Home » 归档于 eric@world-rivet.com » 第2页
Are Closed End Rivets Waterproof?
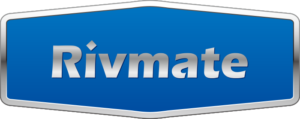
Rivmate Fastener
Top Rivet and Rivet Nut Manufacturer in China
Table of Contents
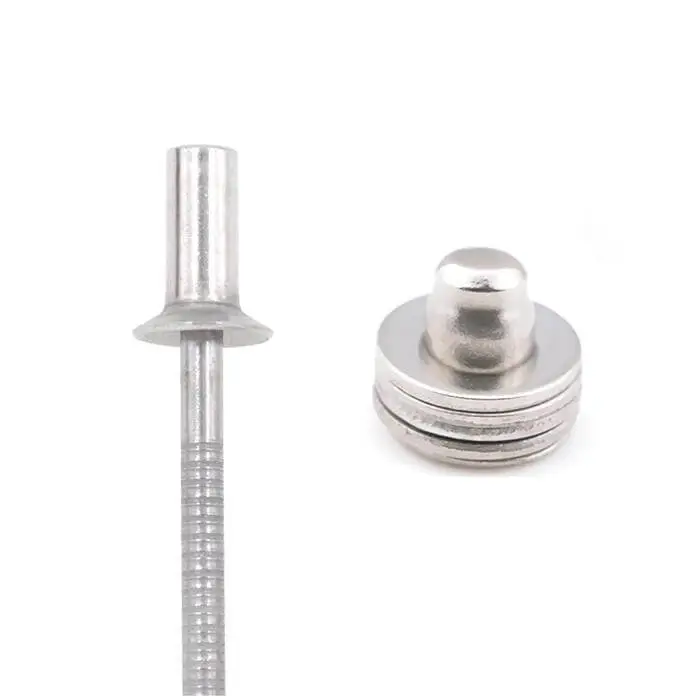
Are closed end rivets waterproof? I’m sure everyone who uses closed end rivets will want to dive into this. This blog will explain the question “are closed end rivets waterproof” from the structure of closed end rivets, waterproof match and waterproof principle.
Table of Contents
What are closed end rivets?
Closed End Blind Rivets (Sealed Type Blind Rivets) are a type of blind rivet specifically designed to provide sealing performance. It is structurally improved on the basis of the traditional open end rivets, and is characterized by the closed end of the rivet body (i.e., the “closed end”), forming a sealed cavity structure. This structure can effectively prevent moisture, gas, dust, etc. through the rivet hole penetration after riveting is completed, widely used in the sealing, corrosion resistance requirements of the scene.
Structural features:
- Closed type rivet shell: the end of the solid seal design, after riveting, the mandrel remains in the rivet body but does not penetrate the bottom of the shell. Eliminate the “center channel” leakage problem that exists with open end rivets.
- Automatic locking of the mandrel: the mandrel is mechanically locked after pulling off, which enhances the structural strength and ensures that it will not fall off or come loose.
- Blind Side: Still has the advantages of blind rivets for one side assembly, suitable for closed structures where the back side is not accessible.
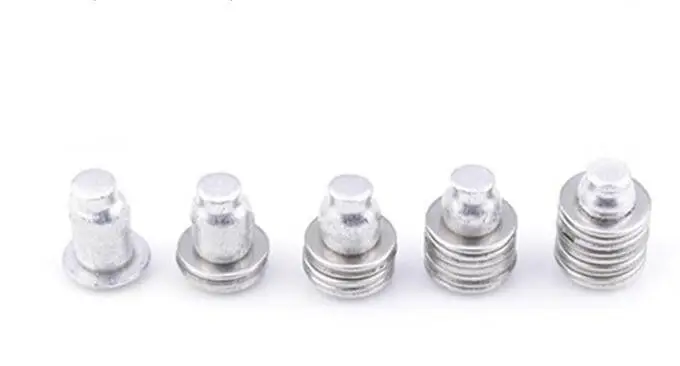
Comparison Criteria | Closed End Rivets | Open End Rivets |
---|---|---|
Tail Structure | Fully sealed tail prevents fluid or gas ingress | Open tail allows mandrel access; no sealing capability |
Sealing Performance | ✅ Excellent sealing against water, dust, oil | ❌ No sealing; prone to leakage |
Mandrel Retention | Mandrel is fully locked inside the rivet body | Mandrel may partially remain or become loose |
Suitable Environments | Moist, corrosive, or sealed applications (e.g., enclosures, marine use) | General-purpose, non-sealed industrial applications |
Structural Strength | Slightly higher; mandrel lock enhances tensile strength | Standard strength; suitable for light to medium-duty connections |
Material Combinations | Typically aluminum/steel, stainless/stainless (for corrosion resistance) | Broad use of materials like aluminum, steel, stainless steel |
Manufacturing Cost | Slightly higher due to more complex structure | Lower cost, high production efficiency |
Typical Applications | Electrical cabinets, marine components, outdoor equipment, food machinery | Sheet metal, furniture, general light-duty assembly |
Are closed end blind rivets truly waterproof?
Why are Closed End Blind Rivets “waterproof”?
#1 Structure determines the sealing
Closed end rivets are solid sealing structure, avoiding such as open end rivets through the channel, to prevent water vapor from the core stem through the hole into.
#2 Mandrel locking, no shedding gap
Rivet mandrel breakage is tightly locked in the rivet body, will not form due to the release of the mandrel caused by the “capillary gap”, to enhance the stability of the seal.
#3 Close-fitting expansion tails form a ring-shaped clamp
The tails during the expansion process are closely fitted to the base material, which helps to form a ring-shaped water-blocking structure, especially suitable for sheet metal butt joints.
But note: waterproof performance ≠ absolute sealing
Even for closed type rivets, their intrinsic sealing is structural and is not a complete substitute for specialized seals. The following points may affect its actual waterproof effect:
- Too large or burr holes → may lead to micro-leakage
- deformation of the base material or installation angle is skewed → the tail expansion is not tightly fitted
- Failure to add sealing gasket → unable to shield the small gap between the rivet cap edge and the material
- Prolonged exposure to high pressure water or corrosive environments → increased risk of leakage
Do You Have Any Questions?
Let Us Solve Your Problem
How does the closed-end design contribute to waterproofing?
Closed end design is the core of closed end blind rivets to realize waterproof function. This design structurally eliminates the “liquid channel” that is common with traditional open end rivets, providing an important guarantee of waterproof performance. The main functions of the enclosed design in terms of waterproofing are as follows:
1. Blocking the path of liquid penetration from the mandrel channel
Open end type rivets are open, the residual channel after the breakage of the mandrel is easy to become the infiltration point of water vapor, dust, oil mist.
Closed type rivet tail is completely sealed metal bottom, after riveting is completed, the mandrel can not penetrate the entire rivet body, can effectively block the possibility of water vapor into the back.
2. Formation of a stable sealed chamber structure
The rivet mandrel is pulled off and stuck inside the closed chamber and locked by the jaw structure, forming a closed metal chamber.
The tail of the rivet expands into an “umbrella” structure, forming an annular fit with the base material.
3. Avoiding micro-gap leakage caused by a loose mandrel
Under prolonged vibration or thermal expansion and contraction, open end rivets may loosen the mandrel and form hairline gaps, which are a high risk for moisture infiltration.
Closed end rivets have a mandrel that is locked in a closed housing, eliminating the risk of a “hollow core”.
4. Enhanced corrosion and airtight protection
- In high humidity and salt spray environments, water vapor infiltration can lead to internal oxidative corrosion.
- The sealing design physically isolates the core rod and parent material from outside moisture.
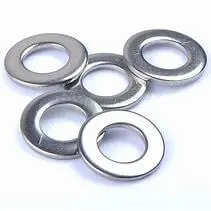
Do closed end rivets provide a full seal against water, moisture, and air?
Due to the unique structural design of CLOSED END BLIND RIVETS, closed end blind rivets offer the following basic sealing performance:
- Excellent waterproof performance in most static, light spray, low-pressure wet zone use scenarios.
- Good sealing for water vapor, moisture and other microparticles.
- Stops rapid air leakage
However, if it is used in high-pressure water environment, high airtightness or electronic sealed compartments, it is recommended to cooperate with sealing gaskets or special sealant to enhance the overall sealing level.
What materials and coatings improve the waterproof performance of closed end rivets?
How you need to use Closed-End Blind Rivets in applications where waterproofing performance is critical, then you need to choose the right material with a surface coating treatment. The right extras can enhance their waterproof, corrosion-resistant and long-term sealing performance. Here are some measures to enhance the waterproofing of closed rivets:
- Uses Stainless Steel 304/316 raw material.
- Anodizing – For Aluminum
- Zinc Plating – for steel parts
- Passivation of stainless steel body surfaces.
- Epoxy or PVDF coating (for aluminum, stainless steel)
- For use with rubber gaskets
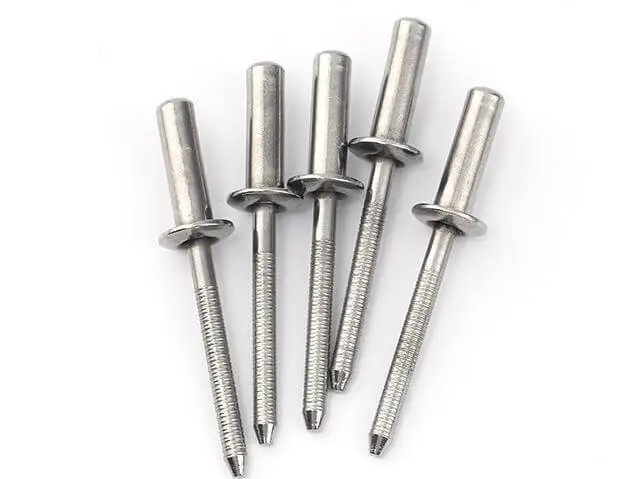
If you want to improve the waterproof performance of closed type rivets, preferred stainless steel body + passivated or anodized material combination, and in high humidity or outdoor environments with gaskets or sealants, can greatly improve the service life and sealing stability.
If you have specific application environments (e.g. IP rating, humidity and salt spray testing, contact materials), Rivmate can help you recommend a more accurate material + coating combination program.
Do You Have Any Questions?
Let Us Solve Your Problem
What are the common failure risks when using closed end rivets in waterproof applications?
While the waterproofing properties of closed type rivets are excellent, improper installation, poor material selection or inadequate environmental controls can still lead to seal failure or structural damage.
Common Failure Risks of Sealed Rivets in Waterproofing Applications
- Mismatch of punched hole size (too large or too small). Rivet fails to form a tight fit with the parent material, resulting in micro-seam water penetration.
- Insufficient installation angle or clamping force. Asymmetric rivet expansion, resulting in gaps between the tail and the base material.
- Failure to use a sealing washer or sealant. Moisture penetration between the rivet head and the contact surface of the base material.
- Material incompatibility leading to galvanic corrosion. The potential difference between the base material and the rivet material is so large that prolonged contact leads to corrosion perforation and the formation of a leakage path.
- Mandrel not completely broken or loose. Gaps or channels exist inside the rivet, reducing the sealing effect.
- The parent material itself is deformed or warped. Localized inability to fit the end of the rivet, resulting in ring seal failure.
- The use environment exceeds the material’s ability to resist corrosion. The surface of the rivet is corroded and perforated, destroying the seal structure.
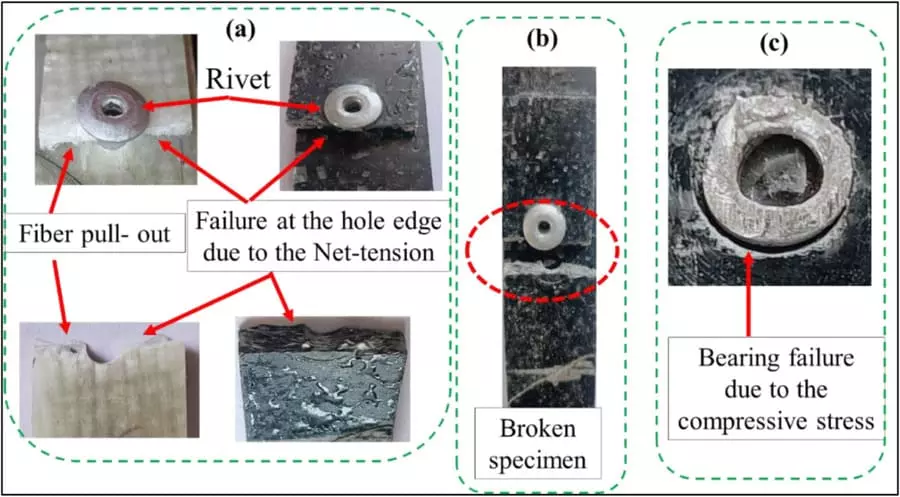
FAQs about Closed End Rivets
1. Can closed end rivets be used in marine or outdoor environments?
Closed end rivets can be used in marine or outdoor environments, provided the material and sealing are suitable for the environment.
The closed construction prevents water, moisture and corrosive substances from penetrating through the rivet channel. If used in marine environments, it is recommended to use a stainless steel rivet body + stainless steel mandrel combination, or a special anti-corrosion coated model with a waterproof gasket or sealant to cope with the harsh conditions of high salt spray and corrosion.
2. Are closed end rivets suitable for sealing electrical enclosures or watertight panels?
Closed end rivets are ideal for sealing electrical enclosures or waterproof panels.
The closed end structure prevents water, moisture and dust from penetrating through the rivet, making it suitable for use in assembly environments where waterproofing, dustproofing and corrosion protection are required. Used in conjunction with rubber gaskets or sealants, they can be further upgraded to meet industrial sealing standards such as IP65/IP67, making them an ideal fastening solution for electrical control boxes, waterproof cabinets and outdoor equipment panels.
3. Do you need additional washers or sealants to ensure full waterproofing?
Yes, to ensure complete waterproofing, it is recommended that closed end rivets be used in conjunction with an additional gasket or sealant.
While closed end rivets provide a good structural seal on their own, small gaps may exist between the rivet cap edge and the parent material. The use of auxiliary materials such as rubber or silicone gaskets, butyl sealants, etc., can effectively seal the contact surface and prevent moisture from seeping in around the rivet, ensuring that a higher level of water resistance is achieved.
Custom Waterproof Rivets Solutions for your Business
If your application or your customer’s usage scenario requires prolonged exposure to water or water vapor, then you must use waterproof rivets. But poor quality waterproof rivets are difficult to realize satisfactory waterproof effect. Therefore, it is vital for you to find a reliable rivet manufacturer.
Rivmate is a leading rivet manufacturer in China with more than 20 years of experience in rivet production. Currently, Rivmate has been supplying high quality rivets to major global rivet brands. If you want to customize your waterproof rivet solution, please contact our engineers.
Get Rivets Quote
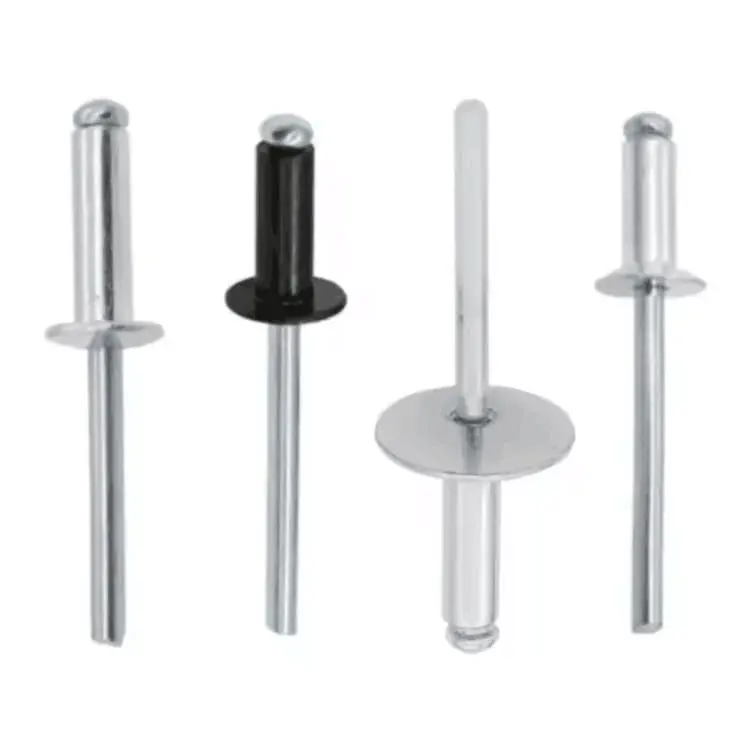
Buy Open Type Blind Rivets
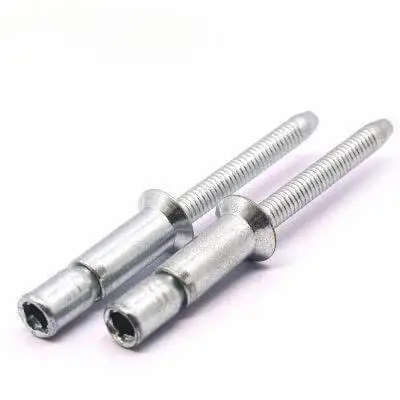
Buy Structural Blind Rivets
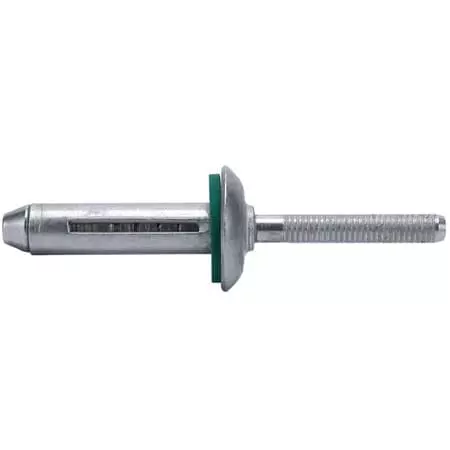