Home » 归档于 eric@world-rivet.com » 第4页
How to Measure Blind Rivet Grip Range?
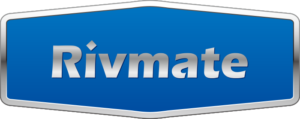
Rivmate Fastener
Top Rivet and Rivet Nut Manufacturer in China
Table of Contents
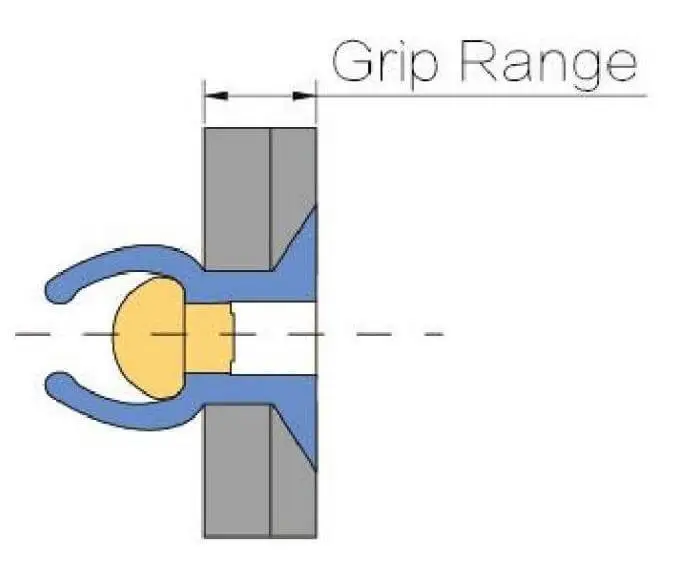
Blind rivet grip range and riveting results are closely related. By reading this guide, you will learn the basic definition of blind rivet grip range, its importance, measurement tools, and measurement procedures.
Table of Contents
What is the Blind Rivet Grip Range?
Blind Rivet Grip Range refers to the range of material thicknesses that a rivet can fasten. It represents the minimum and maximum material thicknesses that can be effectively joined by a blind rivet of a particular size.
For example, if a blind rivet has a Grip Range = 1.6mm – 4.8mm, then it can be used for material combinations with a total thickness between 1.6mm and 4.8mm.
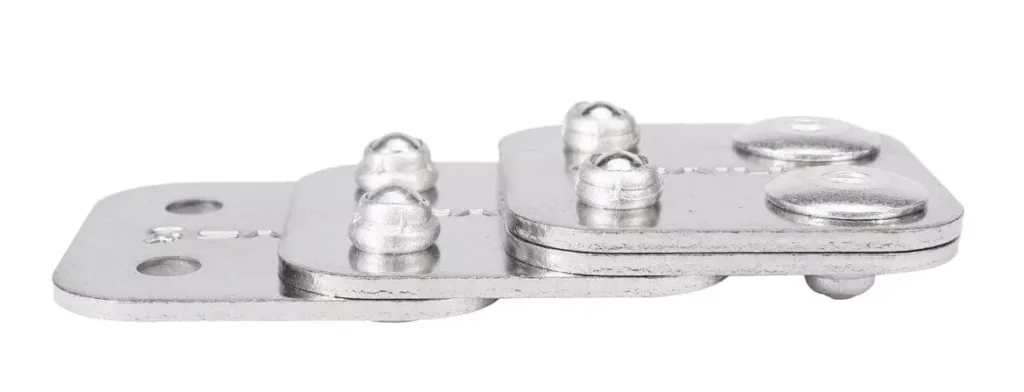
Why is it important to measure blind rivets grip range correctly?
Blind Rivet Grip Range is a critical factor in determining the quality of a riveted joint. Choosing the wrong Grip Range can result in loose rivets, weak joints or material damage. The right blind rivets grip range can bring the following irreplaceable benefits to your project or business:
- Ensure strong riveted links.
- Ensure that the rivet is fully functional to avoid connection failure.
- Increases the strength of the riveted joint and enhances tensile and shear resistance.
- Avoids material damage and increases service life.
- Reduce costs and improve riveting efficiency.
Tools Needed to Measure Blind Rivet Grip Range
Before you proceed to measure the blind rivet grip range, you need to prepare the following measuring tools:
- Caliper
- Steel Ruler
- Thickness Gauge
- Rivet Specification Chart
Do You Have Any Questions?
Let Us Solve Your Problem
Step-by-Step Guide: How to Measure Blind Rivet Grip Range
step1: Calculate the total thickness of the material
Grip Range refers to the range of material thicknesses that the rivet can fasten, so we need to first measure the sum of the thicknesses of all the materials to be joined.
- If it is a single layer material, use vernier calipers or thickness gauge to measure the material thickness.
- For multi-layer materials (e.g. metal + shim + composite), add up the thicknesses of all layers to calculate the overall thickness.
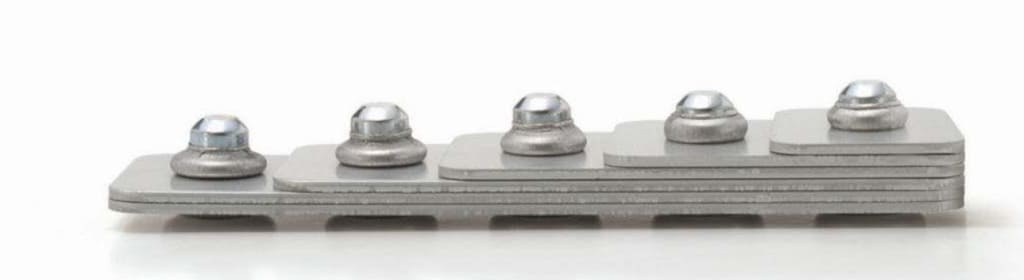
Example calculation:
Sheet metal = 1.5mm
Gasket = 0.5mm
Composite material = 2.0mm
Total thickness = 1.5mm + 0.5mm + 2.0mm = 4.0mm
You will need to select Grip Range to cover 4.0mm thick blind rivets.
step2: Precise measurements with measuring tools
Tool Name | Purpose | Applicable Situation |
Caliper | Precisely measures the thickness of metal, plastic, and other materials | High-precision requirements |
Thickness Gauge | Measures the thickness of thin sheet materials | Suitable for sheet metal, plastics |
Steel Ruler | Rough measurement of larger material thickness | Low-precision requirements |
Grip Range Specification Chart | Compares rivet specifications with material thickness | Selecting the correct rivet |
Measurement steps:
✔ Measure the thickness of the material using a vernier caliper, accurate to 0.1mm.
✔ If the surface of the material is uneven, measure multiple points and take the average value.
✔ If the material is multi-layer, measure layer by layer and totalize to calculate the total thickness.
step3: Selecting the Right Grip Range
After measuring the total material thickness, you will need to consult the rivet specification sheet. Select the Grip Range that will cover that thickness.
Grip Range Selection Example:
Total material thickness(mm) | Recommended Grip Range(mm) | Recommended Rivet Length(mm) |
0.5 – 1.5mm | 0.5 – 2.0mm | 4 – 5mm |
1.6 – 3.2mm | 1.6 – 4.0mm | 6 – 8mm |
3.2 – 4.8mm | 3.2 – 5.0mm | 8 – 10mm |
4.8 – 6.4mm | 4.8 – 7.0mm | 10 – 12mm |
It is important to ensure that the Grip Range fully covers the material thickness to avoid using rivets that are too short or too long.
- Example 1: If the total measured material thickness is 3.8mm, a rivet with Grip Range = 1.6mm – 4.8mm can be selected.
- Example 2: If the total thickness is 6.2mm, select rivets with a Grip Range = 4.8mm – 7.0mm.
Do You Have Any Questions?
Let Us Solve Your Problem
The Relationship Between Blind Rivets Grip Range and Rivet Body Lengths
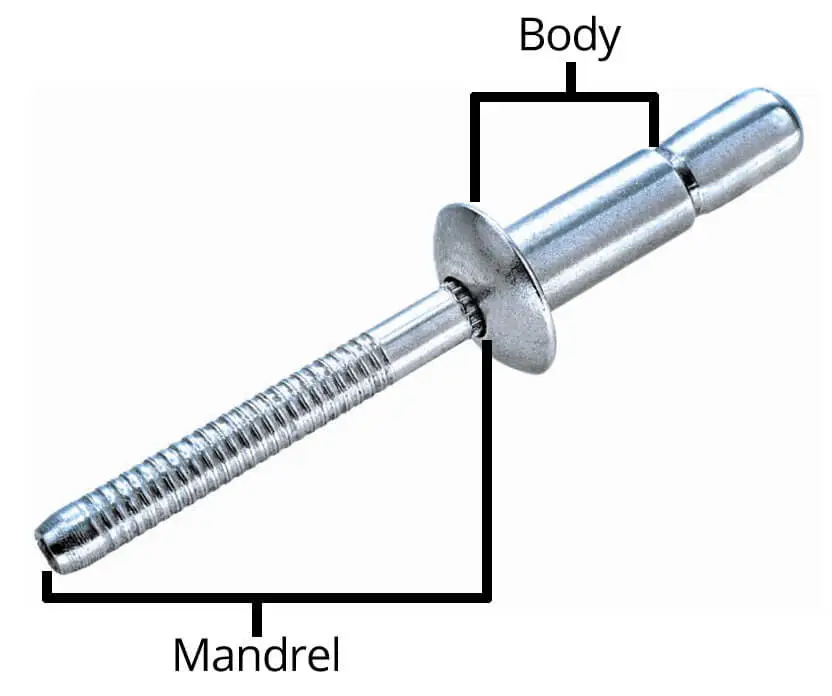
The blind rivet grip range is determined by the rivet body length and rivet type. Typically, the rivet length is > Grip Range so that the end of the rivet has enough material to expand to form the head.
Grip Range (mm) | Recommended Rivet Length (mm) |
0.5 – 2.0mm | 5 – 6mm |
1.6 – 4.0mm | 6 – 8mm |
3.2 – 5.0mm | 8 – 10mm |
4.8 – 7.0mm | 10 – 12mm |
6.4 – 9.5mm | 12 – 16mm |
Typically, the rivet length is approximately 1.5 – 2 times the upper limit of the Grip Range to ensure proper deformation of the rivet.
Common Mistakes When Measuring Blind Rivet Grip Range
1. Neglecting total material thickness calculation errors
Common error:
- Failure to calculate the total thickness of all materials and measuring the thickness of only one of the layers.
- Thickness of shims, coatings, or adhesives are ignored, resulting in the Grip Range selected being too short.
- Inconsistent thickness measurements in different areas, not averaged.
Use vernier calipers or a thickness gauge to accurately measure the thickness of each layer of material and total all layers. Note the need to include any additional spacer layers (e.g., coatings, glues, sealing gaskets, etc.) to ensure that the proper Grip Range is selected.To minimize errors, take measurements at multiple points and average the values to minimize errors.
2. Ignore Grip Range vs. Rivet Length
In practice, the rivet body is larger than the grip range. If the Grip Range is mistakenly assumed to be equal to the length of the rivet, the tail of the rivet will not expand sufficiently.
So when choosing the right rivets for your business, you need to use the recommended grip range with the rivet length against the photo to avoid problems.
3. Choosing the wrong type of rivet
For the vast majority of rivets, all of the above applies. However, there is one particular type of blind rivet — multi grip blind rivets — that is not applicable.
Multi grip blind rivets are blind rivets with a wide grip range and can be riveted to a wide range of thicknesses. Typically, multi grip blind rivets of the same size can be riveted to a wide range of thicknesses.
Custom Blind Rivet Grip Range for your Project
By reading this guide, I’m sure you’ve got a basic understanding of the blind rivets grip range. If you don’t know how to meaure blind rivets grip range or want to customize special blind rivet grip range, please contact us!
Rivmate is a top rivet manufacturer in China, which can well meet your customization needs.
Get Rivets Quote
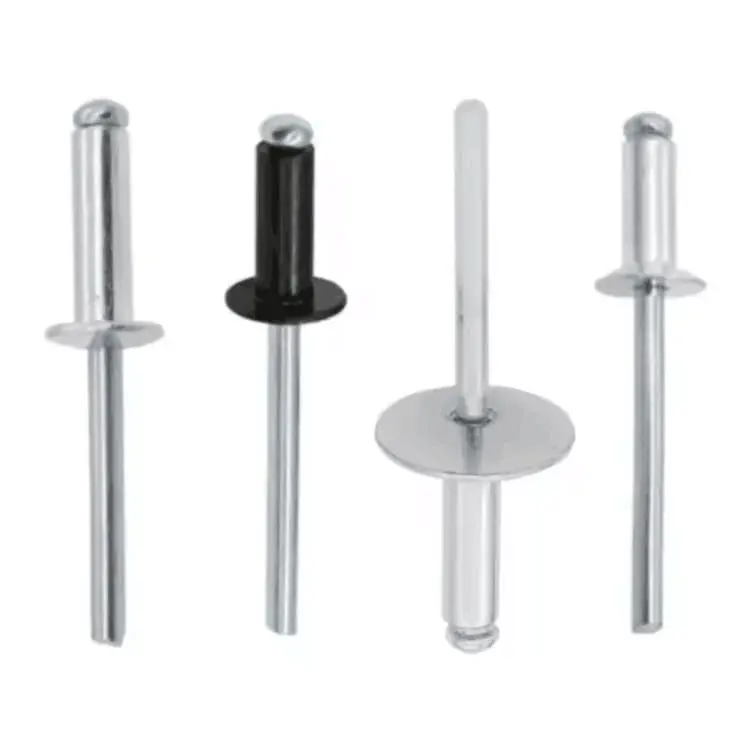
Buy Open Type Blind Rivets
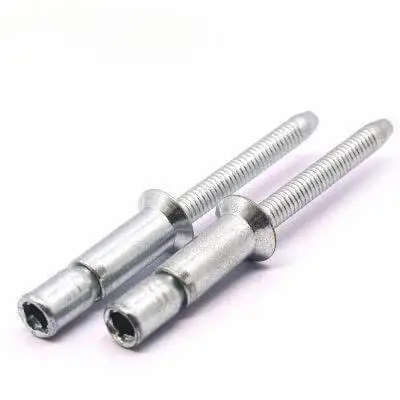
Buy Structural Blind Rivets
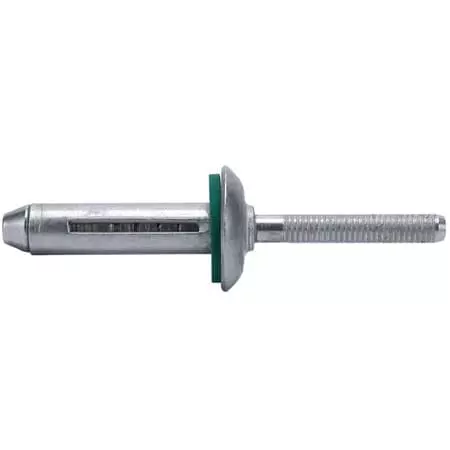