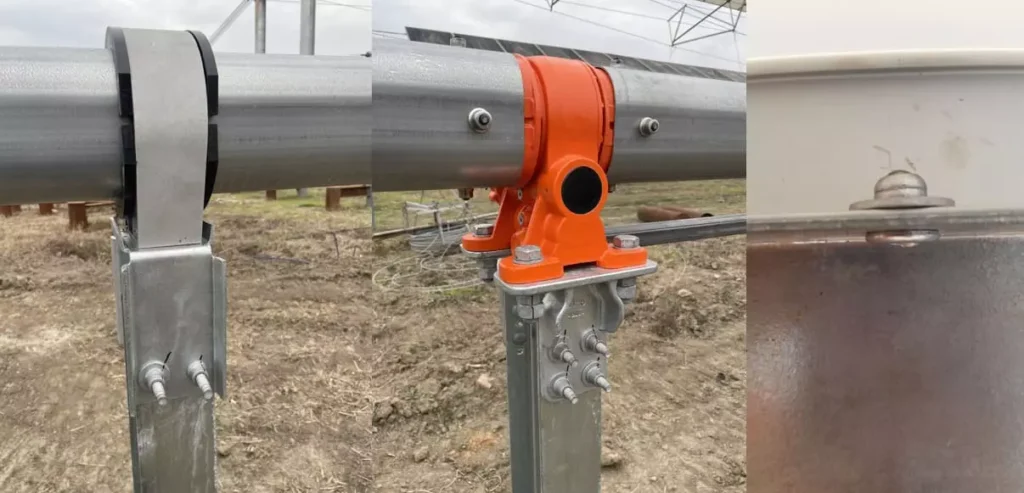
Core Factor 3: Corrosion Resistance
Solar Mount systems are exposed to harsh outdoor environments throughout the year and rivets need to have excellent weathering properties:
- It is recommended to select products that have passed ≥240 hours of neutral salt spray testing.
- Available finishes include: anodized, Dacromet, zinc plating + closed passivation, etc.
- Enclosed structure effectively prevents rainwater, sand and dust from entering the connection core, prolonging its life.
📌 High-risk environments: seashores, acid rain areas, high concentration of industrial emissions recommend the use of stainless steel or specially coated rivets
Core Factor 4: Mounting methods and tool compatibility
Solar Mount projects are often high-altitude, high-volume jobs where installation efficiency is critical:
- Is it a blind hole structure? → Blind Rivets should be used.
- Does it support quick on-site installation? → Blind Rivets with a clear, visually identifiable broken core are recommended.
- Is it compatible with existing tools? → Rivet size (core diameter/stroke) should be compatible with commonly used rivet guns/pneumatic guns.
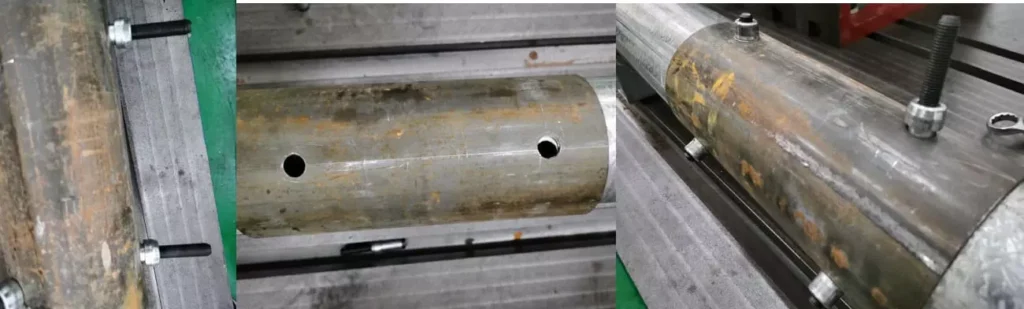
Core Factor 5: Life expectancy and structural certification standards
Rivet connections must maintain the same life expectancy (20-30 years) as the PV system body and meet relevant certification standards:
- Mechanical properties should meet the requirements of ISO 14589 / DIN 7337 / ASTM F1470 standards.
- Shear force, tensile force test report and material composition certificate should be provided by the factory.
- High-end items should be certified by third-party testing organizations (e.g. SGS, TÜV).
- Environmental compliance: RoHS / REACH compliant, especially for export projects.
Performance requirements and validation methods for rivet fasteners in solar mounts
In solar racking systems, rivet fasteners must have high strength, corrosion resistance, reliable locking and good mounting consistency. Only with these characteristics can they be adapted to the harsh environment of long-term outdoor operation. Key performance requirements include:
- Tensile / shear strength: withstand wind loads and structural stresses, structural rivets need to be ≥4.5-6.0kN;
- Anti-corrosion ability: through the ≥ 240 hours salt spray test, it is recommended to use stainless steel or Dacromet treated products;
- Lock core security: the mandrel should be locked and not exposed after riveting to prevent loosening or water ingress;
- Installation reliability: support for single-sided installation, mandrel breakage needs to be clearly prompted to ensure construction consistency;
- Fatigue and environmental testing: Long-term stability is verified through thermal cycling, moisture and heat, and vibration testing.
These properties are the basis for ensuring that Solar Mount rivets achieve a 25-year design life on your project.
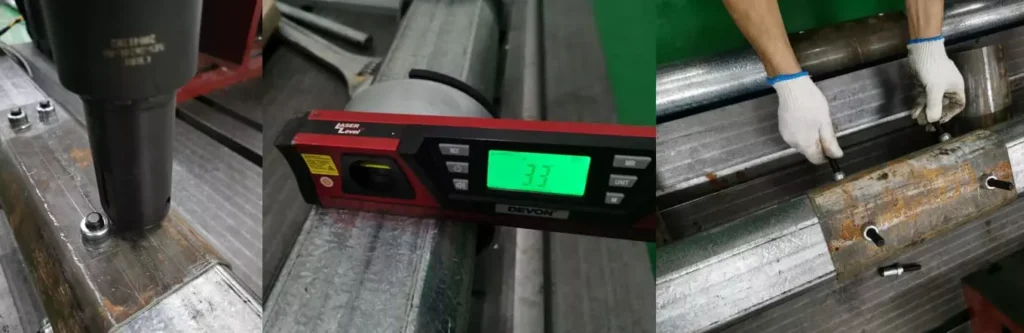
Why Choose Rivmate Solar Mount Rivets?
As a key connecting element in a solar mounting system, choosing the right rivets is critical to the structural stability, corrosion resistance and long-term operational safety of a project.Rivmate specializes in photovoltaic fastening technology. Rivmate specializes in PV fastening technology and offers a wide range of riveting solutions for Solar Mounts, including structural, closed and triple-flap types. And our solar mount rivets are ISO and salt spray certified to meet global PV engineering standards.
Whether you are a mount manufacturer, module manufacturer or EPC engineer, Rivmate can provide you with samples, drawings, selection support and efficient delivery. Contact us for a rivet recommendation for your project or meet us at the next fastener show.
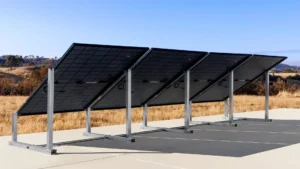
How to Choose Hidden Rivet Fasteners for Solar Mount?
How to Choose Hidden Rive

How to Choose Rivet Fasteners for Solar Roof?
How to Choose Rivet Faste
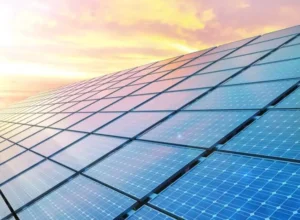
How to Choose Rivet Fasteners for Solar Cover?
How to Choose Rivet Faste
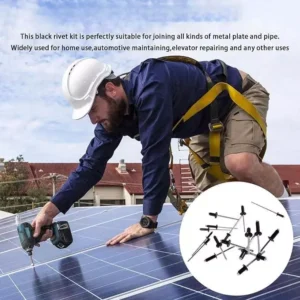
How to Choose Rivet Fasteners for Solar Panels?
How to Choose Rivet Faste