Home » 归档于 eric@world-rivet.com » 第3页
Best Ways to Set a Pop Rivet
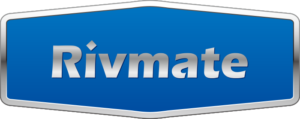
Rivmate Fastener
Top Rivet and Rivet Nut Manufacturer in China
Table of Contents
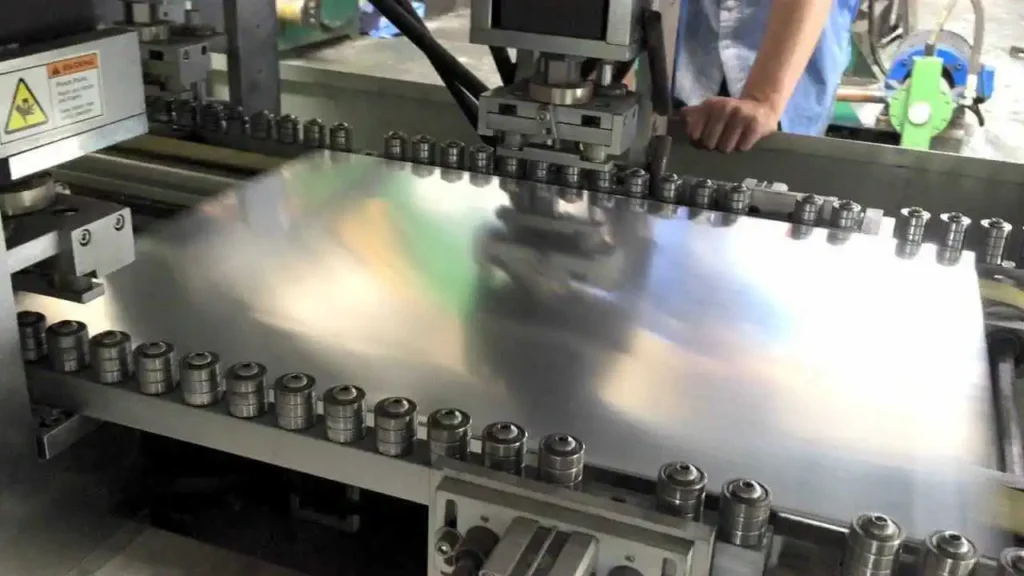
You will know the best way to set a pop rivet by reading the guide.
There are many different types of rivets, and blind rivets are the most popular. Anyone who uses a blind rivet on a regular basis knows that a blind rivet provides a permanent connection that will not loosen over time like bolts and screws do. The construction of a blind rivet dictates that it is easy to set, extremely strong, and suitable for a wide range of materials from metals to plastics to composites. However, the prerequisite for all these roles and advantages is that you need to set a pop rivet correctly.
Pop rivets are installed the same as most blind rivets, using a pop rivet tool to pull the rivet mandrel for installation.
Table of Contents
What Tools are Needed to Set A Pop Rivet?
Common pop rivet tools available on the market and in applications are as follows:
- Manual rivet gun: suitable for aluminum, small specifications, portable and low cost.
- Electric rivet gun: suitable for light industry, maintenance operations, constant tension.
- Pneumatic rivet gun: suitable for high-frequency assembly line, stainless steel or structural rivets.
If you want to know more about pop rivet tools, read this article “Types Of Rivet Guns And What Are Rivet Guns Used For”.
How do you set a pop rivet correctly?
Steps for proper installation of blind rivets:
- Pre-drill matching holes (slightly larger than the rivet diameter about 0.1-0.3mm);
- Inserting the rivet, ensuring that the cap edge is tight against the parent material;
- Pulling the rivet mandrel using a rivet gun;
- The tail of the rivet expands to secure the material and the rivet mandrel breaks at the breaking point;
- The rivet mandrel can be automatically ejected or left in the rivet body after breakage.
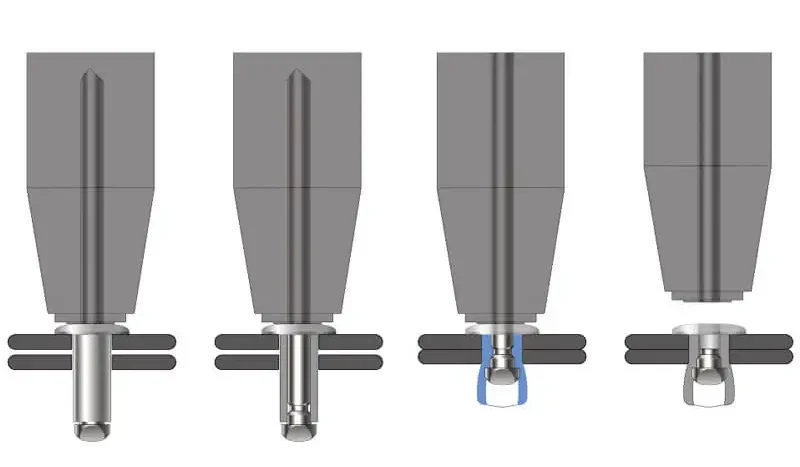
Do You Have Any Questions?
Let Us Solve Your Problem
What size drill bit should I use for a specific rivet size?
The relationship between drill hole size and rivet diameter is very critical, which directly affects the rivet installation firmness, expansion effect, clamping force and safety in use. Drill hole size to match rivet diameter. The reference standards are as follows:
Rivet Diameter | Recommended Drill Bit |
2.4 mm | 2.5 – 2.6 mm |
3.2 mm (1/8″) | 3.3 – 3.4 mm |
4.0 mm | 4.1 – 4.2 mm |
4.8 mm (3/16″) | 4.9 – 5.0 mm |
6.4 mm (1/4″) | 6.5 – 6.6 mm |
Basic principles
- Drill diameter should be slightly larger than the rivet body diameter
- Ensure smooth insertion of the rivet mandrel into the rivet body
- Avoid the rivet difficult to install or installation of the wall of the hole cuts
- Maintain sufficient friction fit to prevent the rivet from rotating and loosening.
Typical recommendation: hole diameter = rivet diameter + 0.1mm ~ 0.3mm
- The hole is too large: the rivet rotates, can not be clamped, affecting the shear strength The rivet can not be inserted. Core break point offset, abnormal structural forces.
- Hole too small: head slippage, hole wall cut deformation. Installation difficulties, core deflection, rivet head deformation.
How do I Know If the Rivet is Set Properly?
Judgment Criteria:
- The rivet mandrel has been broken and the break is neat.
- The rivet cap is tightly attached to the material performance, flat and without warping.
- The material is firmly clamped, connected tightly without shaking.
- No “empty hit”, “soft rivet”, “rotation” phenomenon.
- Uniform expansion of the tail, no breakage or collapse.
- No obvious indentation, deformation or cracks on the surface of the material.
Do You Have Any Questions?
Let Us Solve Your Problem
Can I Set a Pop Rivet Without a Rivet Gun?
It is theoretically impossible to install pop rivets without using rivet guns. This is because pop rivets are designed with strict design requirements in mind.
- Provide sufficient pulling force (hundreds to thousands of newtons) to pull the rivet mandrel.
- The rivet mandrel must break at a specific break point.
- Hand tools such as pliers and hammers make it difficult to ensure clamping force and directional accuracy.
The rivetless alternative is limited to emergency situations and carries a high risk of damage to the workpiece.
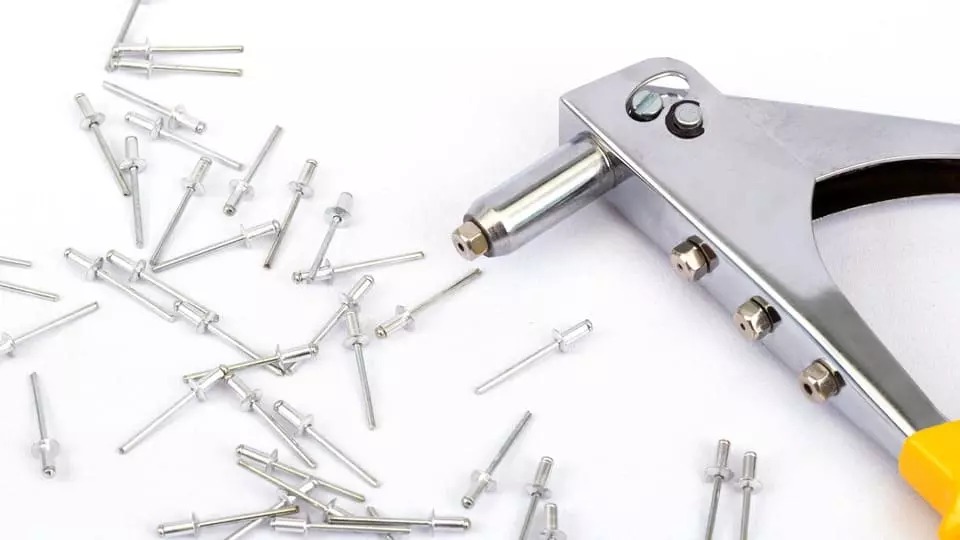
Can Pop Rivets be Used on Plastic, Metal, or Composite Materials?
Yes, POP rivets can be widely used in plastic, metal and composite materials. However, it is necessary to choose the appropriate rivet type, material and cap structure according to the characteristics of different materials to ensure a strong connection, structural safety and no damage to the material.
Ⅰ. Metal
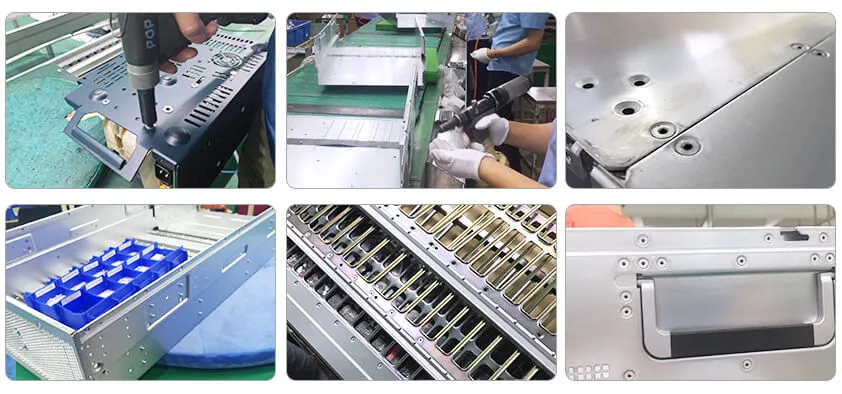
Pop rivets are great for use on metal materials, riveting metal products is the most common use of pop rivets.Pop rivets can be riveted to a wide range of different materials including aluminum, stainless steel, carbon steel, copper and more.
Recommended rivet types are listed below:
- Aluminum rivets: light duty structures such as sheet metal, electrical housings
- Steel/stainless steel rivets: medium to high strength connections, e.g. vehicles, mechanical assemblies
- Structural POP rivets: e.g. BOM, Interlock, for high shear/vibration requirements.
Ⅱ. Plastic
Pop rivets feature the ability to rivet many different materials, including plastics. When riveting plastics, care needs to be taken to prevent the material from cracking, deforming, or penetrating.Pop rivets are commonly used in shell assemblies, electrical panels, 3D printed parts, and more.
Recommended rivet types:
- Large Flange: spreads pressure, prevents indentation.
- Closed-End: waterproof sealing, to protect the internal circuitry
- Plastic-specific rivets (such as resin rivets): flexible deformation, not to hurt the material
- Used with gaskets to prevent perforation expansion
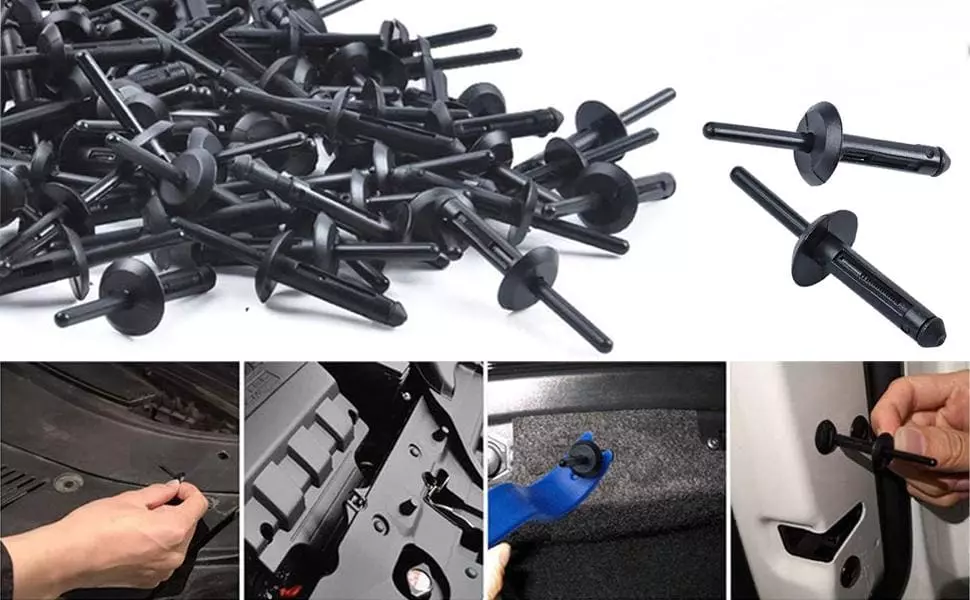
Ⅲ. Composite Materials
Pop rivets can be used on composite materials, but the material properties vary greatly (e.g. carbon fiber, fiberglass, honeycomb panels). A rivet structure with uniform stress distribution and low impact deformation is required.
Recommended rivet types:
- Sealed rivets: to prevent stress concentration caused by the residual core.
- Multi-Grip: Adapt to the difference in layer thicknesses, uniform clamping.
- Washers or backing plates can be added to avoid localized stress concentration.
What type of pop rivet should I use for a specific application?
There are many types of Pop rivets, you need to choose according to the actual needs of your business. The common types of rivets and their applications are as follows:
- Dome head: universal, standard installation;
- Countersunk: mounting surface needs to be flush for normal use;
- Large flange: soft material/plastic parts, increase the force area;
- Sealed/closed-end: sealing, waterproof occasions;
- Multi-grip: adapted to different thicknesses of materials, reducing the types of inventory.
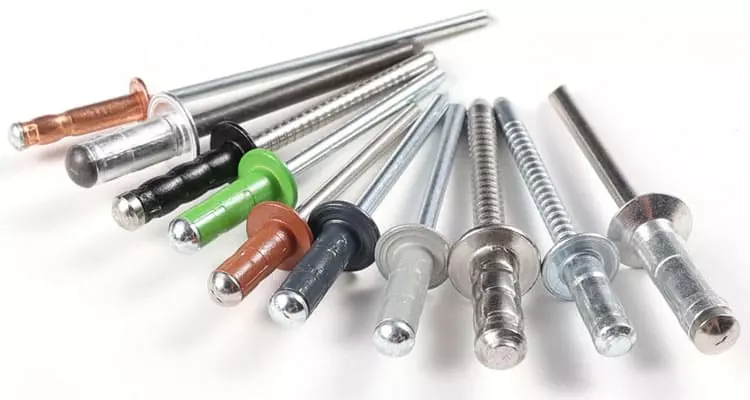
If you want to learn more about rivet types and their applications, read this article “Types of Rivets and Their Application – The Ultimate Guide”.
Why is the rivet not pulling tight or not breaking off?
If not done correctly when setting a pop rivet, it may cause the rivet to fail. Common causes are listed below:
- The rivet hole diameter is large and the pull core tension is dissipated;
- Mismatch between the rivet and the thickness of the parent material, the expansion area is not fully compressed;
- Insufficient tension in the rivet gun or slipping of the jaws;
- The use of unsuitable rivet material (such as aluminum core pull steel mandrel)
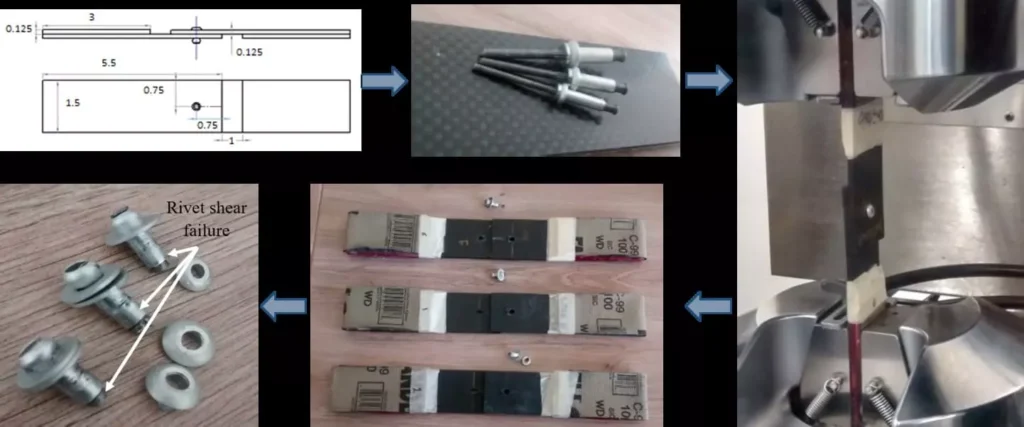
There are many reasons why set pop rivets fail, here is just a list of the common ones. In order to achieve perfect rivets, you need to know the causes and solutions for rivets failure.
What causes a pop rivet to spin during installation?
After installing the pop rivets, there will be times when you will notice the pop rivets rotating, this is a case where the rivets fail. The reason for the rotation is as follows:
- The hole diameter is too large → the rivet cannot make stable contact with the hole wall;
- The material is too soft → the cap edge of the rivet sinks into the surface;
- The pull core is not stuck firmly → the rivet gun can not be pulled to cause rotation;
So how do you resolve this situation?
- Repunch and replace matching rivets;
- Replacement of large cap edge types;
- Using rivets with anti-spin construction or special fixtures.
Custom Riveting Solutions for Your Business
This blog shows you the best ways to set a pop rivet. including what to look for and what can happen when setting pop rivets.
If you don’t know how to choose the most correct rivets and set pop rivets method for your project, please contact us!
Get rivets for testing today!